Hydrogen, the smallest element in the universe, has huge potential as a clean energy source. Using hydrogen (H2) as a fuel and as a means of storing energy could reduce our dependence on petroleum and help us reduce air pollution and greenhouse emissions to meet our goals for a cleaner and better climate. However, adopting hydrogen power on a large scale requires advances in technology and the creation of new infrastructure. Scientists at Lawrence Berkeley National Laboratory (Berkeley Lab) are leading local and national projects aimed at optimizing all stages of the hydrogen energy lifecycle, from engineering technologies for cost-effective and environmentally friendly production of hydrogen gas all the way to developing efficient hydrogen fuel cells.
Here's a round-up of our current focus areas encompassing hydrogen production, storage, usage, and analysis, to enable a carbon-free future.
1. Electrolysis: carbon-free fuel from water
Traditionally, the most common method for generating H2 has been from reforming natural gas at petroleum refineries. But electrolysis, the process of producing hydrogen gas by splitting water molecules using electricity and catalysts, is growing in popularity as we transition away from fossil fuels toward renewable energy sources. And since hydrogen does not produce carbon dioxide when burned in a combustion engine or fed into a fuel cell, when you power electrolyzers with renewable electricity, the resulting hydrogen fuel is a near-zero carbon energy source.
Methods for electrolysis have existed for decades, but the approach hasn't been widely adopted on a commercial scale due to high capital costs and the cost of electricity required. Berkeley Lab scientists are working to develop multiple electrolysis technologies as part of a multi-lab consortium Hydrogen from Next Generation Electrolyzers of Water (H2NEW). The consortium's goals are to enable manufacturable electrolyzers that can lower the cost of hydrogen to $2/kg by 2025, in order to compete with hydrogen generated from natural gas.
