A research partnership between two Department of Energy national laboratories has accelerated inspection of additively manufactured nuclear components, and the effort is now expanding to inspect nuclear fuels.
Idaho National Laboratory is using a software algorithm developed by Oak Ridge National Laboratory to check for flaws in additively manufactured components as part of the process of identifying promising metals and alloys for 3D printing the next generation of nuclear reactors.
Qualifying new materials and manufacturing technologies for nuclear reactor components can take decades. The collaboration contributes to quicker deployment of new reactor types so nuclear energy can continue to fulfill its potential to create abundant and reliable energy.
The ORNL-developed technology has been so successful that researchers are now training the algorithm to inspect the ceramic casings of irradiated nuclear fuel tested at INL.
"If we use this algorithm to reduce the scan time for radioactive fuels by 90%, it will increase worker safety and the rate we can evaluate new materials," said Bill Chuirazzi, an instrument scientist and leader of INL's Diffraction and Imaging group. The ramifications for the nuclear field extend far beyond the current project. "Down the road, it enables us to expedite the life cycle of new nuclear ideas from conception to implementation in the power grid," he said.
The collaboration between ORNL and INL leverages their strengths to enhance the efficiency of federal nuclear research. Only with the labs' combined resources could they move nuclear parts and materials from creation through testing, which is difficult to achieve elsewhere.
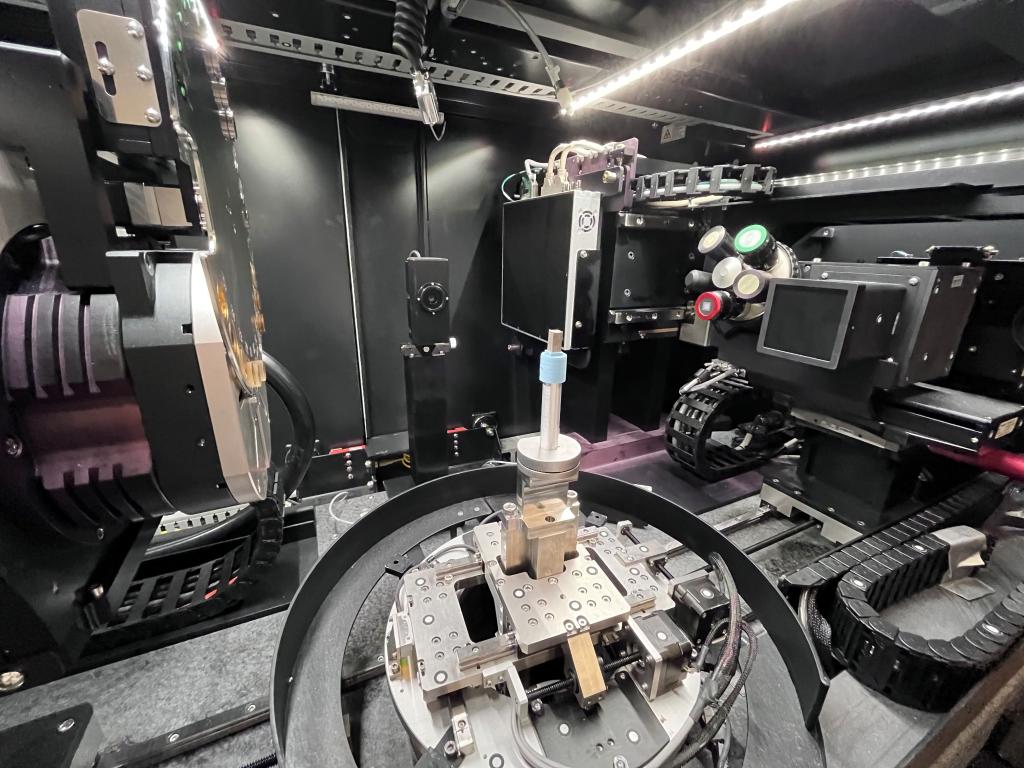
A technology for enhanced inspection
X-ray computed tomography - a CT scan such as those used in the medical field - is used to check the interior quality of 3D-printed objects without damaging them. A series of these X-ray images are combined and reconstructed to reveal the internal structure, identifying weaknesses or printing errors.
However, scanning the same part from many angles can be time-consuming and expensive. ORNL's technology, named Simurgh for a mythological winged beast, offers a solution. Simurgh uses realistic training data to teach a neural network, leveraging physics-based simulations with computer-aided design to reconstruct more accurate images with fewer CT scans than the conventional method. Scan times for very dense materials are now 12 times faster with a fourfold greater ability to detect defects.
ORNL researcher Amir Ziabari and his colleagues developed the technology in 2022 under DOE's Advanced Materials & Manufacturing Technologies Office, or AMMTO, for use with 3D-printed metal parts.
The applications and performance of the technology has since been expanded under the Advanced Materials and Manufacturing Technologies program, or AMMT, in DOE's Office of Nuclear Energy. Through this cross-cutting program, researchers at both labs translated the benefits of Simurgh to the stringent demands of the nuclear field. This has opened a host of new applications, from rapidly characterizing hundreds of nuclear parts and materials to safely inspecting irradiated parts for improving the printing process.
"Nuclear is a high-cost environment with extremely high standards for precision, materials and safety," said Ryan Dehoff, director of DOE's Manufacturing Demonstration Facility, or MDF, at ORNL. "The fact we're using this tool suite in the nuclear sphere speaks to the quality and reliability of the technology."
The MDF, supported by AMMTO, is a nationwide consortium of collaborators working with ORNL to innovate, inspire and catalyze the transformation of U.S. manufacturing.
