CMSC promotes innovation and economic development through modeling and simulation work while teaching the next-generation workforce advanced computing and simulation skills
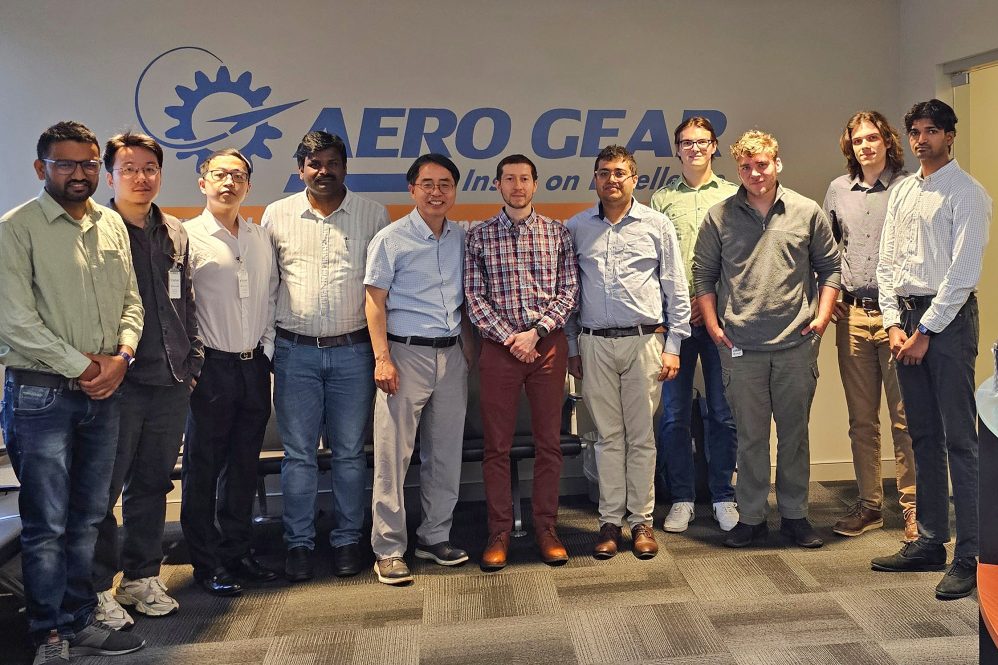
Faculty, staff, and students from UConn's Connecticut Manufacturing Simulation Center (CMSC) visited engineers at Aero Gear, Inc. on May 29 to provide UConn students with an opportunity to observe various manufacturing processes at the company. CMSC offers small Connecticut manufacturing businesses with free technical support and specialized machining processes and simulations.
Since 1982, Aero Gear, Inc. in Windsor has worked to engineer and manufacture customized gears and gearbox assemblies for the global aerospace industry. These drive gear systems help control the power that moves an airplane forward for Pratt & Whitney, Sikorsky, Boeing, and many other aerospace businesses.
