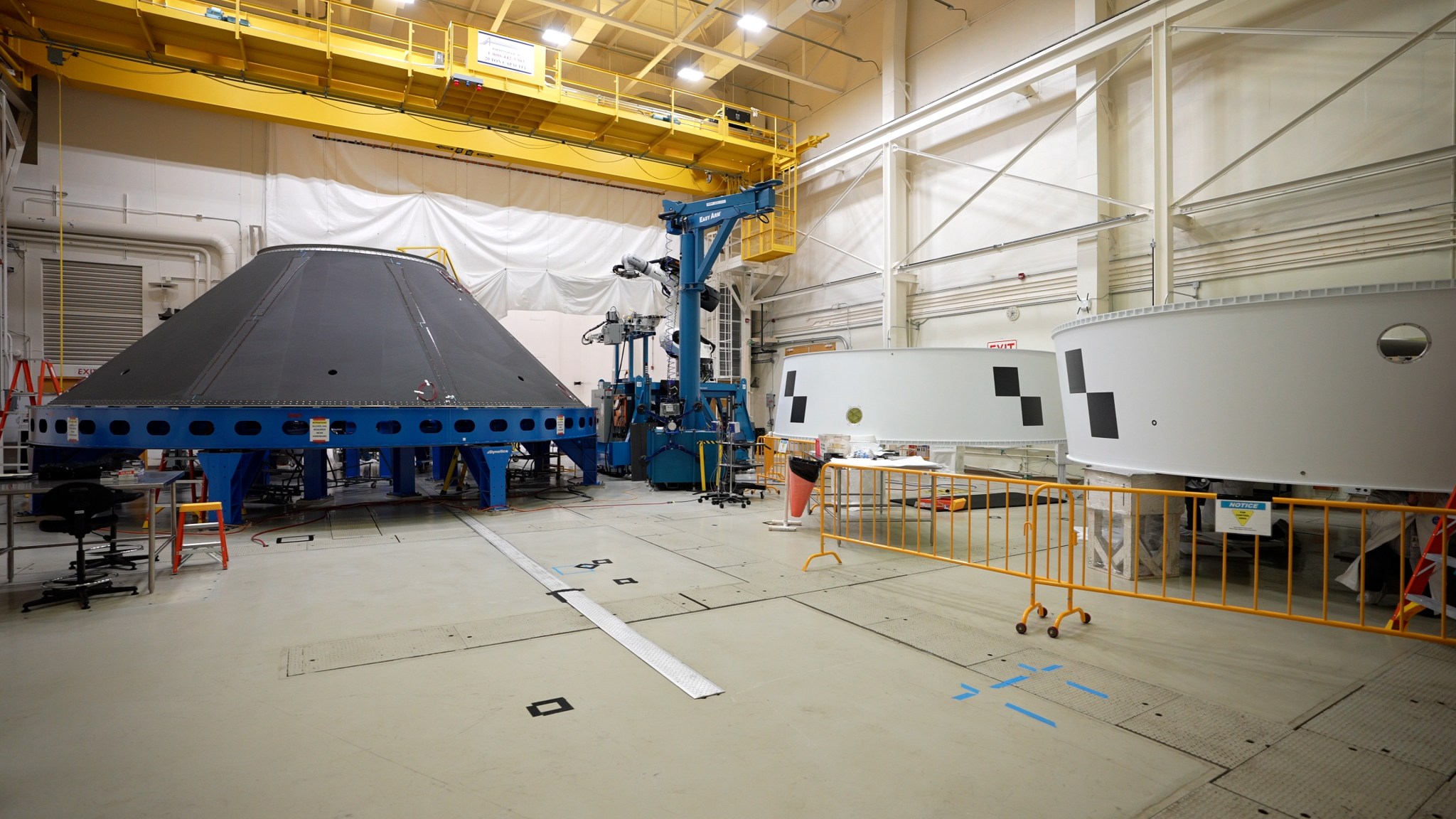
A test version of the SLS (Space Launch System) rocket's payload adapter is ready for evaluation, marking a critical milestone on the journey to the hardware's debut on NASA's Artemis IV mission.