The recent research partnership began after INL encountered a logistical challenge when trying to link defects to specific printing parameters: Researchers needed to scan more than 30 samples to recognize patterns, but each scan took 30 hours. Before paring down the effort, Chuirazzi consulted ORNL's Ziabari. Licensing his colleague's algorithm enabled collection of all the data in a timely way.
"Including prep, it now takes about 15% of the time it did to scan something with our setup," Chuirazzi said. "We can do three scans in the amount of time it took us to complete one."
Chuirazzi realized that these benefits could be applied to a different nuclear challenge under another federal program that focuses on nuclear fuels.
Scanning radioactive materials
Scanning radioactive nuclear fuels and materials is the specialty of INL's Irradiated Materials Characterization Lab, where Chuirazzi works. An array of shielding and other precautions is required to protect technicians and electronics every time highly radioactive samples move through the lab.
INL researchers often delay examining materials removed from a nuclear reactor to let radioactivity dissipate enough for the safety of lab technicians. Radiation accrued during repeated XCT scans also wears on the detector, limiting its operating life and image accuracy. Shorter scans mean less radiation dosage per scan and less waiting, while enabling higher-quality data and faster feedback to material performance models.
"As Simurgh continues to evolve, it cements its role in X-ray CT imaging, revolutionizing the approach to analyzing complex components with enhanced efficiency, cost-effectiveness and safety," Ziabari said. The tool was initially licensed by ZEISS, a manufacturer of industrial X-ray CT scanners and an ORNL research partner. Ziabari was not surprised when the software framework also proved valuable for nuclear applications. He always envisioned its eventual use with a variety of materials in fields ranging from batteries to electronics.
In the nuclear realm, it could hasten the development and characterization of structural materials and fuels for advanced or high-temperature gas reactors, molten salt reactors and small modular reactors. Among the most promising fuels for new advanced reactor designs is Tri-structural ISOtropic particle fuel, or TRISO. TRISO particles are made up of a tiny fuel kernel encapsulated within a carbon- and ceramic-based material.
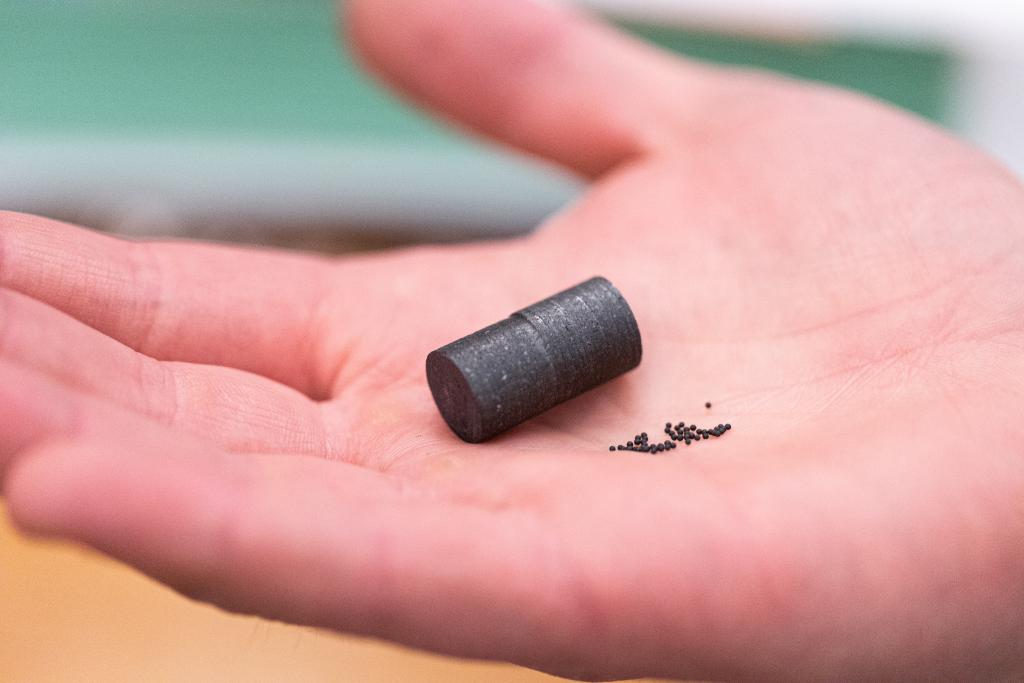
Ziabari is now training Simurgh to process 3D X-ray images of these particles and fuels after they've been irradiated, so INL experts can check for irradiation-induced swelling, cracks, and separation of outer layers. ORNL nuclear researchers are also pursuing opportunities to use the software to identify defects and other features of interest in particles and fuel forms.
This can further pave the way for testing irradiated metal components such as the 3D-printed fuel brackets created at the MDF under the Transformational Challenge Reactor program. These components have been exposed to radiation since 2021 at the Tennessee Valley Authority's Brown's Ferry Nuclear Plant. Once removed from operation, they will be evaluated using Simurgh to reconstruct the X-ray CT data.
The confluence of advanced computational, characterization and irradiated-material handling capabilities across both laboratories will accelerate development of new fuel designs and qualification of materials for 3D-printed nuclear components, helping industry implement new reactors.
About Oak Ridge National Laboratory
UT-Battelle manages ORNL for the Department of Energy's Office of Science, the single largest supporter of basic research in the physical sciences in the United States. The Office of Science is working to address some of the most pressing challenges of our time. For more information, please visit energy.gov/science .
About Idaho National Laboratory
Battelle Energy Alliance manages INL for the U.S. Department of Energy's Office of Nuclear Energy. INL is the nation's center for nuclear energy research and development, celebrating 75 years of scientific innovations in 2024. The laboratory performs research in each of DOE's strategic goal areas: energy, national security, science and the environment. For more information, visit www.inl.gov