FLUID, an open-source, 3D-printed robot, offers an affordable and customizable solution for automated material synthesis, making advanced research accessible to more scientists.
The open-source robotic system FLUID (Flowing Liquid Utilizing Interactive Device) in operation. (Keisuke Takahashi)
A team of researchers led by Professor Keisuke Takahashi at the Faculty of Science, Hokkaido University, have created FLUID (Flowing Liquid Utilizing Interactive Device), an open-source robotic system constructed using a 3D printer and off-the-shelf electronic components.
To demonstrate FLUID's capabilities, the team used the robot to automate the co-precipitation of cobalt and nickel, creating binary materials with precision and efficiency. "By adopting open source, utilizing a 3D printer, and taking advantage of commonly-available electronics, it became possible to construct a functional robot that is customized to a particular set of needs at a fraction of the costs typically associated with commercially-available robots," said Mikael Kuwahara, the lead author of the study.
FLUID's hardware comprises four independent modules, each equipped with a syringe, two valves, a servo motor for valve control, and a stepper motor to precisely control the syringe plunger. Each module also has an end-stop sensor to detect the syringe's maximum fill position. These modules are connected to microcontroller boards that receive commands from a computer via USB. The system also includes software that lets users control the robot's functions, such as valve adjustments and syringe movements and provides real-time status updates and sensor data.
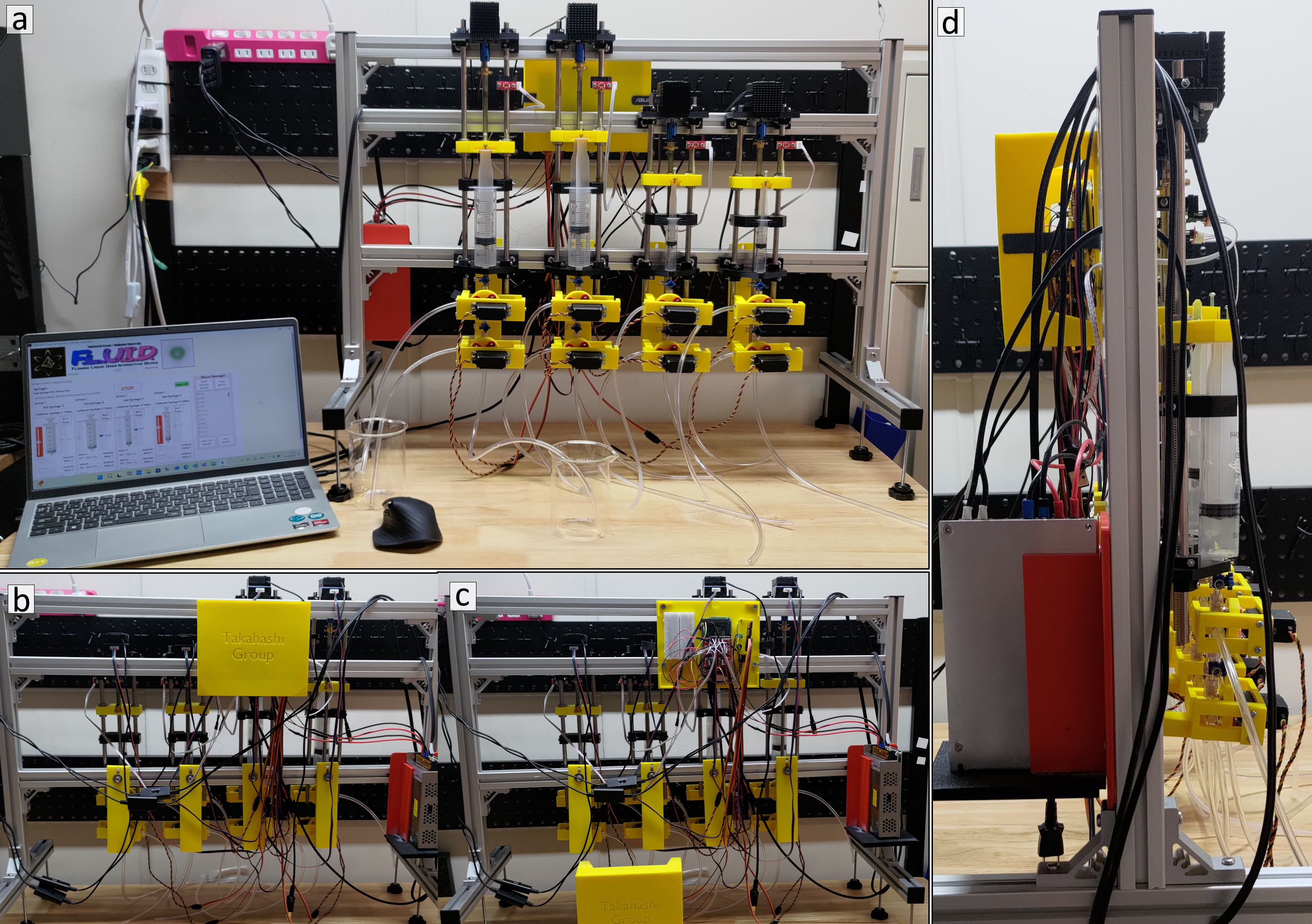
Different views of the FLUID (Flowing Liquid Utilizing Interactive Device) open-source robotic system: (a) front view; (b) rear view; (c) rear view with the wiring of the control circuit exposed; and (d) side view. (Mikael N. Kuwahara, et al. ACS Applied Engineering Materials. April 9, 2025)
