Mechanochemistry using a ball mill demonstrates versatility for generating academically and industrially significant organolithium compounds.
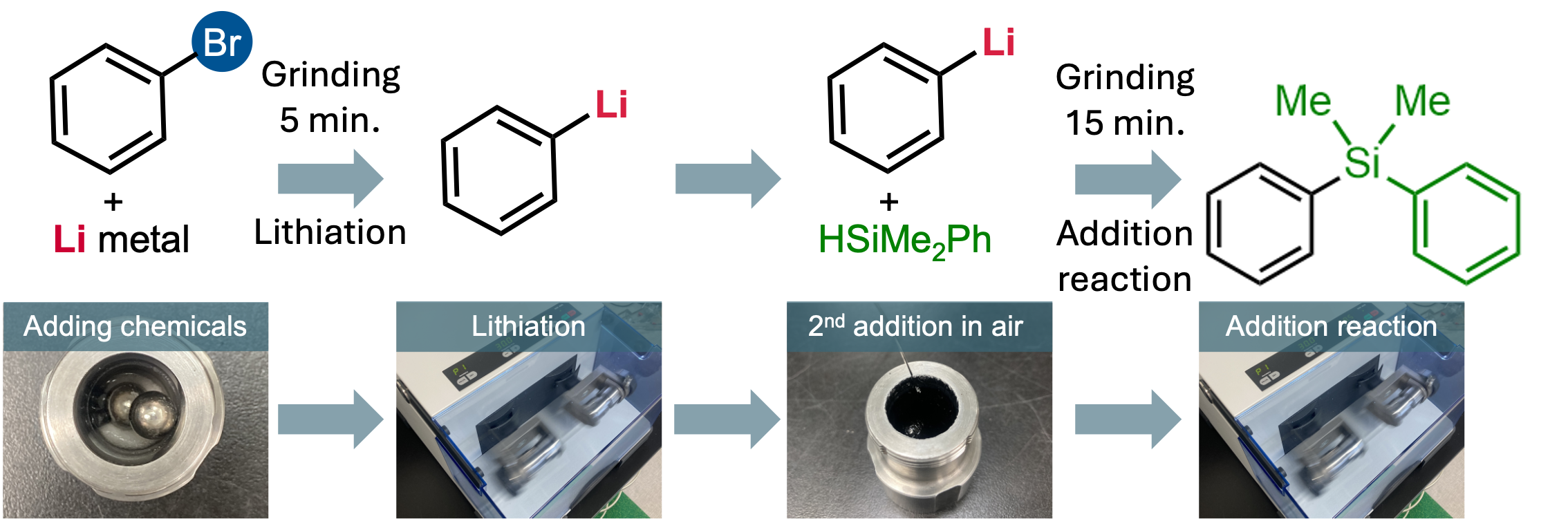
A schematic diagram of the generalized procedure for using a ball mill to perform organolithium reactions (Photo: WPI-ICReDD).
Organolithium compounds, molecules containing a carbon-lithium bond, are excellent precursors for building new carbon-carbon and other carbon-heteroatom bonds. They are widely utilized in both academia and industry for their applications in polymer synthesis, pharmaceuticals, and general organic synthesis. A conventional method for generating organolithiums is done by reacting organohalide compounds, molecules containing a carbon-halogen bond, with lithium metal in an organic solvent. For example, a reaction between 1-bromobutane and lithium metal produces n-butyllithium. Organolithiums are typically unstable and are therefore rapidly converted into a new product in situ after generating them.
Several established synthetic routes towards organolithium compounds require relatively complex reaction set-ups, large quantities of organic solvent, and strict attention towards air, moisture, and temperature sensitivity. As such, access to newly optimized conditions for more straightforward generation of organolithium reagents are in high demand. Using mechanochemistry techniques with a ball-mill, researchers from the Institute for Chemical Reaction Design and Discovery (WPI-ICReDD) at Hokkaido University successfully addressed all these issues. This research was published in the journal Nature Synthesis.
