Researchers at ETH Zurich have developed a climate-friendly covering for walls and ceilings that temporarily stores moisture, creating a comfortable environment in heavily used indoor spaces. The covering components are made of mineral waste materials and are produced by means of 3D printing.
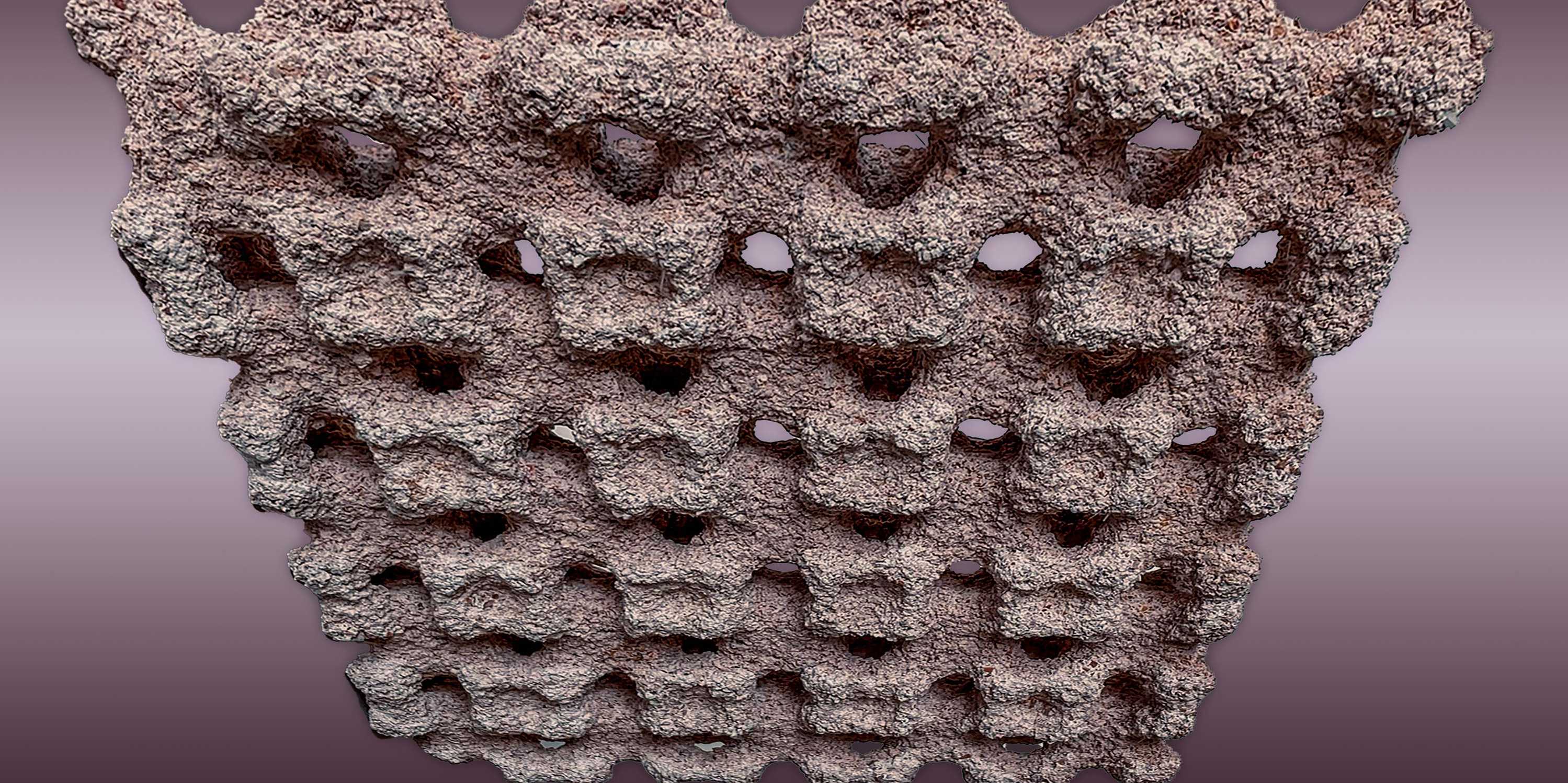
In brief
- ETH civil engineers and architects have developed a new building component that can be used to dehumidify rooms.
- The building component is used in walls and ceilings to bind and temporarily store moisture.
- It is produced sustainably using 3D printing from re-used materials and can replace mechanical ventilation systems.
Whether it's the meeting room of an office building, the exhibition room of a museum or the waiting area of a government office, many people gather in such places, and quickly the air becomes thick. This is partly due to the increased humidity. Ventilation systems are commonly used in office and administrative buildings to dehumidify rooms and ensure a comfortable atmosphere. Mechanical dehumidification works reliably, but it costs energy and - depending on the electricity used - has a negative climate impact.