One team is working on efficient high-temperature electrolysis systems that use the heat generated as a byproduct of industrial processes such as cement and ammonia production, or excess heat from solar thermal and nuclear power plants, as energy to help drive the water-splitting reaction.
Other researchers are pursuing low-temperature proton exchange membrane (PEM) electrolysis, which works at temperatures less than 100 degrees Celsius (212 degrees Fahrenheit), allowing them to be paired with renewable electricity sources like wind and solar. Low-temperature PEM electrolysis technologies are more developed, and constitute a large proportion of the electrolyzers planned for deployment. Unfortunately, these devices require iridium - one of the rarest elements on Earth - in the electrode catalyst that breaks hydrogen protons off from the H2O molecule and forms O2 from the newly single oxygen atoms.
"When lots of iridium is used, as in commercial electrolyzers today, everything works and the systems are highly durable," said Rangachary Mukundan, a senior scientist in the Energy Technologies Area (ETA) with decades of experience studying fuel cells and electrolyzers. But, he noted, when you try to reduce the amount of iridium to lower costs, "you start seeing durability issues. The performance is no longer that stable due to the iridium dissolving over time and moving into the membrane from the catalyst layer."
Xiong Peng, a research scientist in the Energy Conversion Group within ETA, is part of a team seeking to address this issue by redesigning the electrolyzer's porous transport layer (PTL) - the material between the catalyst and the flow field, which is where the water flows through the cell. Recent research shows that modifying the porous nanostructure of this layer through laser ablation improves the contact of the PTL with the electrode and thereby performance.
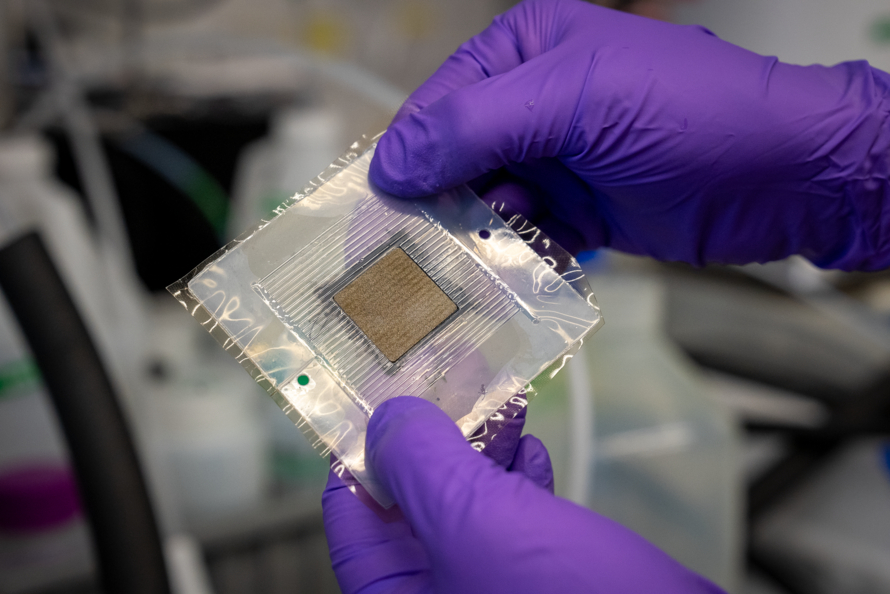
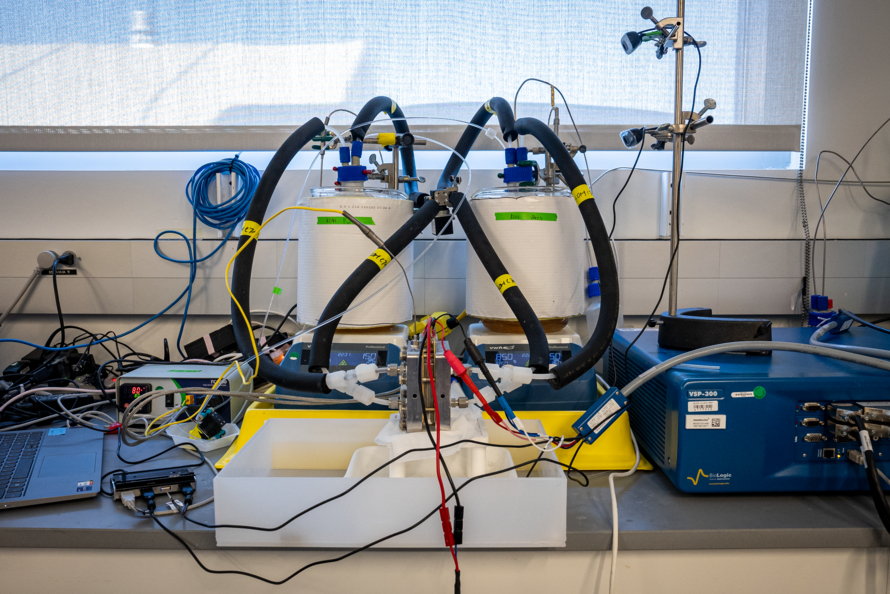
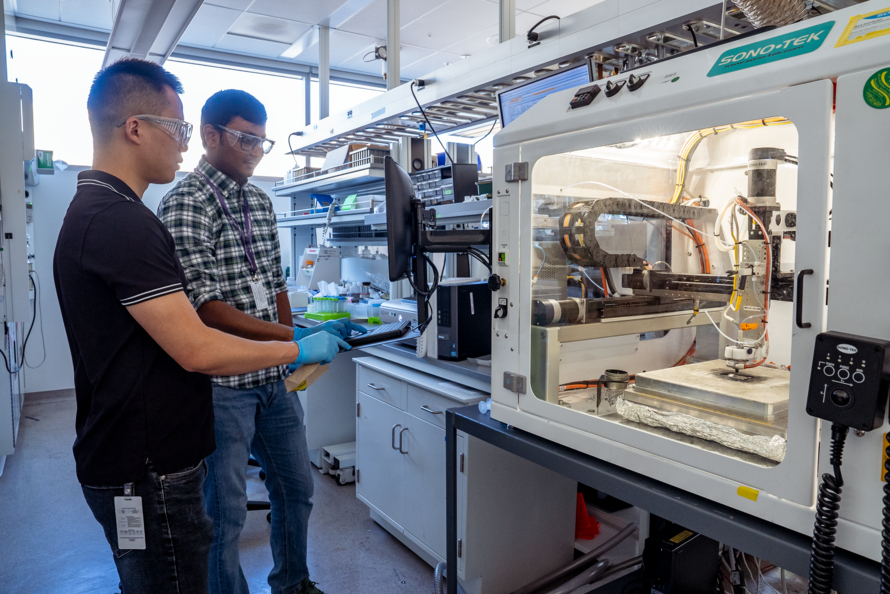
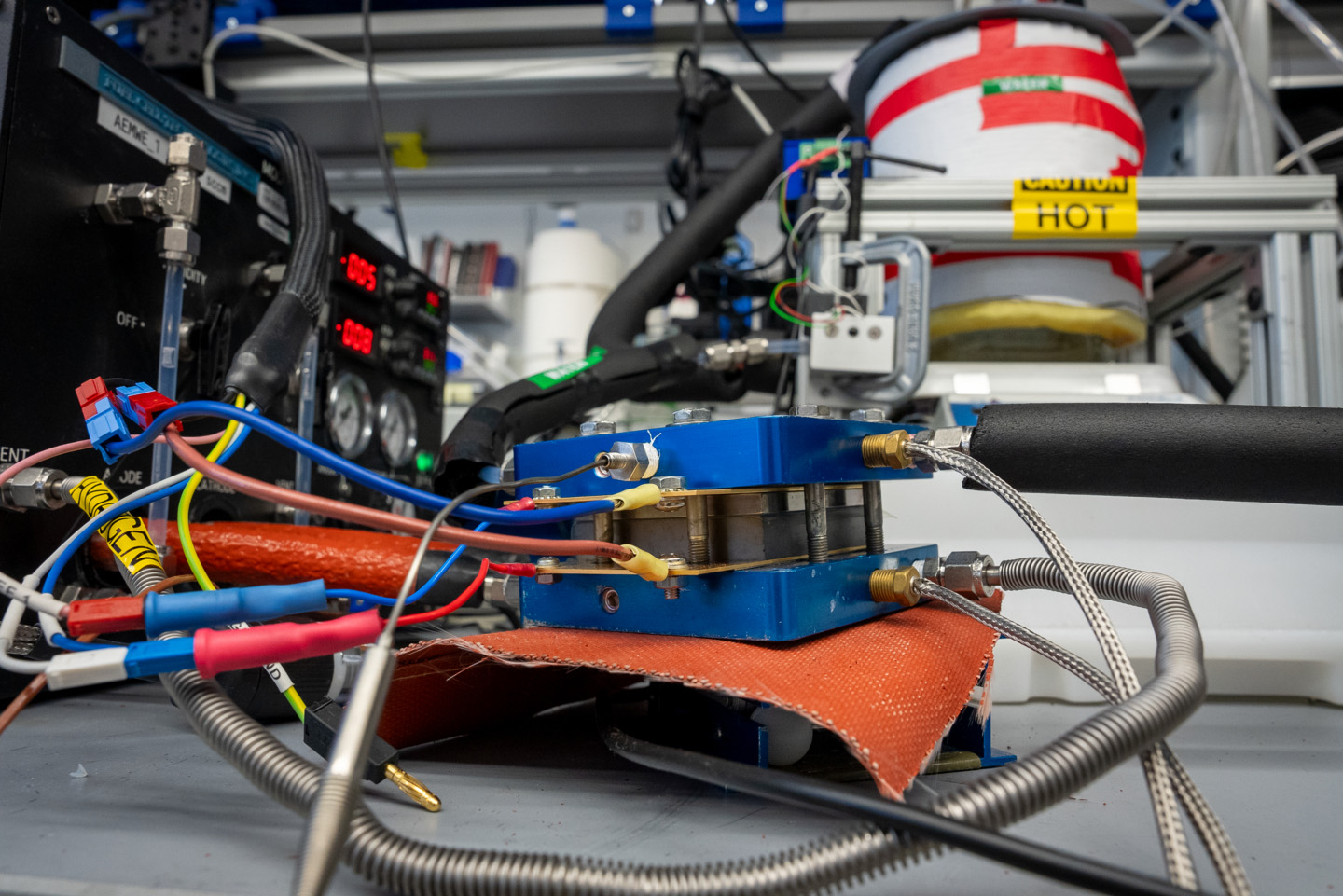
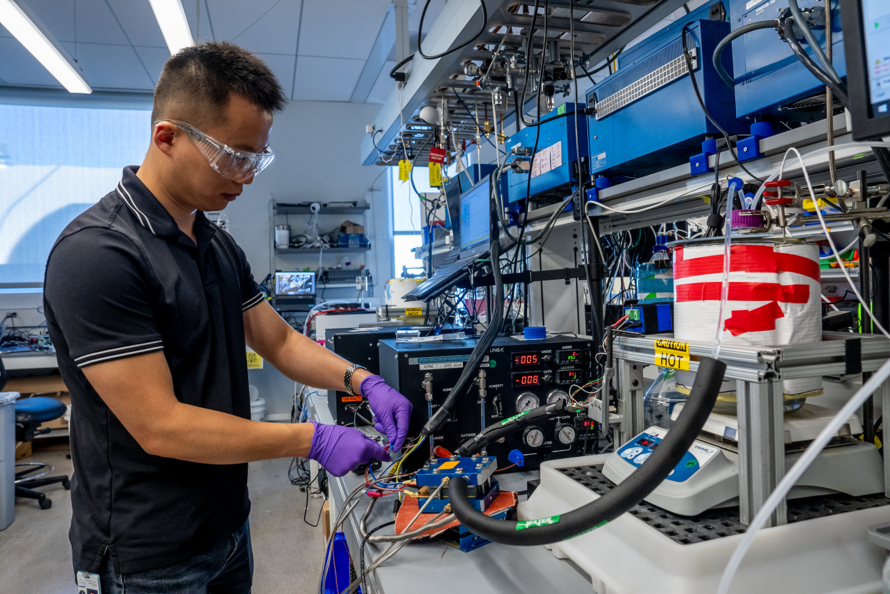
