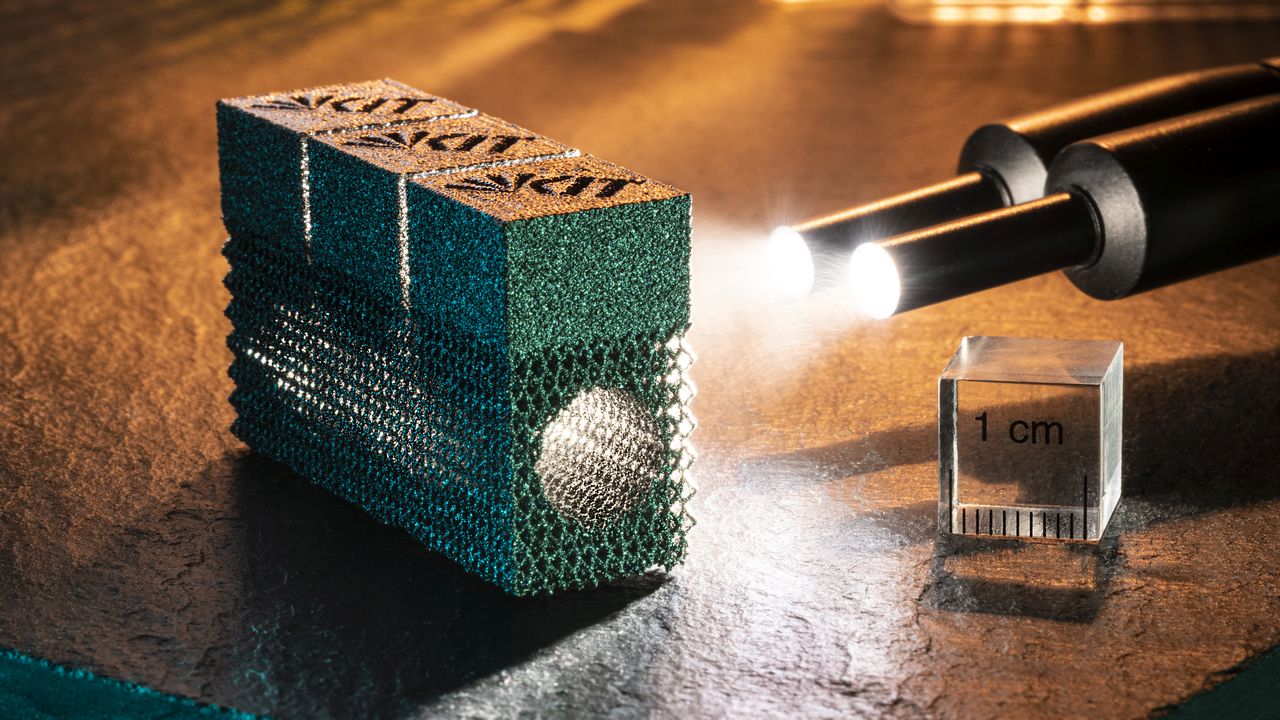
Tungsten has the highest melting point of all metals, 3,422 degrees Celsius. This makes the material ideal for use at high temperatures in e.g. space rocket nozzles, heating elements of high-temperature furnaces, or the fusion reactor. However, the metal is highly brittle and, hence, difficult to process. Researchers of Karlsruhe Institute of Technology (KIT) have developed an innovative approach to making this brittle material soft. To process tungsten, they have determined new process parameters for electron beam melting.
Tungsten is a metal with very attractive properties: It is corrosion-resistant and as heavy as gold. In the form of tungsten carbide, it is as hard as diamond. And it has the highest melting point of all metals, 3,422 degrees Celsius. However, the metal is highly brittle at room temperature. Due to its properties, tungsten is difficult to process using conventional methods. Processing is expensive and time-consuming. An alternative is 3D printing that allows to produce tungsten components that require hardly any finishing. "At the moment, we are working on the additive manufacture of tungsten components by electron beam melting, EBM for short," says Dr. Steffen Antusch from the Institute for Applied Materials - Materials Science and Engineering (IAM-WK) of KIT. The team succeeded in adapting the EBM process to tungsten. Having developed specific process parameters, 3D printing of tungsten components is now possible. "This metal can be applied in many areas. Thanks to its special properties, it is ideally suited for high-temperature applications in energy and light technologies, aerospace industry, and medical engineering. It is indispensable in modern high-tech industry," says Alexander Klein, IAM-WK.
Pre-heating Enables Processing of Brittle Materials
EBM is an additive manufacturing method. Electrons accelerated under vacuum selectively melt metal powder and, in this way, produce a 3D component in an additive way, that is layer by layer. The big advantage of this method consists in the energy source used, the electron beam. It is used to pre-heat the metal powder and the carrier plate prior to melting, as a result of which deformation and inherent stress are reduced. It is possible to process materials that easily break at room temperature and can be deformed at high temperature.
However, the materials used must be electrically conductive. Hence, the process is not suited for ceramic materials, as EBM is based on the principle of electric charging.
Lightweight Titanium Components for KA-RaceIng
Originally, EBM was developed to process titanium alloys and materials needing higher process temperatures. So far, EBM has been used to produce lightweight titanium components for KIT's KA-RaceIng formula student project.
Under research programs of the Helmholtz Association and EUROfusion, the European Fusion Programme, IAM-WK studies materials and processes for future high-temperature applications in the area of fusion energy or medical engineering.
More about the KIT Materials Center: https://www.kit.edu/topics/materials.php
Being "The Research University in the Helmholtz Association", KIT creates and imparts knowledge for the society and the environment. It is the objective to make significant contributions to the global challenges in the fields of energy, mobility, and information. For this, about 9,600 employees cooperate in a broad range of disciplines in natural sciences, engineering sciences, economics, and the humanities and social sciences. KIT prepares its 23,300 students for responsible tasks in society, industry, and science by offering research-based study programs. Innovation efforts at KIT build a bridge between important scientific findings and their application for the benefit of society, economic prosperity, and the preservation of our natural basis of life. KIT is one of the German universities of excellence.