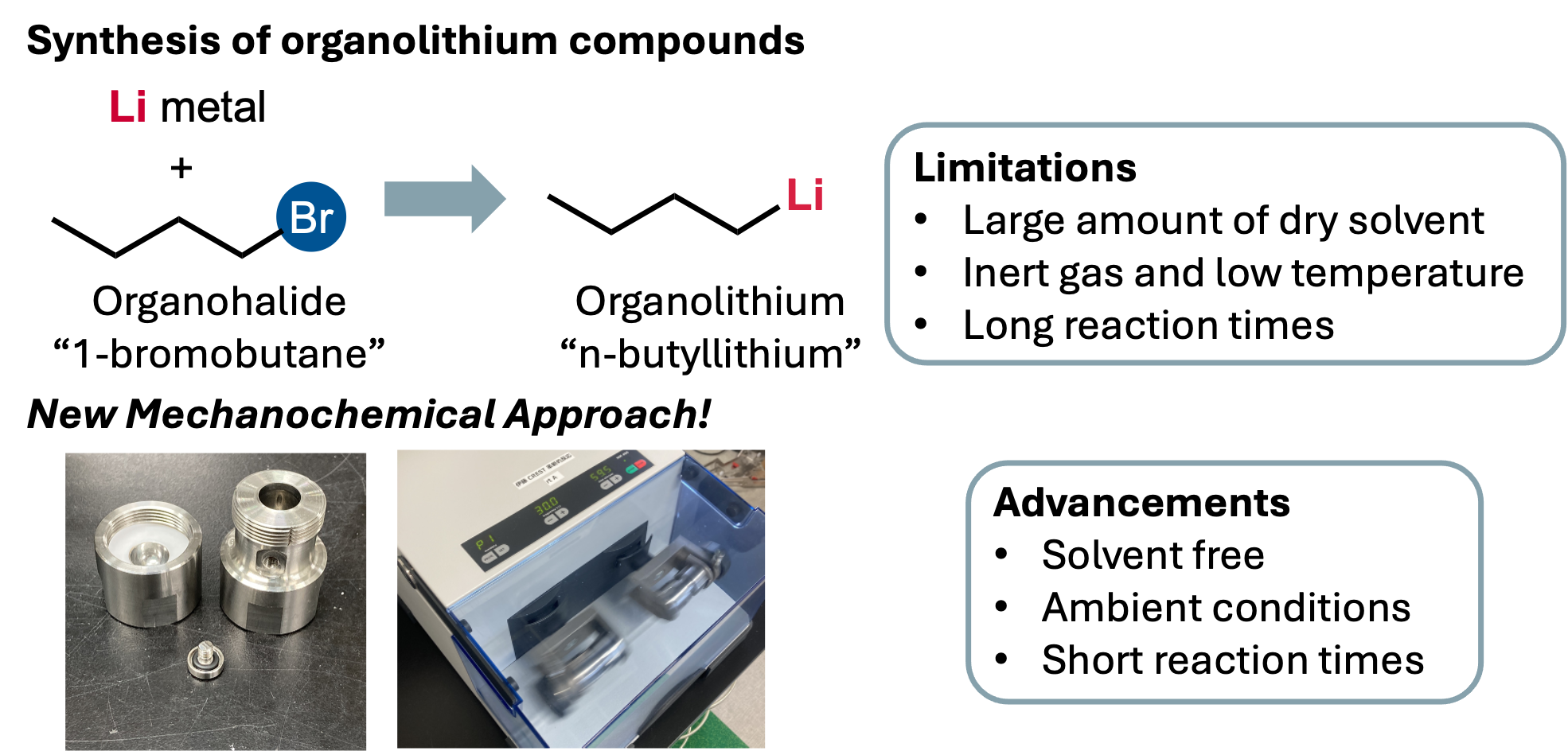
(top) General synthesis of organolithiums and the current limitations. (bottom) Advancements in organolithium transformations using mechanochemistry techniques (Photo: WPI-ICReDD).
"This mechanochemical approach significantly simplifies the synthesis of organolithium reagents, offering an efficient, scalable, and solvent-free method that addresses major challenges in traditional solution-based methods," said Associate Professor Koji Kubota.
Their methodology presents an elegant combination of innovation and simplicity. Pieces of cut-up lithium wire and an organohalide are sealed inside of a milling jar with two balls, without introducing inert gas (nitrogen or argon), and undergo grinding for 5-60 minutes to generate the organolithium. Afterwards, the jar is opened, and a new reagent is introduced to convert the organolithium into a new carbon-carbon bond or carbon-heteroatom bond with 15 minutes of additional grinding.
A representative example demonstrated that 77% conversion into the organolithium could be achieved within 5 minutes. For comparison, the authors further demonstrated that synthesizing the same organolithium using the more traditional solvent-based method under inert gas required 60 minutes to reach 69% conversion, with <5% conversion after 5 minutes. "Our simple protocol, which minimizes the need for extensive care when handling lithium, offers a valuable opportunity for technicians and students with limited experience in organic synthesis to explore reactions involving organolithium species," said doctoral student Keisuke Kondo.
"Our results demonstrate the potential of mechanochemistry to revolutionize synthetic methodologies in organic chemistry by not only improving efficiency but also reducing environmental impact," said Professor Hajime Ito.
Original Article:
Keisuke Kondo, et al. Mechanochemical activation of metallic lithium for the generation and application of organolithium compounds in air. Nature Synthesis. January 21, 2025.
DOI: 10.1038/s44160-025-00753-3
Funding:
This work was supported by the Japan Society for the Promotion of Science (JSPS) KAKENHI (22H00318, 24H00453, 24H01050, 24H01832, 22K18333); the Japan Science and Technology Agency (JST) CREST (JPMJCR19R1) and FOREST (JPMJFR201I), and by the Institute for Chemical Reaction Design and Discovery (ICReDD), which was established by the World Premier International Research Initiative (WPI), MEXT, Japan.