UConn's Connecticut Manufacturing Simulation Center collaboration with local biotech companies is fostering innovation and economic development in the state
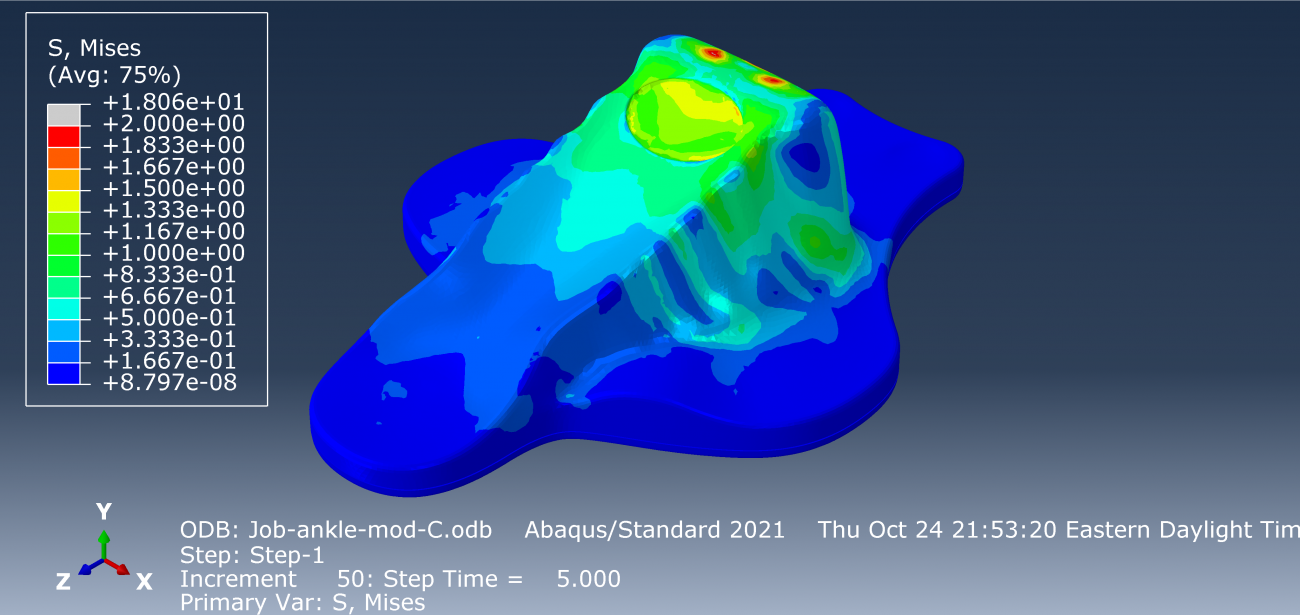
In this CAD-enhanced model, the level of stress in the ankle therapy device is shown in color codes under human weight loads from above.
A creative collaboration between UConn's Connecticut Manufacturing Simulation Center (CMSC) and ZANEEZ® Health in Glastonbury, Conn., is focusing on virtual prototyping of an innovative foot and ankle platform made from advanced thermoplastic polymers. This process reduces the time and cost associated with multiple rounds of physical testing, optimizing structural integrity and product performance before physical production begins.
"AnkleSTONE®, developed by ZANEEZ® Health, represents a significant advancement in orthopedic rehabilitation devices," says Jeongho Kim, principal investigator and CMSC director, and also a professor for the School of Mechanical, Aerospace and Manufacturing Engineering. "This partnership with CMSC allows our team to provide advanced technical expertise and simulation capabilities to enhance product development.
"At CMSC," Kim explains, "we have the tools and computational resources to assist companies like ZANEEZ® in overcoming limitations in physical prototyping. Our partnership enables them to analyze critical load capacities and structural performance, for example, helping refine the AnkleSTONE® design for maximum effectiveness and resilience."
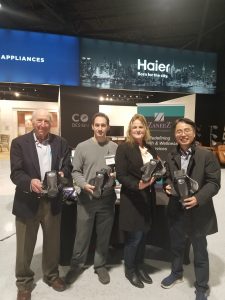
Supported by the U.S. Economic Development Administration, CMSC provides technical assistance at no cost to small- and medium-sized manufacturers in Connecticut, fostering innovation and economic development in the state. The center offers a suite of high-performance computing-based modeling and simulation services, enabling companies to replace costly physical prototypes with virtual simulations that streamline the development process.
Many small businesses, Kim adds, lack the specialized resources required for intensive prototyping. The center's physics-based modeling and virtual prototyping approach, he says, allows companies like ZANEEZ® to develop cost-effective solutions efficiently.
CMSC's staff is currently engaged in virtual prototyping of the AnkleSTONE® foot and ankle platform, made from advanced thermoplastic polymers. This process reduces the time and cost associated with multiple rounds of physical testing, optimizing structural integrity and product performance before physical production begins.
"Research and support from CMSC has made our development process more efficient, saving a tremendous amount of time and expense versus physical prototyping and destructive testing," says Dan Tangari, a lead designer from Spark Design LLC, working with ZANEEZ®. Spark, Tangari explains, works with a diverse group of clients to help develop innovative products from initial concept through production.
CMSC, says Tangari, has been assisting Marien Zanyk, ZANEEZ® founder and CEO, in refining her AnkleSTONE® product for injection molding. "This requires accounting for complex loads and stress that the product will encounter during use," he explains. "This type of analysis is outside the scope of our capabilities. Partnering with Dr. Kim and CMSC was an invaluable step in the development process."
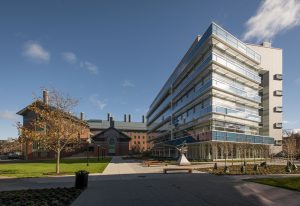
Through Kim's advanced structural analysis of the AnkleSTONE® product, potential weak areas were identified in the design for typical use-case scenarios, Tangari continues. "Our combined team was able to meet virtually at regular intervals to review new findings based on the latest simulations. This virtual prototyping provided insights that guided our design improvements, allowing us to iterate faster, and make much more informed decisions during CAD refinement. The collaboration between ZANEEZ® and CMSC allows us to feel confident moving forward that we have a proven design that is ready for production."
Since its inception in 2016, CMSC has collaborated with over 50 businesses, training more than 350 professionals, 2,400 UConn students, and 24 community students. Other CMSC projects include partnerships with Aero Gear, PCX Aerospace, and Advanced Manufacturing LLC, focusing on complex simulation and optimization for Connecticut's manufacturing sector.