"This allows us to use lower iridium content per unit of H2 produced," said Mukundan. "We are also currently working on developing a better understanding of the durability of iridium in these water electrolyzers to eventually improve their lifetimes when less of the element is used, and developing accelerated stress tests to better evaluate the durability of the entire system."
Another issue standing in the way of cost-effective fuel generation from PEM electrolyzers is their wasteful energy demand when they are in standby mode. Traditionally, these systems must be kept warm and juiced with a little electricity to maintain the correct charges at the electrodes when they are not splitting water molecules, to avoid degradation by keeping the iridium anode in an electron accepting state and the platinum cathode in an electron donating state. Mukundan and his colleagues are investigating system designs that can be kept idle without degradation.
"If the system can be operated dynamically without any durability problems, then you would just operate the system during times of low electricity prices and keep the system idle at peak demand times when electricity prices are high," said Mukundan. "For future systems that produce H2 at very low cost, this type of dynamic operation is critical."
2. Methane Pyrolysis: making hydrogen fuel from a greenhouse gas
Whereas electrolysis splits water, another technique, called methane pyrolysis, uses heat and catalysts to split methane gas (CH4) - a potent greenhouse gas produced by agriculture and industrial processes - into hydrogen and useful solid carbon products like graphite, carbon nanotubes, and fullerenes. There are no large-scale methane pyrolysis systems in use yet because existing technologies require high heat (greater than 1,000 C or 1,832 F) to initiate the molecular breakdown, therefore making the process expensive due to the costs of energy and specialized, temperature-resilient equipment. But given that the approach offers the three-for-one benefit of removing a greenhouse gas while producing a carbon-free fuel and valuable materials, many researchers are working to make methane pyrolysis commercially viable.