Comprised of two metal rings and eight composite panels, the cone-shaped payload adapter will be part of the SLS Block 1B configuration and housed inside the universal stage adapter atop the rocket's more powerful in-space stage, called the exploration upper stage. The payload adapter is an evolution from the Orion stage adapter used in the Block 1 configuration of the first three Artemis missions that sits at the topmost portion of the rocket and helps connect the rocket and spacecraft.
"Like the Orion stage adapter and the launch vehicle stage adapter used for the first three SLS flights, the payload adapter for the evolved SLS Block 1B configuration is fully manufactured and tested at NASA's Marshall Space Flight Center in Huntsville, Alabama," said Casey Wolfe, assistant branch chief for the advanced manufacturing branch at Marshall. "Marshall's automated fiber placement and large-scale integration facilities provide our teams the ability to build composite hardware elements for multiple Artemis missions in parallel, allowing for cost and schedule savings."
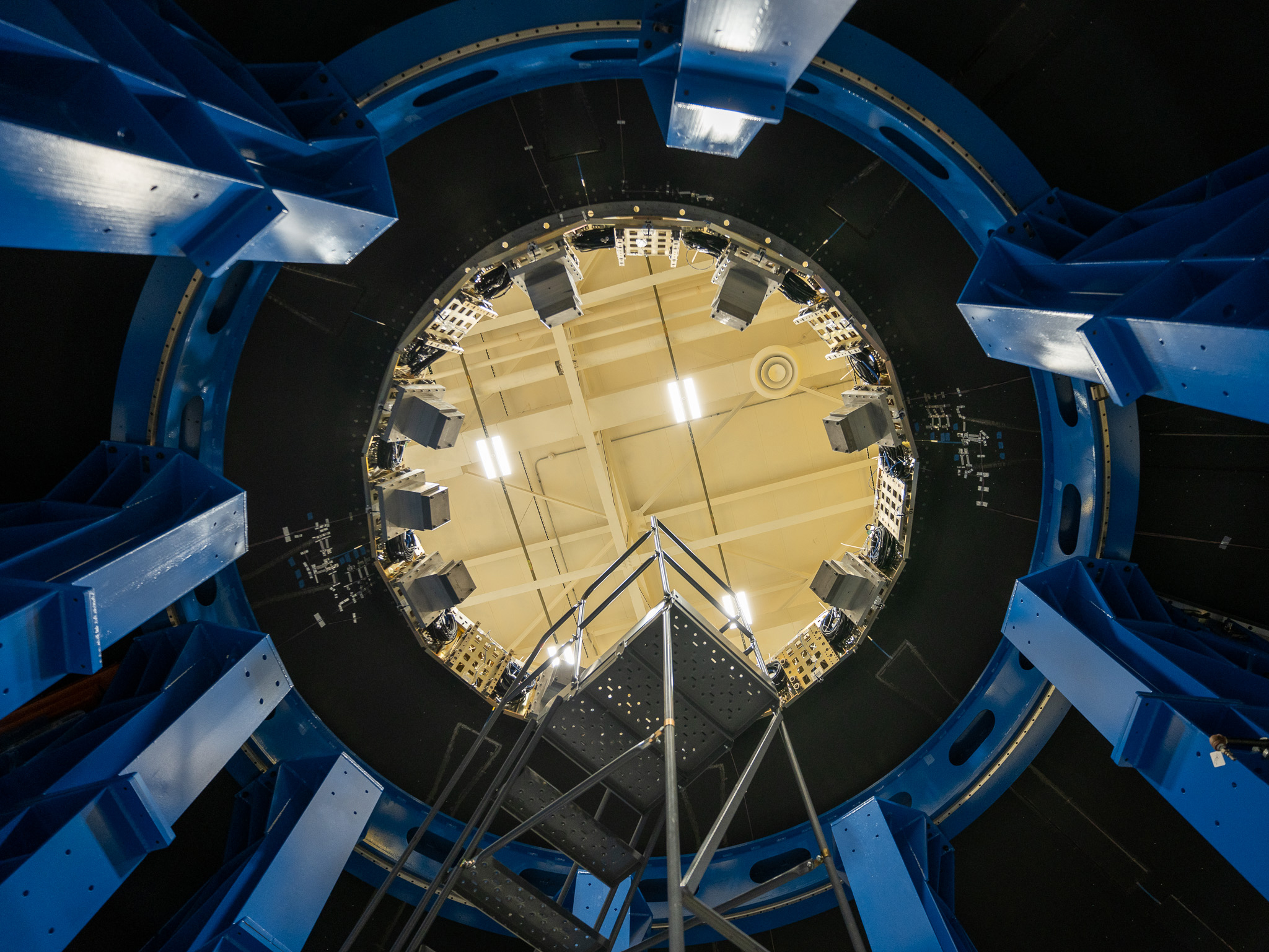
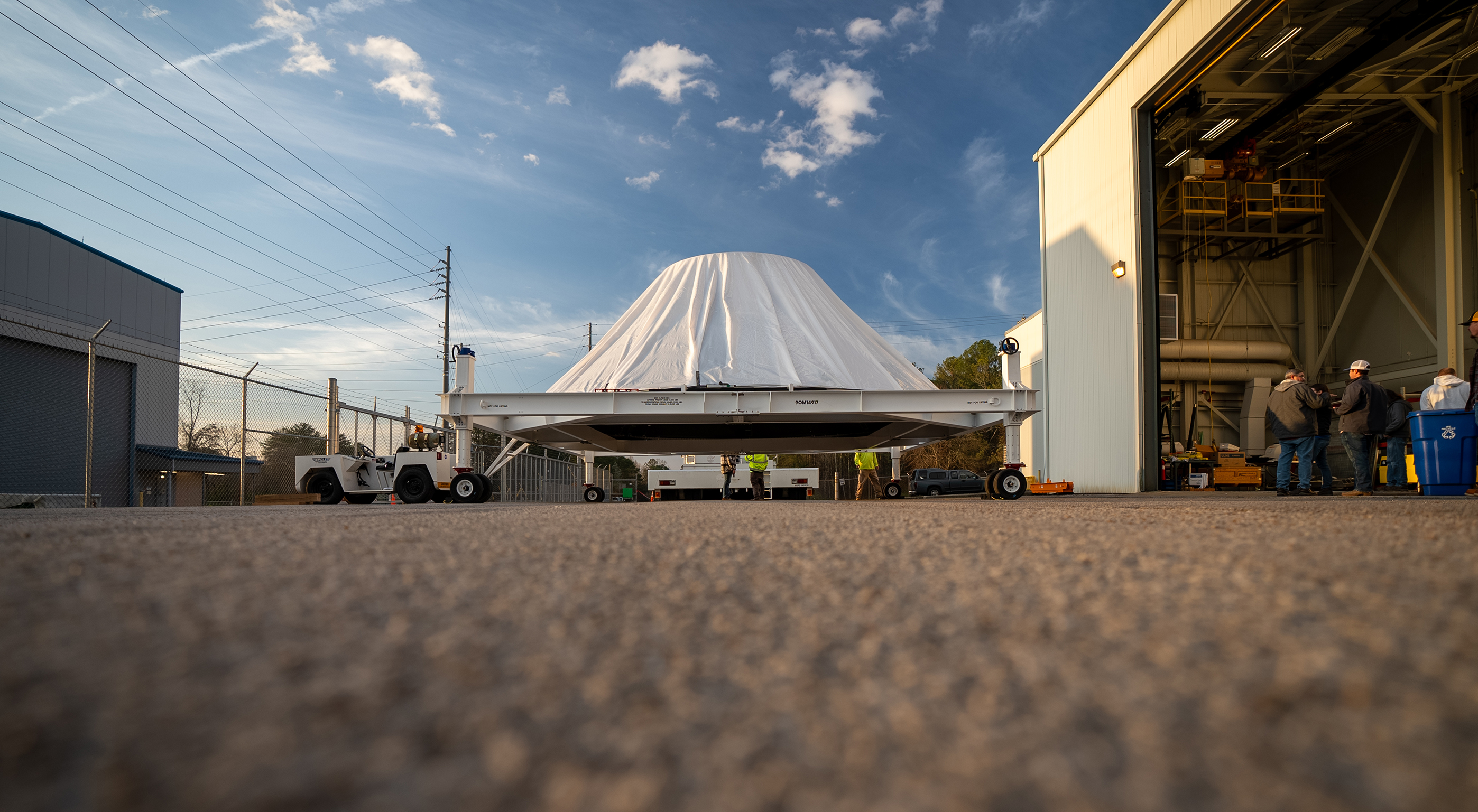
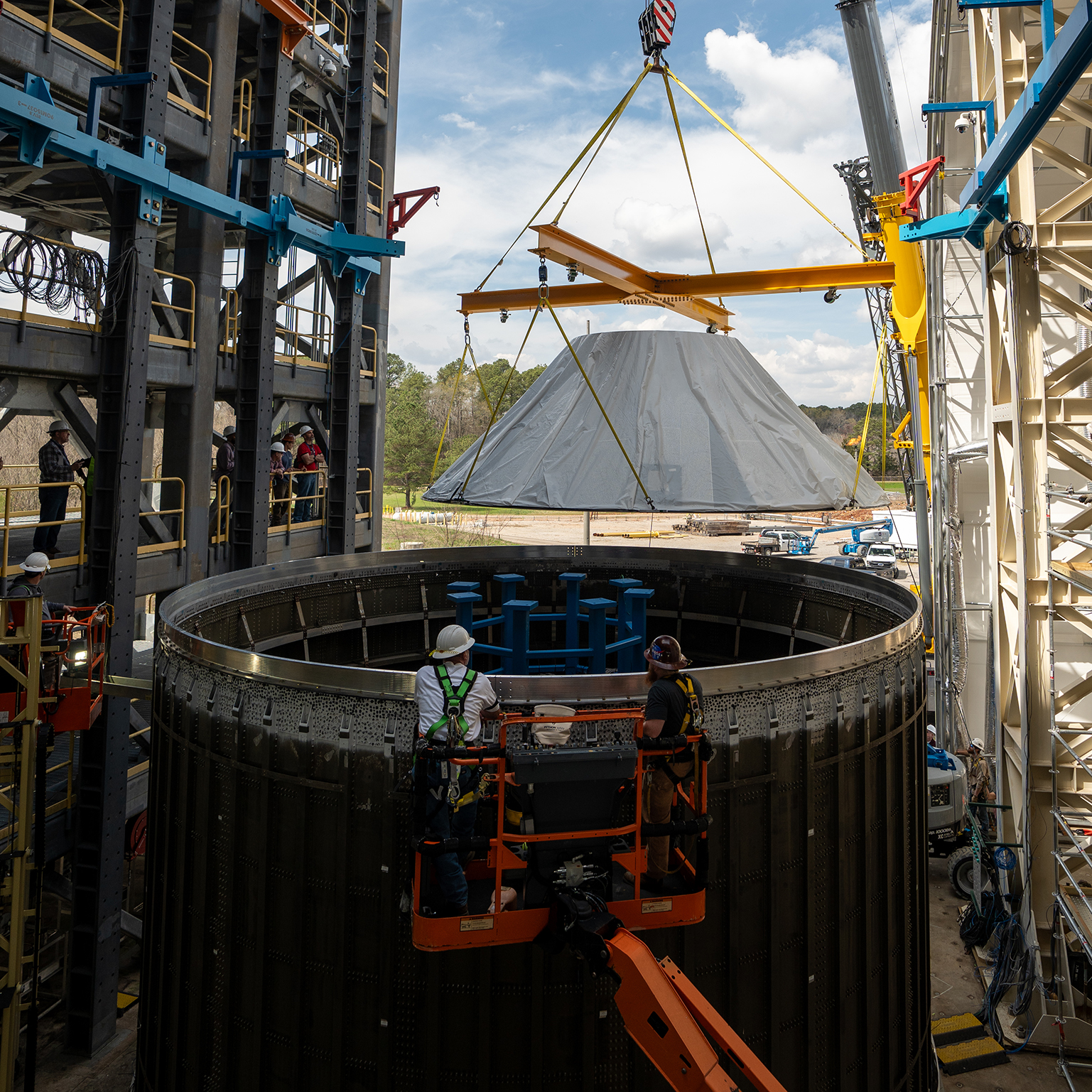
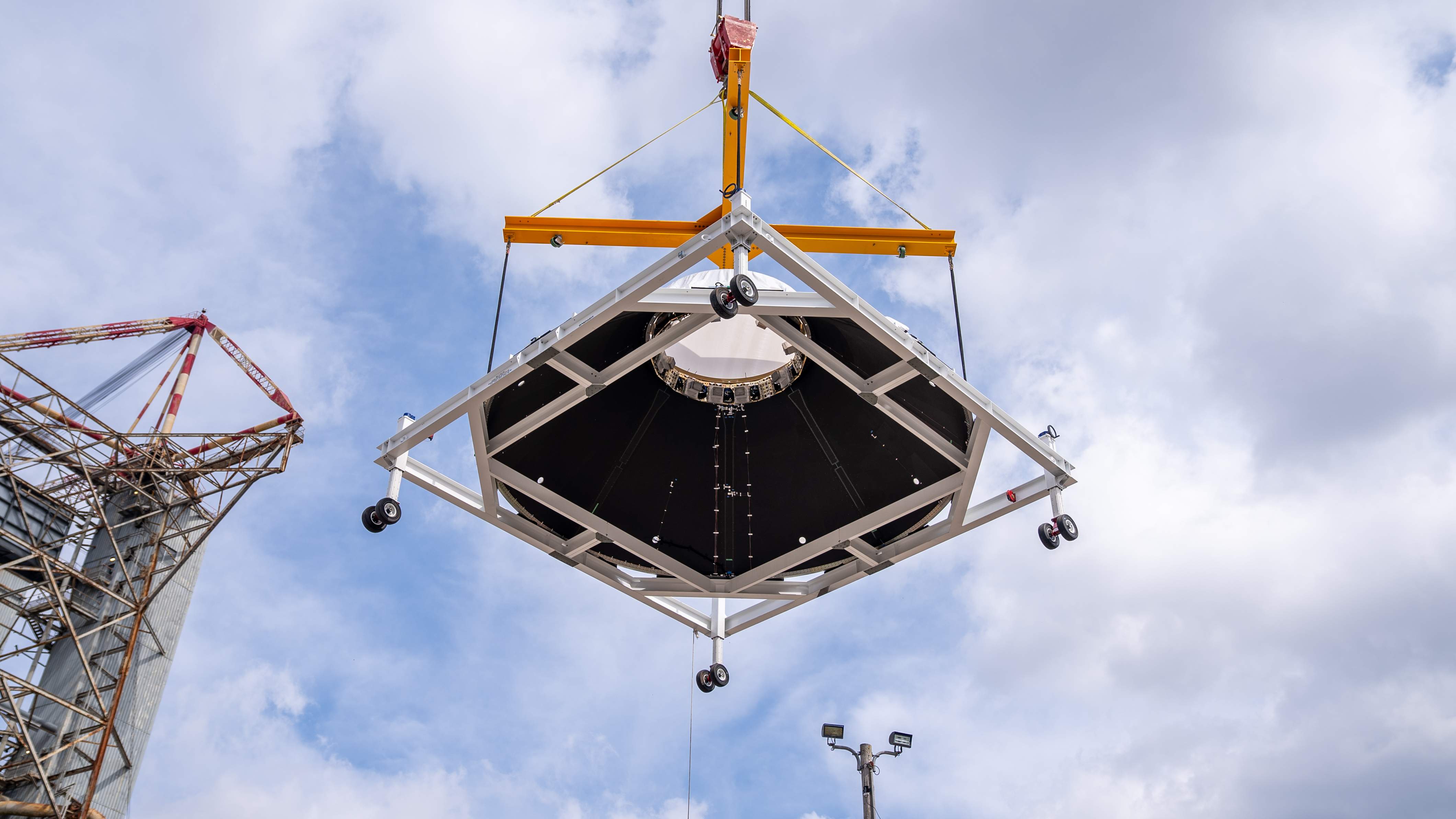
At about 8.5 feet tall, the payload adapter's eight composite sandwich panels, which measure about 12 feet each in length, contain a metallic honeycomb-style structure at their thickest point but taper to a single carbon fiber layer at each end. The panels are pieced together using a high-precision process called determinant assembly, in which each component is designed to fit securely in a specific place, like puzzle pieces.
After manufacturing, the payload adapter will also be structurally tested at Marshall, which manages the SLS Program. The first structural test series begins this spring. Test teams will use the engineering development unit - an exact replica of the flight version of the hardware - to check the structure's strength and durability by twisting, shaking, and applying extreme pressure.
While every Block 1B configuration