A machine that recognises and removes weeds, a robot that cuts and picks ripe fruit with arm grippers or a greenhouse that autonomously controls the climate. This is all in a day's work for WUR researchers Bram Veldhuisen and Anja Dieleman, who are involved in the development and implementation of these smart AI technologies. This makes the agricultural and horticultural sectors more sustainable, improves their yields and makes them less labour-intensive. We asked them about promising solutions, the hurdles to overcome and the potential risks.
Artificial Intelligence (AI) offers solutions for agriculture and horticulture in several areas, says Bram Veldhuisen, researcher in precision agriculture and agri-robotics. "Like recognising weeds or harvesting crops. You can train a machine to distinguish between a potato plant and weeds, for example, or to know when a crop is ripe and ready to be harvested. This is obviously very convenient because doing all that manually - as is mostly the case now - is extremely time and energy consuming. Moreover, it's easy to overlook things with the naked eye. Smart systems equipped with high-tech cameras and sensors can detect more."
Smart implements
One of the challenges is how to ensure that these smart systems are also - almost - 100 percent reliable. Smart implements are the missing link here, says Veldhuisen. "This is an integrated system in a machine or robot that has the ability to check its own work. If you send a robot into the field to clear weeds, you don't want it to accidentally take some of the crops too. And if you want to harvest, then you only want to remove the ripe crops from the field. A smart implement knows whether the work is going well or whether someone needs to intervene or make an adjustment."
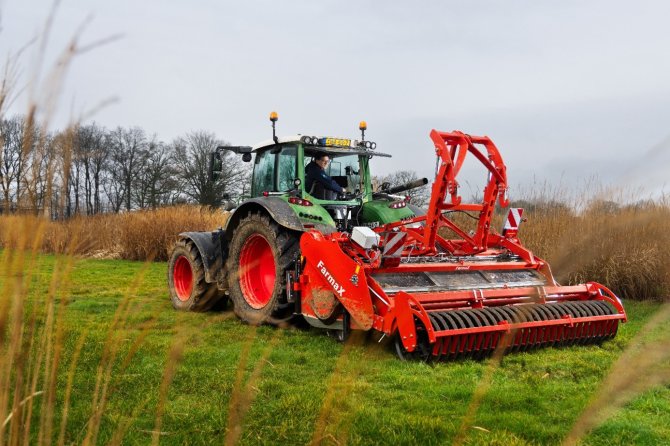
Signal if something goes wrong
Smart implements are not yet applied in practice, says Veldhuisen. "At WUR, we are working on developing this, including in Robs4Crops. In this project, we developed a camera system for a hoeing machine in a beet field. This allows the machine to look ahead and behind, counting the number of crop plants coming up and behind it. If there's a mismatch between these numbers, the machine gives a signal, so the farmer knows something has gone wrong. You could also develop such a system for the sowing process. For every type of machine, it is therefore possible to devise control steps that are currently still carried out by humans."
Smart harvesting and picking robots
In other projects, WUR researchers are working on another application of AI technology, namely smart harvesting robots. Veldhuisen: "A few years ago, we developed a harvesting robot for broccoli. We fitted the robot with a camera system that sees very precisely which broccoli is ripe enough. Similar applications have been developed in other crops, such as a harvesting robot for peppers. WUR is also working on another project, The Next Fruit 4.0, which focuses on fruit growing. This also looks at picking robots. Developing these is slightly more challenging because you need to be even more careful with fruit than with other crops. When picking an apple or pear, it should be twisted rather than pulled or cut. You also want to avoid any bruising.
Autonomous cultivation in greenhouse horticulture
AI is not only playing an increasingly large role in arable farming but also in protected cultivation, like greenhouse horticulture. Particularly when it comes to autonomous cultivation, says Anja Dieleman, researcher in the field of plant physiology. "Autonomous cultivation is about remotely controlling cultivation in a greenhouse. This is done using information from sensors and cameras relating to greenhouse climate, plant development or the presence of diseases and pests, for example. With the development of smart models, growers can use this information to make decisions. Should the temperature be higher or lower? Do I need to give extra water? When can I harvest? Do I need to use crop protection products?"
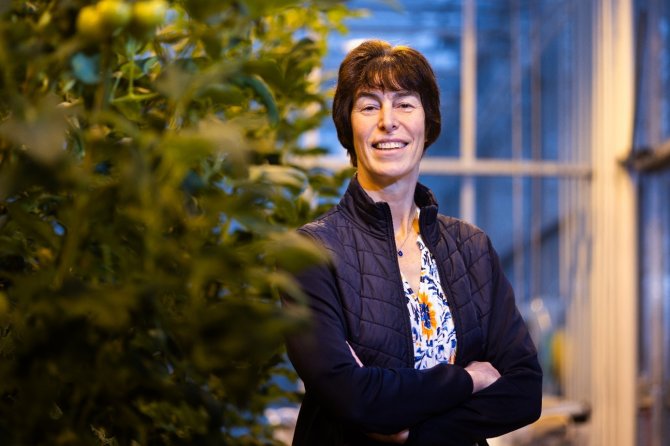
Intelligent algorithms and digital twins
Dieleman is project leader of AGROS, in which WUR is working with a consortium of companies to develop an autonomous greenhouse. "We have now reached part 2 of the project, AGROS II. In AGROS I, the work included developing good vision technology in the greenhouse. In part 2, this will be elaborated further, including a mobile camera system that moves through the greenhouse. This enables us to measure the development of a large number of plants, allowing us to control cultivation more effectively. "We do the control using intelligent algorithms and digital twins based on mechanistic models. This is how we make autonomous cultivation even smarter."
Level is getting higher
However, we are not yet at the point where we can control a greenhouse completely autonomously, says Dieleman. "We are now at the level where data and intelligent algorithms mainly support growers in their decisions. Particularly in the field of autonomous climate control, the sector is already quite advanced. Controlling autonomous crop management is trickier. For example, determining the right time to irrigate, space plants and harvest ripe fruits. That requires crop feedback. And that's where the challenge lies. Although there are good sensors on the market for continuously measuring greenhouse air temperature, for example, there are none that automatically determine the daily number of newly formed leaves. We are now developing vision technology for that. But even if we can't control a greenhouse completely autonomously, these developments help to improve greenhouse cultivation. Because we are working on this, growers are becoming more aware of the importance of data collection and cultivation plans. This will automatically raise the level of cultivation."
Practice stands to gain
Both Dieleman and Veldhuisen see that farmers and growers are eager to make more use of smart technology. Veldhuisen: "Not just because it improves their yields, but also because of the issues around labour supply. Fewer and fewer people want to do intensive work in the field. Smart machines offer a solution to that problem. We are also seeing an increasing awareness of issues such as climate and the environment. By making smarter use of energy, water and nutrients and replacing chemical control with more environmentally friendly methods, such as laser weeding, operations have a less harmful impact. Now it's just a matter of ensuring technology maturity and practical accessibility."

More autonomy not without risks
Finally, experts emphasise that introducing more autonomous technology is not without risks. Dieleman: "If you want to control a crop remotely, you need to be able to rely on the data. If a hose is loose or a well is blocked, the numbers are no longer correct. To avoid such problems, you need to incorporate an extra check." Veldhuisen: "Another issue that arises when you start working more digitally is the risk of cybersecurity threats. If someone with the wrong intentions hacks your system, they could set the machine to destroy all your plants. And you need to ensure that autonomous machines move around safely. In that respect, we can follow the development of self-driving cars. But first, let's prove that everything we want now actually works."