A multi-institutional team led by Ji Su of Berkeley Lab's Energy Conversion Group is developing a new liquid metal catalyst with promise for high efficiency, high durability methane pyrolysis at lower temperatures between 450-800 C (842-1472 F). A paper describing the principles of the catalyst and data from early experiments was recently published in Science, and the team received a 2023 R&D 100 award.
"The low temperature activity opens the opportunity for the methane pyrolysis process to use waste heat from other industrial processes rather than other energy sources that themselves generate carbon," said Su. "For example, the total waste heat generated in the European Union that is within the range our catalyst uses is estimated to be about 120 terawatt-hours per year. Additionally, a low operating temperature is ideal for electric heating using renewable electricity, which results in a higher efficiency and zero CO2 footprint."
The team's prototype system is elegantly simple. The catalyst is an alloy of nickel, molybdenum, and bismuth. A thin layer of the alloy just a few centimeters tall is packed in a small, curved quartz tube on top of a thin sheet of porous quartz. The tube is heated, causing the catalyst to become liquid. Methane is piped in through the bottom and bubbles through the porous quartz into the liquid catalyst, where the alloy's mixture of metallic atoms work together to break the CH4 molecules apart. Hydrogen gas flows out the top of the tube, where it can be collected, while the carbon byproduct - pure graphite, in these tests - accumulates neatly on top of the catalyst. The scientists noted that, in the prototype system, 2.4 liters of hydrogen gas can be produced by one gram of nickel in the catalyst in one hour. After running the system continuously at 800 degrees for 120 hours, the system still functioned smoothly and no chemicals products other than graphite were detected, indicating promising durability and complete breakdown of the methane without any unintended byproducts that could damage the system or become a source of pollution.
Although this technology is still in early development, the team is optimistic that it would operate well at commercial scale. "Our technology surpasses the overall performance of any other catalyst for methane pyrolysis," said Su. He and the others plan to build a meter-long version of the methane reactor next, and envision that someday soon, a system with many of the tube reactors hooked up in parallel to a heat source could run simultaneously, producing large amounts of clean hydrogen fuel.
3. Solar generation: nature-inspired, sustainable fuels
Electrolysis and pyrolysis are not the only pathways to sustainable hydrogen. Another avenue is solar generation - a class of technologies inspired by photosynthesis that use the energy in sunlight to drive chemical reactions converting water and atmospheric gases into fuels. Scientists affiliated with the Liquid Sunlight Alliance (LiSA), a Berkeley Lab-led Fuels from Sunlight Energy Innovation Hub funded by the U.S. Department of Energy, are working to mature these solar fuels systems and bring them up to the scale needed for industrial use.
Recently, a LiSA team developed a new artificial photosynthesis cell made from cuprous oxide (Cu2O) with thin layers of silver on top and gold and iron oxide on the bottom. Cuprous oxide is a great solar fuel catalyst because it is cheap, readily available, and highly reactive to light - but on its own, it quickly becomes damaged by the corrosive free electrons and charged molecules involved in and produced during the chemical reactions. The team found that their sandwich-like design greatly reduced corrosion and improved longevity by funneling charges generated on the top surface through the copper material into the gold and iron "sink." Though their experiments were for generating ethylene, another gaseous fuel, the technology could be easily adapted for production of H2.