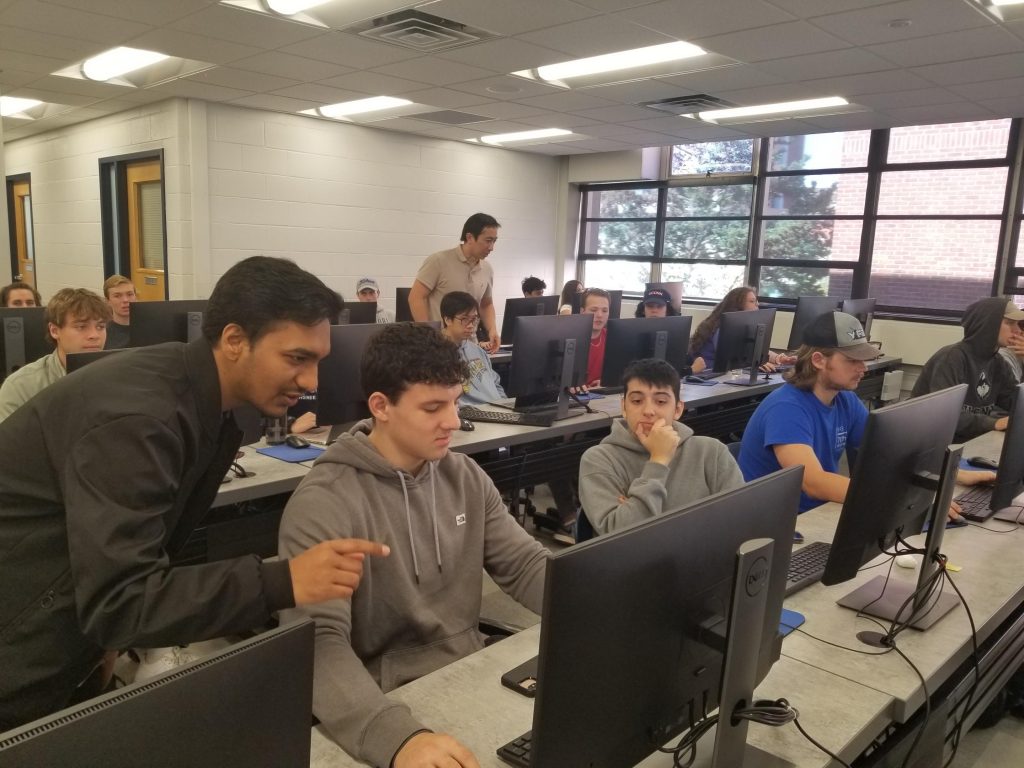
Although the company has since grown from two to 170 employees and houses dozens of machining instruments, some processes cannot be carried out in the facility. So, they sought technical advice from UConn's Connecticut Manufacturing Simulation Center (CMSC).
"CMSC has the tools-and willing researchers-to approach complex materials physics problems that we simply have no way to investigate," says Pat Brueckner, director of engineering at Aero Gear. "Our collaboration with CMSC helps us understand our heat treat and machining processes from a more academic perspective and close a scientific gap that exists between academia and real-world applications."
In partnership with the U.S. Economic Development Administration, CMSC provides technical support-at no cost-to small-to-medium manufacturing businesses in Connecticut. The center strives to promote innovation and economic development and train the next-generation workforce with computing and simulation skills.
"Some businesses may not have relevant expertise or resources to handle complicated processes or have the right machinery to complete a job," says Jeongho Kim, professor of civil and environmental engineering and director of CMSC. "We're able to help, by being sort of an R&D department for them. They give us their problems and we work to find them answers through physics-based modeling and simulation."
CMSC also provides finite element modeling and simulation, structural/thermal/fluid analysis, and machine learning methods for diagnosis and prognosis. It uses state-of-the-art equipment to aid manufacturers with welding, laser cutting, 3D printing, machining, milling, cutting, heat treating, die quenching, stamping, spinning, metal forming, forging, casting, injection molding, composites manufacturing and additive manufacturing needs.
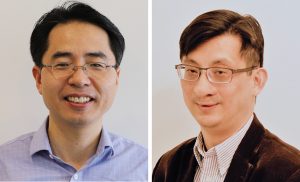
But more importantly, the well-trained CMSC staff can work one-on-one with industry partners to help them find solutions for problems. Led by Professor Kim and associate professor Jiong Tang, United Technologies Corporation Professor of Advanced Materials and Processing, the CMSC team also consists of engineering graduate students and technicians.
For Aero Gear, the CMSC staff is helping with heat treatment and carburizing processes solutions for a customized steel gear. These processes can help ensure the metal is more durable and wear-resistant. CMSC is also taking the lead on crafting aluminum accessory gearbox housing by using a high precision milling process known as Computer Numerical Control (CNC) milling.
"Jeongho and his team will regularly present their latest findings and those data help shape our decision-making process when we run into manufacturing problems," Brueckner says. "Their research is certainly helpful and has made our process more efficient. In my opinion, the partnership over the last few years has been very successful."
Since its establishment in 2016, the CMSC contracted with 40 industries and trained more than 300 professionals, 1,800 UConn students, and 24 community students.
