Manufacturers in Akron, Cleveland and Erie (PA) to produce 5,000 shields per day
An engineering team from Case Western Reserve University, Nottingham Spirk and Penn State Behrend have partnered with manufacturers in Northeast Ohio and Erie, Pennsylvania, to launch rapid production of face shields for health providers treating patients diagnosed with COVID-19.
They expect to produce 5,000 shields per day starting early April to help address the critical national shortage of protective gear for medical workers. The shields are being sold at cost to any hospital that contacts the vendor, Bliley Technologies Inc. Orders are already being accepted, including from Cleveland Clinic.
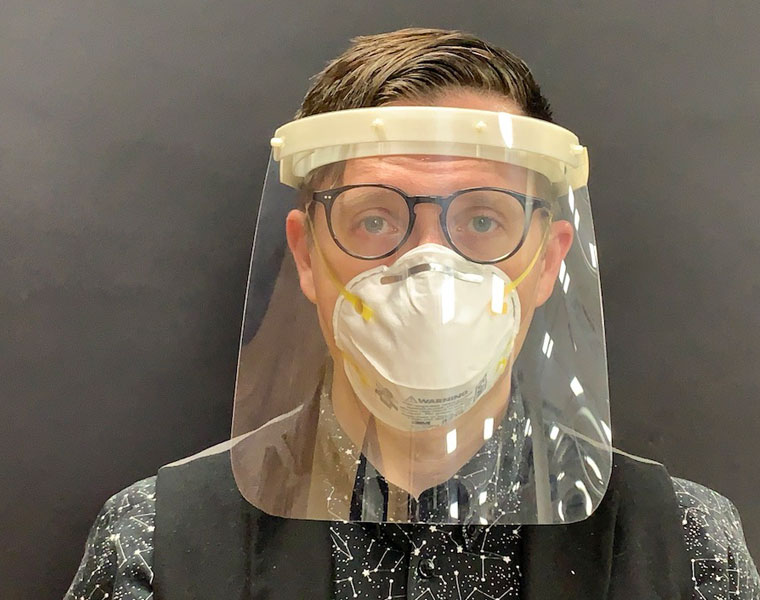
"Access to rapid prototyping equipment at think[box] allowed this to ramp up in six days," said Ian Charnas, director of innovation and technology at Sears think[box] at Case Western Reserve. "Without that, we would have had no chance to make this happen so quickly."
Charnas teamed with Bill Rabbitt, engineering project manager at Nottingham Spirk and double engineering alumnus of Case Western Reserve, and Jason Williams, an assistant teaching professor of engineering at Penn State Behrend in Erie, Pennsylvania.
Charnas became aware that he and Williams were working on a similar project "so we merged our efforts," he said. "By last Friday, March 27, we had a manufacturing line set up with finished designs. Everybody we talked to strongly wanted to help, and they were answering their phones at midnight. Saving lives is at the forefront of what everyone's thinking."
University Hospitals and Cleveland-based manufacturing-advocacy group MAGNET also were simultaneously investigating face shields and provided crucial help.
The team's design is based on the Prusa Face Shield, and aims to improve the design in sterilization and high-volume production
The headband is an injection-molded polypropylene part compatible with nearly every hospital sterilization method, including the autoclave. Using injection-molding and die-cutting, tens of thousands of face shields can be produced daily.
Their design creates a shield with components that can be cut on a rolling die machine. That reduces the cutting time from 30 seconds to less than one second.
Production is also a team effort: The R.C. Musson Rubber Co. in Akron, Ohio, will make the rubber straps. Die Cut Products of Cleveland will supply additional clear shields.
The supply chain also includes three Erie manufacturing companies: Port Erie Plastics, which is building the mold and molding the frames; Munot Plastics, which will produce the shields; and Bliley Technologies Inc., which will manage logistics and distribution to Northeast Ohio and Erie and State College, Pennsylvania.
Williams, Charnas and Rabbitt created a website for their White Label Face Shields. They are making designs for the component pieces available for free download.