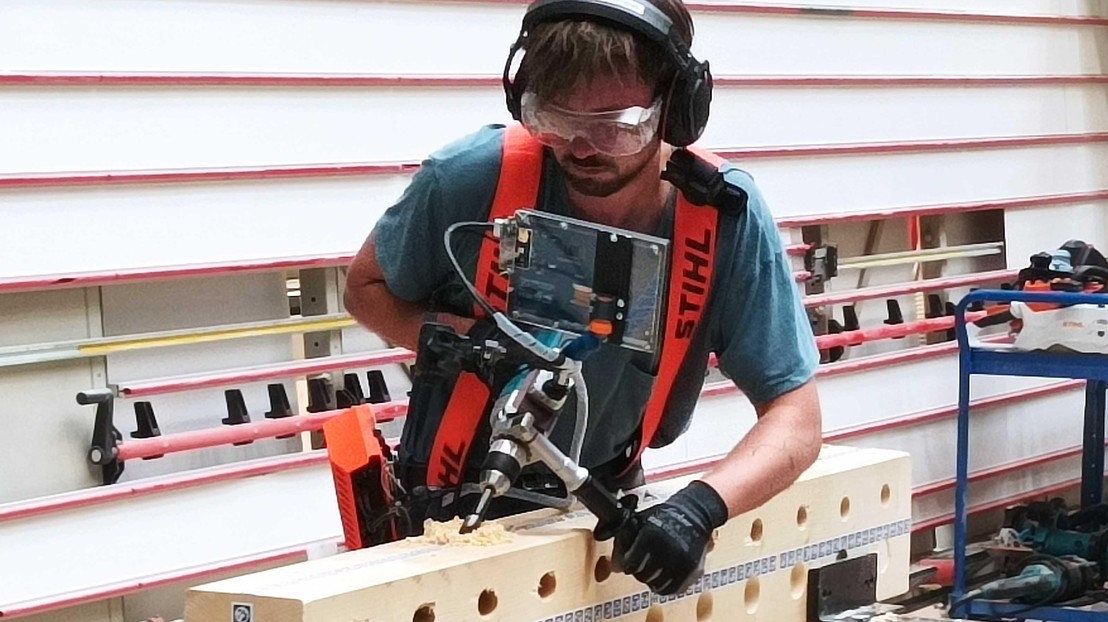
The operator sees the instructions through colored lines on the screen. © 2024 Andrea Settimi
A system developed at EPFL uses augmented reality (AR) to help carpenters make extremely precise timber cuts without having to measure or mark up beams. Its hybrid approach stands to make digitally assisted technology affordable for small businesses, woodworkers and construction professionals in developing countries.
Timber is an increasingly popular construction material thanks to its low environmental impact, carbon storage capacity, potential for fast assembly and excellent insulation properties. Growing demand for timber structures, coupled with technological advancements, has led many producers to automate their processes over the past 20 years. Today we can find sophisticated robots in their workshops - machines that are as impressive as they are expensive, equipped with articulated arms and precision cutters to carry out repetitive yet complicated tasks.
At EPFL, engineers have developed an AR-based system called Augmented Carpentry that could put paid to the stereotype of a carpenter working with a pencil in one hand and a tape measure in the other. Available in open source, the system is a first step towards a hybrid process that combines the dexterity of humans with the reliability of computer processing. Augmented Carpentry is poised to make digitally assisted timber-cutting methods affordable for small businesses, woodworkers and construction professionals in developing countries.
Our system includes feedback in real time. If the woodworking tool or the beam it's cutting slips, for example, the virtual overlay will remain aligned with the actual piece of timber so that operators can instantly see how to adjust their movements.
An augmented working space
The system is the result of four years of research, development and testing by Andrea Settimi - an EPFL PhD student whose thesis is being supervised jointly by Julien Gamerro, former post-doctoral fellow, and Yves Weinand, head of EPFL's Laboratory of Timber Construction (IBOIS) - along with several other project participants. It's capable of producing holograms with sub-millimeter precision to guide human operators. The physical device consists of a screen that displays a virtual workspace overlying actual pieces of timber. Lines of different colors give numerous indications: how to position the tool, how deep to drill, what the right cutting angle is, how long a cut should be and so on. They enable operators to work in a way that's both intuitive and precise. "Our system includes a detection mechanism and integrated sensors that give feedback in real time," says Settimi. "If the woodworking tool or the beam it's cutting slips, for example, the virtual overlay will remain aligned with the actual piece of timber so that operators can instantly see how to adjust their movements."
To achieve such a high degree of precision, the research team studied various aspects of computer-vision technology and painstakingly integrated them into its device so that it could incorporate the woodworking tool as well as the specific piece of timber and woodworking plan. They scanned and generated 3D computer models of commonly used tools, creating a vast database. To use the system, operators first scan their timber pieces by lot, enabling the program to record the details of each one. Then the operators place markers randomly on the timber pieces so that the system can detect their orientation and position. The last step is to upload the woodworking plans, which are integrated directly into the program in 3D and displayed in augmented reality.