Against this backdrop, a team of researchers from ETH Zurich investigated a new approach to passive dehumidification of indoor spaces. Passive, in this context, means that high humidity is absorbed by walls and ceilings and temporarily stored there. Rather than being released into the environment by a mechanical ventilation system, the moisture is temporarily stored in a hygroscopic, moisture-binding material and later released when the room is ventilated. "Our solution is suitable for high-traffic spaces for which the ventilation systems already in place are insufficient," says Guillaume Habert, Professor for Sustainable Construction, who supervised the ETH research project.
Waste material from marble quarrying
Habert and his research team followed the principle of the circular economy in their search for a suitable hygroscopic material. The starting point is finely ground waste from marble quarries. A binder is needed to turn this powder into moisture-binding wall and ceiling components. This task is performed by a geopolymer, a class of materials consisting of metakaolin (known from porcelain production) and an alkaline solution (potassium silicate and water). The alkaline solution activates the metakaolin and provides a geopolymer binder that binds the marble powder to form a solid building material. The geopolymer binder is comparable to cement but emits less CO2 during its production.
In the ETH project, the scientists succeeded in producing a prototype of a wall and ceiling component measuring 20 × 20 cm and 4 cm thick. Production was carried out using 3D printing in a group led by Benjamin Dillenburger, Professor for Digital Building Technologies. In this process, the marble powder is applied in layers and glued by the geopolymer binder (binder jet printing technology). "This process enables the efficient production of components in a wide variety of shapes," says Benjamin Dillenburger.
Moisture-controlling components increase comfort
Combining geopolymer and 3D printing to produce a moisture reservoir is an innovative approach to sustainable construction. Building physicist Magda Posani led the study of the material's hygroscopic properties at ETH Zurich before recently taking on a professorship at Aalto University in Espoo, Finland. The project is based on the doctoral theses of materials scientist Vera Voney, supervised by Senior Research Associate Coralie Brumaud and architect Pietro Odaglia, who developed the material and the 3D printing machine at ETH.
"We were able to demonstrate with numerical simulations that the building components can significantly reduce humidity in heavily used indoor spaces," says Posani, summarising the main result of the research project. For the simulation, it was assumed that the walls and ceiling of a reading room used by 15 people in a public library in Oporto, Portugal had been completely lined with hygroscopic components. Magda Posani calculated how often and to what extent the humidity exceeded the comfort zone, i.e. 40 to 60 percent relative humidity in this virtual reading room over the course of a year. From this, she calculated a discomfort index, a figure that expresses the loss of comfort caused by excessively high or low humidity. If the reading room were fitted with the moisture-binding components, the discomfort index could be reduced by 75 percent compared to a conventional painted wall. If components were used that were 5 cm thick instead of just 4 cm, the discomfort index fell by as much as 85 percent.

In conventional 3D printing, a viscous plastic is applied layer by layer to a base plate. A different 3D printing process is used for the production of the wall and ceiling component: binder jet printing. Here, a powder bed of finely ground marble and metakaolin is placed on the base plate. A movable jet applies a potassium silicate solution to the desired places, which solidifies the powder. By repeating the process, the component is built up layer by layer. (Illustration: Vera Voney)
More climate-friendly than ventilation systems
The hygroscopic wall and ceiling components are climate-friendly, i.e. they cause significantly lower greenhouse gas emissions over a 30-year life cycle than a ventilation system that dehumidifies air quality to the same extent. In the simulation calculations, the wall and ceiling components were also compared with a clay plaster that has been used since time immemorial and also passively regulates the air humidity in indoor spaces. This old technique proved to be even more climate-friendly than the hygroscopic components. However, the plaster has a lower storage capacity for water vapour.
The research at ETH has shown that the combination of geopolymer and 3D printing can be used to produce wall and ceiling components for efficient moisture buffering. After this proof of concept, the technology is, in principle, ready to be further developed and scaled for industrial manufacture. At the same time, research continues. In a project with Turin Polytechnic and Aalto University, ETH Zurich is working to produce wall and ceiling components with even lower greenhouse gas emissions. Because one thing is clear: if Switzerland wants to achieve its net zero target by 2050, it needs buildings that cause as little greenhouse gas emissions as possible during construction and use.
Reference
Posani, M, Voney, V, Odaglia, P, Du, Y, Komkova, A, Brumaud, C, Dillenburger, B, Habert, G. Low-carbon indoor humidity regulation via 3D-printed superhygroscopic building components. Nature Communications, 10. Januar 2025. DOI: 10.1038/s41467-024-54944-1.