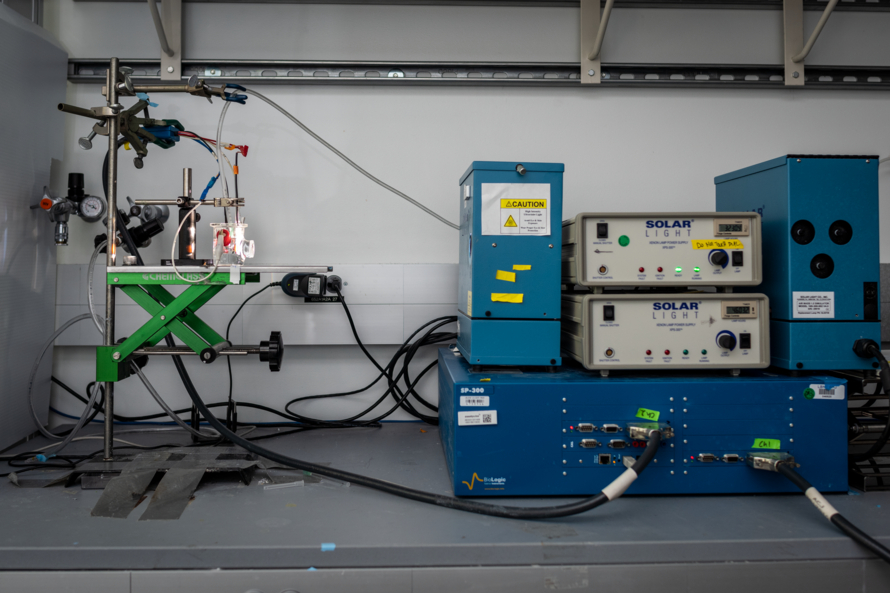
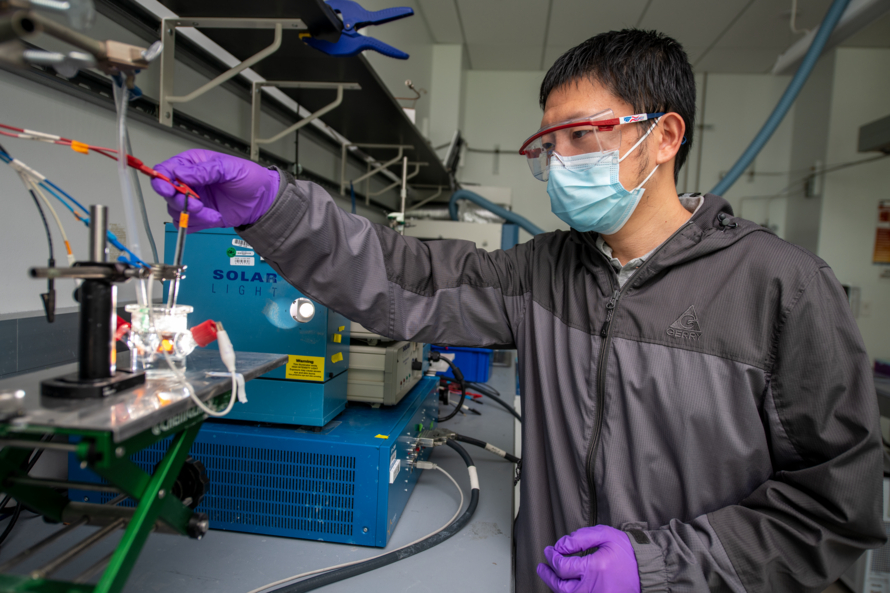
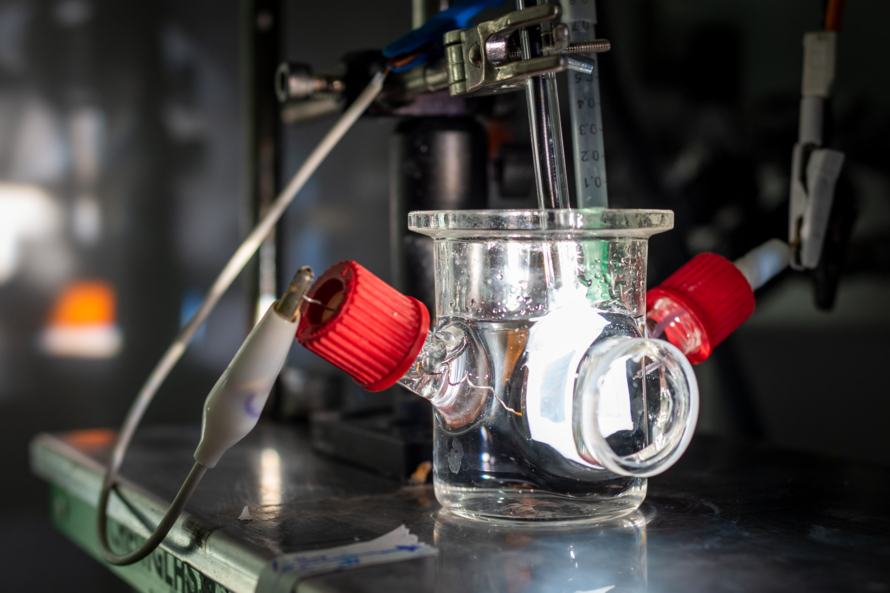
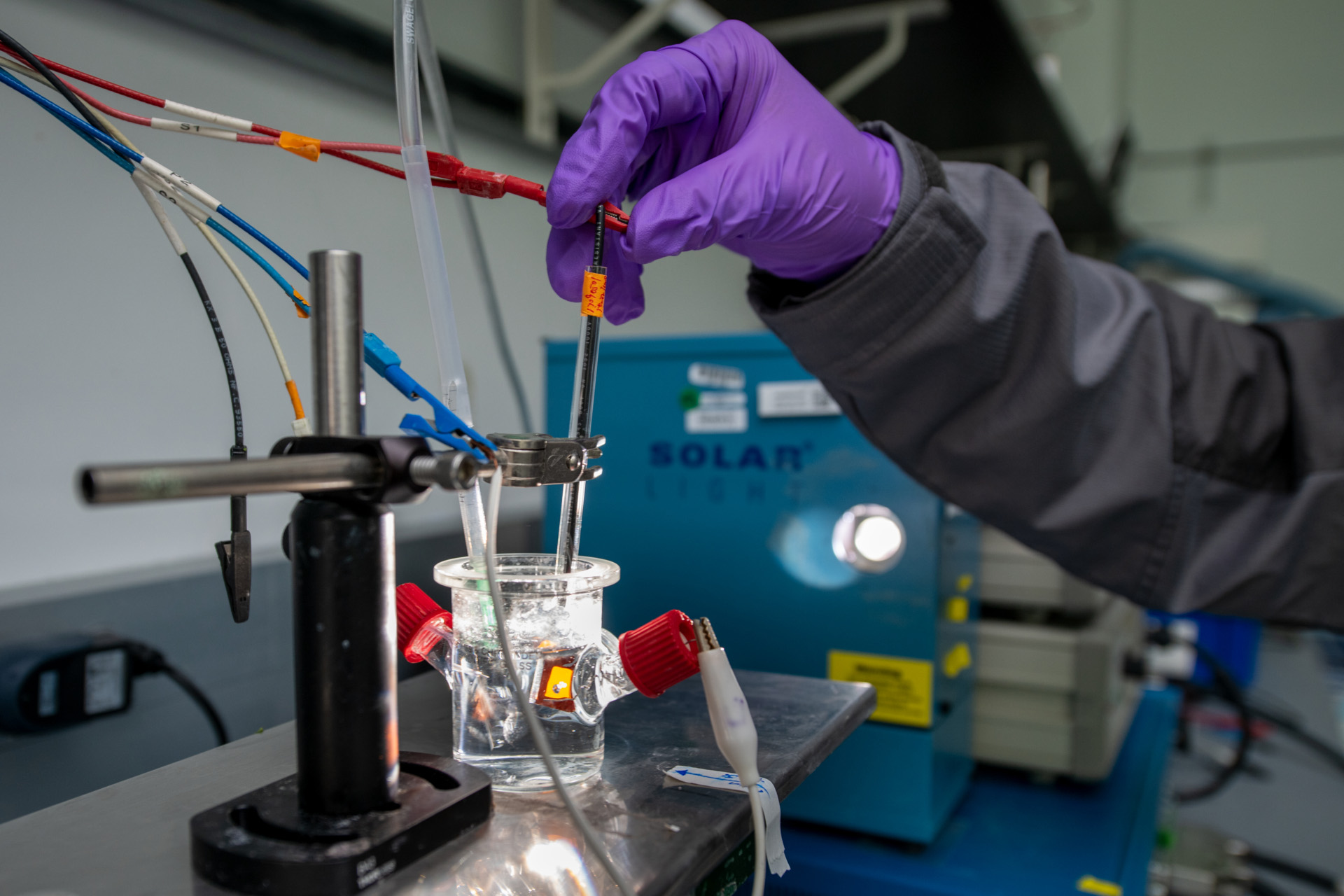
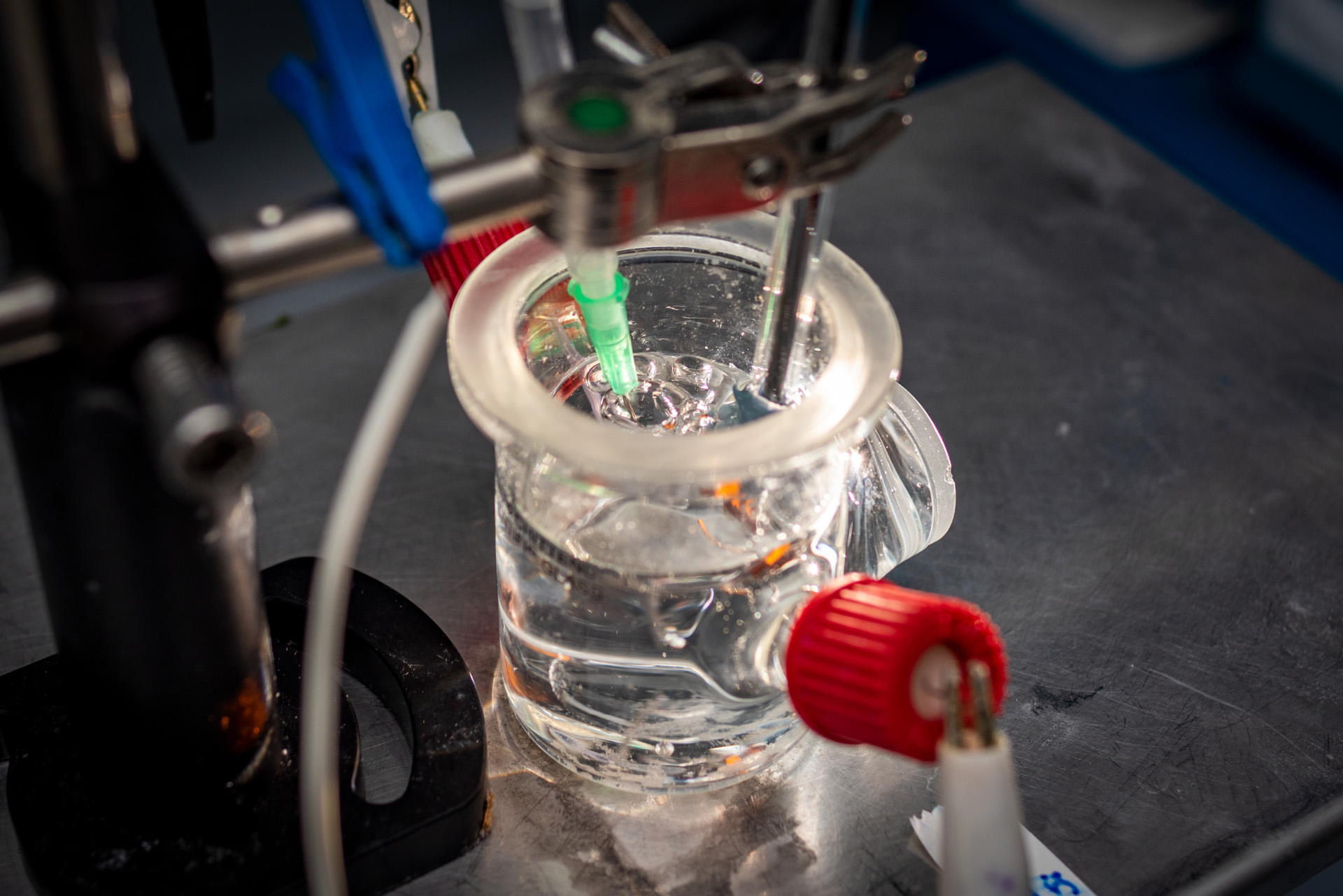
"The new insights in the work with Cu2O can apply equally well to making other solar fuels like hydrogen," said Joel Ager, a materials scientist and collaborator on the study. "Solar production of hydrogen is a more mature technology yet it still lacks the longevity needed for commercial use. We are excited to apply the insights from what we are learning from Cu2O to other systems."