The researchers have made the design files openly available so researchers anywhere in the world can replicate or modify the robot according to their specific experimental needs. By providing an open-source and 3D-printable alternative to expensive commercial robots, FLUID could enable a broader community of researchers to engage in automated experimentation in material science.
This could be particularly beneficial for researchers in resource-limited settings or for scientists focusing on niche areas where commercial solutions may not be readily available or cost-effective. With a customizable design that can be printed using commercial components, they can conduct sophisticated experiments without significant capital investment.
"This approach aims to democratize automation in material synthesis, providing researchers with a practical, cost-effective solution to accelerate innovation in materials science," Takahashi explained.
Looking ahead, the researchers plan to integrate additional sensors to monitor other parameters, such as temperature and pH. These will expand the robot's ability to handle a wider variety of chemical reactions, including polymer mixing and organic synthesis. The software will also be further developed to include features like macro recording to streamline repetitive tasks and enhanced data logging to improve experimental reproducibility and data analysis.
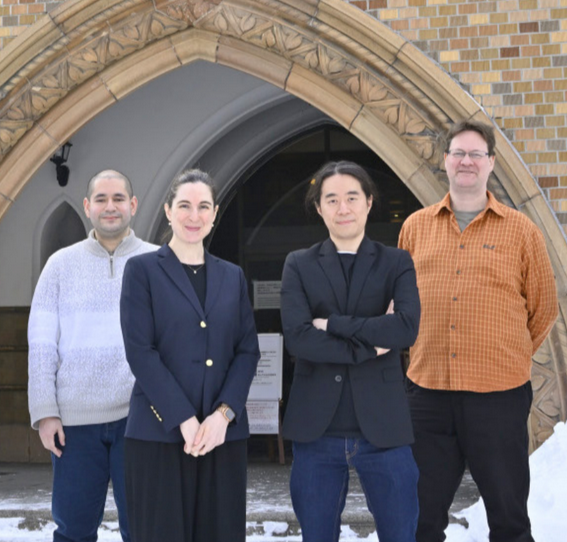
(from left) Fernando Garcia-Escobar, Lauren Takahashi, Keisuke Takahashi and Mikael N. Kuwahara of the research team.
Original Article:
Mikael N. Kuwahara et al. Development of an Open-Source 3D-Printed Material Synthesis Robot FLUID: Hardware and Software Blueprints for Accessible Automation in Materials Science. ACS Applied Engineering Materials. April 9, 2025.
DOI: 10.1021/acsaenm.5c00084
Funding:
This work is funded by the Japan Science and Technology Agency (JST) ERATO (JPMJER1903), PRESTO (JPMJPR24T5), and JST Mirai Program (JPMJMI22G4); Japan Society of the Promotion of Science (JSPS) KAKENHI Grant-in-Aid for Scientific Research (B; JP23H01762, 24K01241).