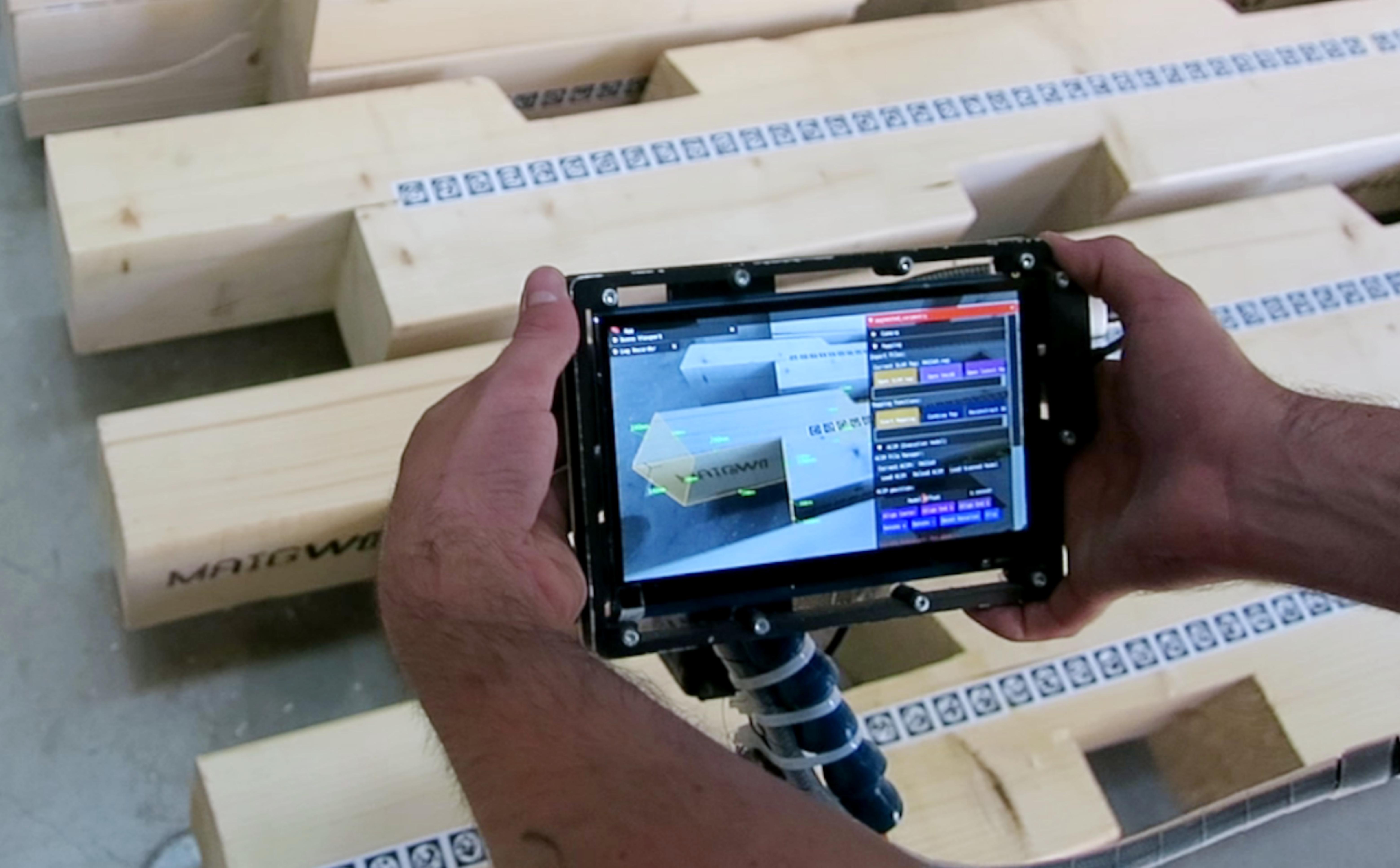
so that the system can detect their orientation and position © 2024 A. Settimi
Thanks to the use of computer vision and sensors, standard woodworking tools can become smart devices capable of guiding users in real time. The system visualizes cutting lines directly on a beam, for instance, showing operators exactly where to guide the saw. This significantly reduces the risk of human error and improves precision during assembly.
Recognizing beams and tools in cluttered workshops
A key part of the research project was to develop advanced computer vision methods for detecting items and positioning the camera in complex, cluttered spaces like workshops. These spaces generally contain various types of objects - other pieces of wood, tools, panels, etc. - scattered about in no particular order, making it hard for computer vision systems to map the environment. The research team worked with EPFL's Center for Imaging to develop programs that could accurately recognize and locate the items of interest - in this case, woodworking tools and timber pieces. Such capabilities have never before been implemented at this scale for timber construction and are essential for making sure the virtual workspace aligns with the physical reality.
Digitally assisted, manual construction methods that are local and resilient
Thanks to Augmented Carpentry, even small businesses and woodworkers can create intricate shapes and designs - a task until now reserved for costly robots. "Another benefit of our AR system is that it takes advantage of human capabilities, even when operators have little training, to quickly digitize construction processes," says Settimi. Human dexterity and cognition are enhanced by machine precision, in a good example of a hybrid approach. "By leveraging the potential of human-machine collaboration for modern carpentry and the design of timber structures, Augmented Carpentry can ensure human operators remain involved in the process, thus promoting construction methods that are digitally assisted, local and socially responsible," he says.