Ager leads the Photoelectrochemical team for HydroGEN, a consortium of five DOE national labs that collaborate with industry and academic partners to develop advanced water-splitting materials. Through HydroGEN, Berkeley Lab scientists began working with researchers at the University of Michigan to analyze that group's silicon and gallium nitride-based artificial photosynthesis device. Experiments from the past several years have shown that the device is remarkably efficient at producing hydrogen. And, unlike every other artificial photosynthesis catalyst - and most technology, in general - the gallium nitride gets more efficient over time instead of breaking down. Using advanced electron microscopy and X-ray spectroscopy performed at Berkeley Lab's Molecular Foundry, the collaboration was able to show that increased hydrogen production from the sidewalls of the nanowires used in the device was responsible for the performance improvement. Work performed at Lawrence Livermore National Laboratory, another member of the HydroGEN consortium, subsequently unraveled the atomic mechanism responsible for the effect.
"We've been working on this material for over 10 years - we know it's stable and efficient. But this collaboration helped to identify the fundamental mechanisms behind why it gets more robust and efficient instead of degrading," said Zetian Mi, the material's inventor and a professor of electrical and computer engineering at the University of Michigan. "The findings from this work will help us build more efficient artificial photosynthesis devices at a lower cost," said Mi.
4. Better methods for hydrogen storage
Once H2 has been generated, it must be stored and transported to fueling stations, power plants, factories that use hydrogen in chemical manufacturing, and other users. However, hydrogen is tricky to contain due to its miniscule size. Since each atom in the H2 pair is composed of just one proton and one electron, the molecule can easily slip through the spaces between larger atoms bonded together in solid materials. To reduce escape from storage vessels, hydrogen gas is often stored in either liquid form at very low temperature or compressed at high pressures. And while these approaches work quite well, they are very energy intensive and expensive.
Berkeley Lab scientists are developing special materials called metal organic frameworks (MOFs) that can soak up the hydrogen gas like a sponge at pressures and temperatures much closer to ambient conditions. All MOFs are composed of repeating units of metallic atom clusters surrounded by organic linking molecules, though the exact constituents vary widely depending on what kind of molecules the MOF is meant to attract.
These units give rise to a porous three-dimensional structure with an incredibly high surface area per volume of the material. Hydrogen gas readily flows into the pores then clings tightly to charged particles on the interior surfaces until the pressure is released, after which the hydrogen is discharged and can be transferred to its final destination.
"Liquid hydrogen requires massive cooling to negative 250 degree Celsius, and compressed gas requires high pressures 350-700 times atmospheric pressure," explained Peng Peng, a research scientist in ETA's Sustainable Energy & Environmental Systems department. "MOFs can store the same amount of hydrogen as high-pressure gas under moderate cooling, and half of the pressure."
Other advantages of MOFs include less loss of evaporated gas to the atmosphere compared to liquid storage containers and lower combustion hazard than high-pressure tanks.
Peng and his colleagues have been setting targets for new MOFs and evaluating MOF properties and performance through computational models based on small-scale testing of samples synthesized by chemist and materials scientist collaborators at UC Berkeley, through the DOE Hydrogen Materials Advanced Research Consortium (HyMARC). Some of the materials have advanced to the prototype stage and a handful are already on the way to commercialization. According to Peng, the biggest obstacles for MOFs at this time are the high cost of manufacturing the material and charging hydrogen gas into it rapidly.
The Berkeley Lab team, through HyMARC, is also looking at other storage solutions such as metals that bind hydrogen atoms, called hydrides, and ways to store hydrogen in other chemical bonds known as a chemical carrier, in molecules like toluene (C₆H₅CH₃). Working with both academic groups and industry partners, Berkeley Lab scientists are designing coupled systems that integrate storage technologies with the hydrogen-consuming device that feeds from it.
