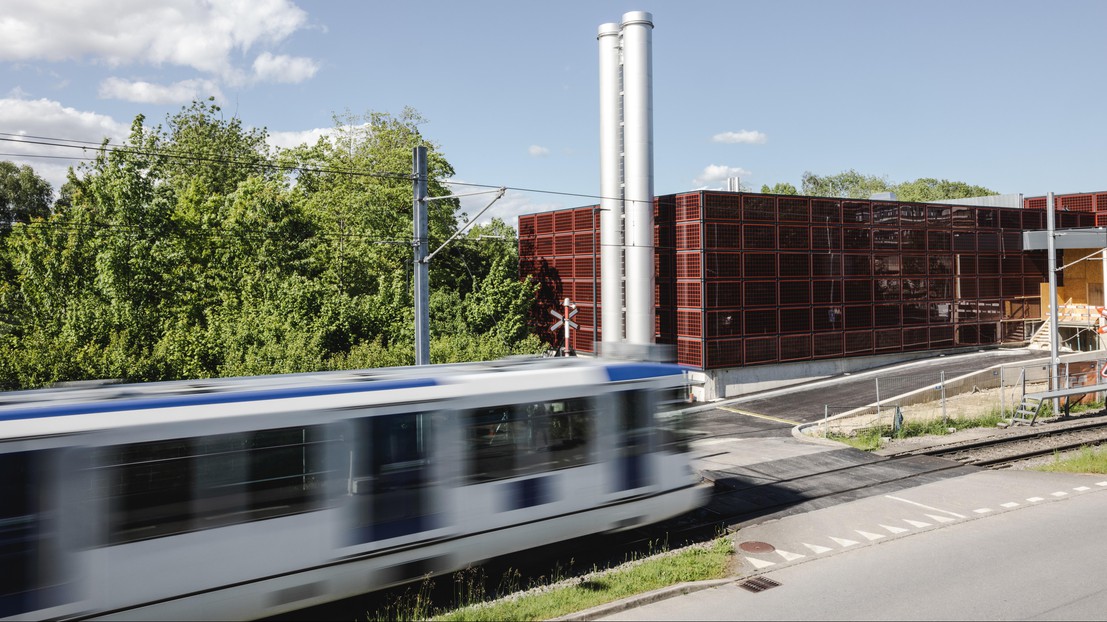
© 2021 Niels Ackermann/Lundi13
EPFL has recently brought an innovative heating plant online and will soon connect it to a large data center. The plant will help the Ecublens campus optimize how it generates and consumes energy, with the goal of achieving carbon neutrality.
Seen from the metro, the new structure's design is quite striking: red blocks clad entirely in solar panels. In reality, this is merely the visible portion of a vast underground network that extends from Lake Geneva to the campus's Innovation Park. Opened this year, EPFL's new heat-pump-powered plant stands out for its aesthetic appeal, innovative approach and energy-saving performance. It will be presented as part of CISBAT 2021, a conference focusing on the energy and environmental efficiency of the built environment, to be held at EPFL from 8 to 10 September.
Adjacent to the building are two chimneys connected to gas boilers. These provided heat to the EPFL campus for two years while the plant was under construction. In the future, they will be used only in the case of a system failure. "The new plant was put to the test one weekend this past February, when the temperature fell below freezing. It passed with flying colors," says Pascal Gebhard, who is part of the Infrastructure group within the Vice Presidency for Operations (VPO). With his colleagues from the construction and operations teams, he has been overseeing the project since it got underway in 2014, and particularly since 2019, when the old heating plant was demolished.
The new plant is attracting a lot of attention, and we get numerous requests for visits. Heat pump technology is gaining ground around Lake Geneva. What's more, thermal waste recovery allows us to close the loop and reuse the water several times. Less water is required, less energy is needed for pumping, and less water is discharged back into the local stream.
Before construction on the new plant got underway, the campus buildings had been using lake water in their heating system since 1985. EPFL has actually been a trailblazer in this field since the late 1970s, when it built its first pumping station for cooling purposes. But during that time, two oil-fired turbines were used to supplement heating needs, particularly following an increase in the number of buildings on campus.
An innovative solution
When it came time to upgrade the outdated heating plant, EPFL's Sustainability Unit - and in particular its former head Philippe Vollichard, who has now retired - pushed hard for an innovative solution. Rather than opting for gas, which would save money in the short run, but at the cost of CO2 emissions, the decision was made to build an integrated system that combined multiple renewable energy sources.
The new pumping station draws water deeper from the lake at a constant temperature of 7°C. It is connected to next-generation heat pumps that raise the water temperature to 50°C thanks to a thermodynamic process that involves compression, condensation, expansion and evaporation, thus delivering significantly better energy performance.
The other major advance is that the plant makes use of thermal waste generated by a data center built on top of it, with server racks whose doors are designed to accommodate filtered industrial water cooled by lake water. This solution is energy-efficient but technically quite bold - normally, water and electronics are best kept far apart.