The center currently collaborates with Aero Gear and three other key industry partners: PCX Aerosystems in Newington; Carey Manufacturing in Cromwell; and Advanced Manufacturing, LLC in East Hartford.
The CMSC's staff is working with PCX Aerospace on a carburization simulation of a steel thin-walled gear shaft used in the aerospace industry. "We greatly appreciate the CMSC's professional work and willingness to address our technical needs," says Gregory Niedbala, engineering manager at PCX Aerosystems. "Their simulation support has been helpful in overcoming challenges and achieving our goals. Their commitment to excellence and dedication to our success speaks volumes to the positive impact they have."
For Carey Manufacturing, the team is helping business leaders Alison Carey and Mike Fitzpatrick on developing a simulation that depicts how a laser beam could cut through carbon steel.
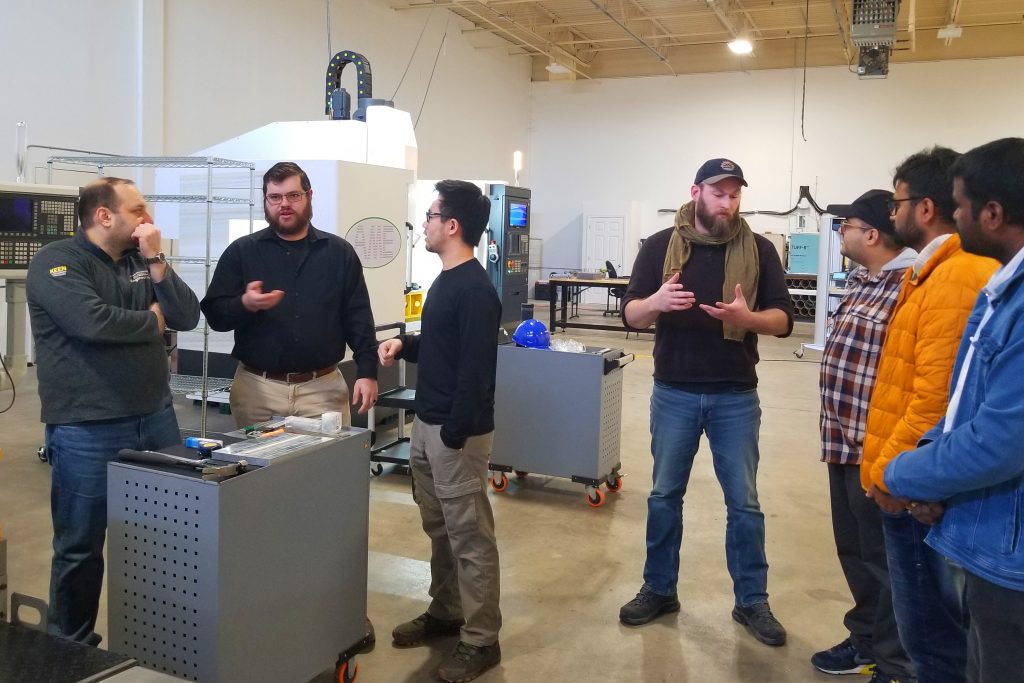
And for Advanced Manufacturing LLC, CMSC is working with company president Dongsheng Li and process engineer Oliver Walz on a friction stir welding simulation and optimization. Friction stir welding technology allows for workpieces to be joined without needing to reach a melting point, hence, avoiding many of the issues present in traditional welding methods such as thermal stresses which can result in part failure under stress.
"Think of kneading of two pieces of dough or clay together in order to join them into a homogeneous solid," Walz explains. "This process achieves a very high strength weld and is most commonly used in industries that fabricate aluminum parts but can be used to weld polymers, steels, copper, and even dissimilar metals."
With only six employees, the small business will benefit from results of CMSC's simulation by helping to improve the efficiency and efficacy of its technology processes.
"CMSC's work in simulating material behavior of the entire welding process is a significant contribution to our company's engineering practices," Walz says. "The greater understanding of material behavior these simulations show, will give us the ability to predict and mitigate negative effects of a weld on a workpiece such as material stresses, deformation, and weld faults."