5. Advanced fuel cells that harness hydrogen power
In addition to producing and storing hydrogen, our researchers build and test fuel cells that can be used in large-scale energy production systems to support the electric grid, as well as power zero-emission vehicles.
A key project in the latter area is the Million-Mile Fuel Cell Truck Consortium (M2FCT), a multi-lab DOE initiative that Berkeley Lab co-leads to advance PEM fuel cells so that they are durable enough to use in the heavy trucks used for long-haul transportation. The members of M2FCT also perform cost analysis and life cycle assessment of the hydrogen-powered trucks to forecast the impacts of replacing the diesel-powered ones.
PEM fuel cells look like PEM electrolysis devices that work in reverse. Instead of generating H2 from water using electricity, the fuel cells split H2 molecules, generating a flow of free electrons - electricity that can power an engine - and protons, which move across a membrane then interact with O2 entering the cell from the air to form water vapor. One cell can generate about 300 watts currently, enough to power five standard light bulbs. A fuel cell engine capable of powering a car or truck is composed of many cells stacked together.
"Transitioning to hydrogen fuel cell heavy-duty vehicles would have a significant impact on reducing greenhouse gas emissions," said Ahmet Kusoglu, a scientist in the Energy Conversion Group and member of the M2FCT team. He noted that heavy-duty trucks make up a small fraction (~5%) of the total vehicles driven in the U.S. but contribute over ~25% of all transportation-based emissions and eat up one quarter of the fuel consumed annually.
Fuel-cell engines for light-duty vehicles - like passenger cars - are quite advanced, following decades of research and development. But this technology can't be copy-pasted into heavy-duty vehicles. Fuel cell engines for cars have been designed to be lightweight and affordable, whereas trucks require tough cells that can last for long distances at low operational cost - weight and sticker price aren't as big of concerns.
Kusoglu and his colleagues aim to understand how and why a PEM fuel cell degrades to develop materials and strategies to improve the system durability toward the target of a lifespan of one million miles - which would represent a five-fold increase over the durability of current fuel cell car engines. On top of the obvious benefits of cutting emissions from the transportation sector, the program will also make it easier for implementation of fuel cells in a variety of heavy-duty applications, from port equipment to ships to trains.
"The heavy-duty vehicle market could be an avenue to get fuel cell technology deployed quickly," Adam Weber, Leader of the Energy Conversion Group and co-director of M2FCT and former deputy director of the Fuel Cell Performance and Durability consortium, which was focused on fuel cells for the light-duty vehicles. "This will encourage building the needed hydrogen refueling infrastructure."
6. Building systems that work, economically and environmentally
Our scientists aren't just designing hydrogen technologies and hoping they will work in the real world. They use technoeconomic analysis (TEA) and life-cycle assessment (LCA) to study the inputs, outputs, and environmental and economic impacts of different devices and systems. TEA and LCA allows scientists to investigate how energy technologies will work at industrial scale while they are still in early development, and to understand how changing components of a technology - for example, switching a material used in an electrolyzer - will affect cost, performance, and supply chains.
Hanna Breunig, deputy head of the Sustainable Energy and Environmental Systems Department, specializes in TEA and LCA for hydrogen energy systems. She is also co-director of the Lab's HyMARC work. Breunig and her colleagues collaborate on many of the projects mentioned previously in this article, and lead their own research.
One of the department's current analysis projects is focused on using hydrogen to limit the use of fossil fuels in iron and steelmaking, an enormous global industry that is a significant source of CO2 emissions. According to the International Energy Agency, global steel production contributes 2.78 billion metric tons of CO2 emissions per year, or roughly 1.39 tons of CO2 per ton of steel made.
These emissions come from the natural gas or coke (concentrated coal that's been heated to remove impurities) that is mixed with iron ore (iron oxides) in high temperature furnaces to remove oxygen, in order to produce more purified iron that can be combined with carbon to make steel. The natural gas and coke react with the oxygen to form CO2.
But an alternative type of furnace has been designed that burns hydrogen fuel to provide the heat and electrons needed to remove oxygen from iron ore. Because steel is an alloy of iron and carbon, some carbon will always be needed in the production process, yet the total amount required, and the reliance on petroleum products, could be significantly reduced by switching to this new design. "When we look at the emissions that are resulting from producing iron and steel, it's coming from providing high temperatures as well as providing the reducing agent that goes into taking that iron ore and turning it into an iron sponge that's later processed," said Breunig. "So to go from a blast furnace that uses a coke product to a direct reduction iron furnace that uses hydrogen with some source of carbon - that might be biochar, it could be bio-methane - you can reduce the greenhouse gas emissions by over 95%"
Breunig and Fabian Rosner at Berkeley Lab are working with the National Renewable Energy Laboratory in Colorado to develop a supply chain tool linking hydrogen-powered furnaces with hydrogen gas generated by renewable-powered electrolysis offshore and onshore in the United States. Using TEA and LCA, they have identified process improvements that would make steel made from this remarkable decarbonized system more cost competitive for buyers, as well as less sensitive to fluctuations in hydrogen delivery prices.
The research featured in this article is funded by the DOE Office of Science and the Office of Energy Efficiency and Renewable Energy.