Cooling the servers to heat the rest of EPFL generates considerable electricity savings, particularly in comparison with the conventional approach of cooling the servers with refrigeration units. In a standard system, 3.3 units of electricity are needed to deliver one unit of electricity to the servers. Here, after factoring in savings in heating, this figure is 1.3 units, a 60% reduction.
What about plant waste?
The innovation doesn't stop there. With solar panels covering the sides and roof of the building and a large space for pilot tests in the works, the plant could one day make use of a nearby composting facility, where plant waste from the neighboring campus's parks and gardens is deposited. A digester for food waste from campus cafeterias could be another step towards small-scale local biogas production.
Nevertheless, the very small quantities of biogas produced would be insufficient to supply all of EPFL's needs, according to David Gremaud, Energy Project Manager at the VP.
The primary purpose of this facility is to treat food waste locally rather than trucking it off site. In addition, it can be used by the academic community for teaching and research purposes.
Energy savings
Switching from the oil-fired turbines to heat pumps will cut EPFL's CO2 emissions by 1,800 metric tons a year. The energy savings from the solar panels will only be marginal, however, since they will generate a total of just 160 kW, whereas a single heat pump requires 2,000 kW. But according to Gianluca Paglia, a project manager for energy systems and construction methods at EPFL's Sustainability Unit, having the solar panels installed directly on the building that houses a heating plant is a rare and instructive example of building-integrated photovoltaics - one of the topics addressed at CISBAT.
The construction work itself was delayed several times due to COVID - but also due to an infiltration of quagga mussels. These creatures, which live in the deep waters of Lake Geneva, colonized the heating system's piping and other equipment. Engineers had to clean out the equipment thoroughly and install a new, removable strainer that allows for easier surface cleaning. They also introduced new filters.
Another issue that had to be dealt with was the discharge of wastewater from the cooling system into the local stream. The engineers designed a mechanism whereby the discharge valves could be regulated so as to preserve the local biotope, paving the way for the canton to approve the project's environmental impact statement.
New data center will soon be up and running
The delays in the new heating plant also affected EPFL's new data center, which is still under construction. The project managers are now waiting for the server racks to be delivered. "We're operating on a tight schedule," says Aristide Boisseau, the head of data center operations at EPFL. The new heating plant will be linked to a 1,000 m² data center that will eventually house 12 rows of servers, including one for the University of Lausanne. The server racks used at the data center will be slightly higher than conventional models and have water-cooled doors. It's a design that's already used in other buildings, but until now only for cooling purposes. The plan is to have the heat generated by the servers recycled into the heating plant, which should start this winter. That will increase the campus' data storage and processing capacity, initially to half capacity at 2 MW, and then to 4 MW.
We don't want to put all our eggs in one basket. We plan to slightly reduce the number of small data centers we have - currently around 30 - and keep the two large ones in the MA and INJ buildings. -
Space for running pilot tests
The last major advantage - and not the least - of the new heating plant is that it will include a large, raised area for running pilot tests. This space will be the size of six badminton courts and span an entire side of the plant's building. Here, engineers will be able to run all kinds of experiments and demonstrations. "Before Philippe left, we made a shortlist of possible projects in the areas of both teaching and research," says François Maréchal, a chemical engineer and professor of mechanical engineering at EPFL.
Indeed, the area lends itself to teaching purposes in a variety of ways, such as to explain system design and comparison, track operations data, reconcile measurements, improve process control and generate forecasts. It also opens the door to an array of synergies between EPFL labs, especially within the School of Engineering. For instance, Maréchal's colleague Jan van Herle, a senior scientist at EPFL's Group of Energy Materials (GEM) in Sion, is working on a fuel cell that can be installed at the heating plant to convert the biogas produced from organic waste into heat and electricity. Jürg Schiffmann, an associate professor at EPFL's Laboratory for Applied Mechanical Design, has developed a new kind of compressor for heat pumps, and Prof. Mario Paolone at EPFL's Distributed Electrical Systems Laboratory has come up with a way of integrating the heating plant into the smart system used to manage the campus' electricity use.
Heating-system design is a field with much promise for the future, and Maréchal is encouraged by how EPFL's own heating plant has evolved over the years.
The technology used at our heating plant isn't necessarily complicated. What makes our plant innovative is the way the different systems are integrated together. It stood out when it was first built 50 years ago and it still does today, making the EPFL campus a benchmark when it comes to sustainable development.
Another promising development is the growing number of students who sign up for Maréchal's class on energy system optimization. In this class, whose size has risen from 15 to 60 students in just a few years, Maréchal uses EPFL's new heating plant as a case study. "Every engineer who is involved in energy systems must have one eye on the energy transition. It's a crucial issue, and a highly motivating one for engineering students. While it requires a lot of work, it also shows students how important it is to analyze systemic ways of incorporating renewable energy in their designs. In the end, they're quite proud of what they achieve."