
Shortly after dawn on March 27, 2001, NASA pilot Bill Rieke took off from an airfield just outside of Phoenix in NASA's blue-and-white Learjet 25 and flew low over a series of microphones for the first flight test of a groundbreaking NASA technology.
On one of the plane's engines was an experimental jagged-edged nozzle that researchers at Glenn Research Center in Cleveland had discovered made aircraft significantly quieter. These initial flight tests were an important step toward using these "chevron nozzles" on modern aircraft, lowering noise levels for communities.
NASA Glenn has been exploring ways of reducing engine noise since the first jet airliners appeared in the 1950s. New turbofan engines in the 1960s were quieter, but the expansion of the overall airline industry meant that noise was still an issue. With the introduction of noise-limiting mandates in the 1970s, NASA and engine manufacturers embarked on a decades-long search for technologies to lower noise levels.
NASA researchers discovered that the military's use of rectangular notches, or tabs, along an engine nozzle's exit - to help disguise a jet fighter's infrared signature - could also reduce engine noise by helping mix the hot air from the engine core and the cooler air blowing through the engine fan. In the 1990s, Glenn researcher Dennis Huff and his colleagues discovered that a serrated, or sawtooth, shape, referred to as a chevron, offered more promise.
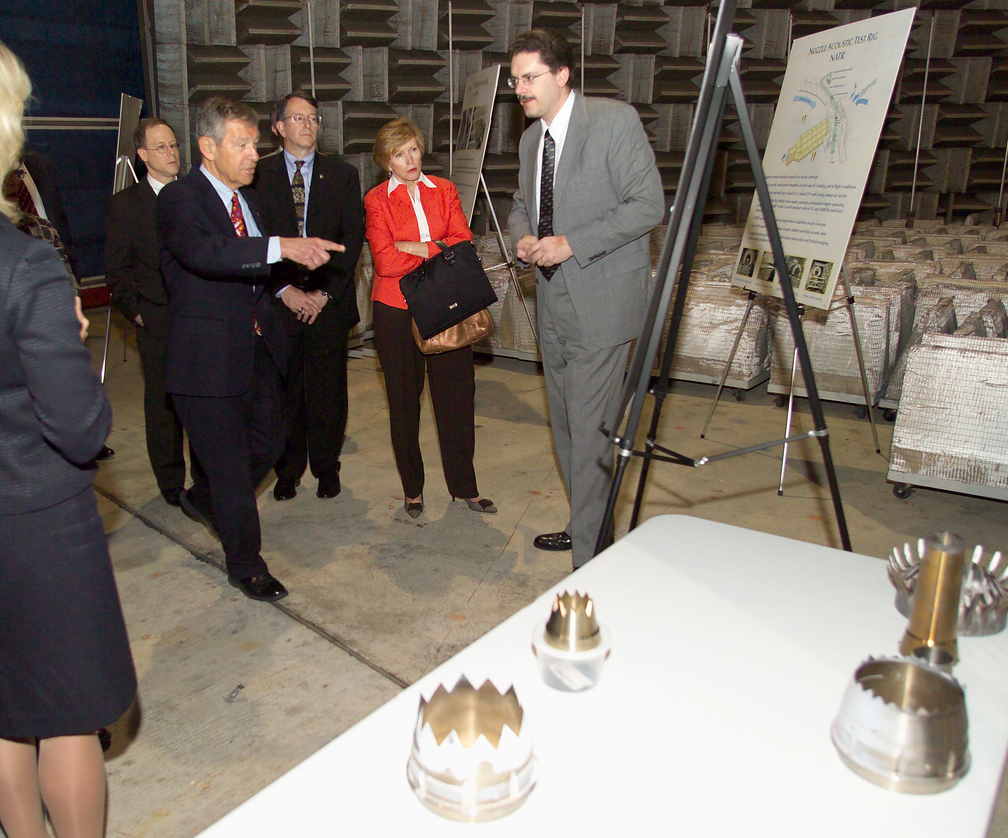
NASA contracted with General Electric and Pratt & Whitney to develop an array of tab and chevron designs to be analyzed in Glenn's unique Aero-Acoustic Propulsion Laboratory (AAPL). Extensive testing in the spring of 1997 showed the possibilities for reducing noise with these types of nozzles.
Engine manufacturers were impressed with the findings but wary of any technology that might impact performance. So, in 1998, NASA funded engine tests of the 14 most promising designs. The tests revealed the chevron nozzle had a negligible 0.25% reduction of thrust. It was a major development for jet noise research.
In September 2000, Glenn's Flight Operations Branch was contacted about the logistics of flight-testing chevron nozzles on the center's Learjet 25 to verify the ground tests and improve computer modeling. Nothing further came of the request, however, until early the next year when Huff informed Rieke, chief of Flight Operations, that the researchers would like to conduct flight tests in late March-with just eight weeks to prepare.
Glenn's Acoustics Branch worked with colleagues at NASA's Langley Research Center in Hampton, Virginia, and the Arizona-based engine manufacturer Honeywell on the effort. They planned to conduct testing at Estrella Sailport just outside of Phoenix from March 26 to 28, 2001.
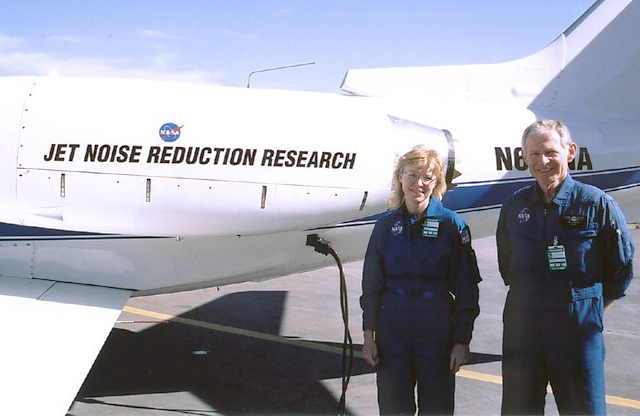
With the required safety and design reviews, the eight-week target date would be difficult to meet for any test flight, but this one was particularly challenging as it involved modifications to the engine nacelle. While the special nozzle engineers created for the flights would allow them to switch between a six- and a 12-chevron design during testing, it also got hot quickly. This necessitated the installation of new sensors, rewiring of fire alarm cables, and the presence of an onboard test engineer to monitor the temperatures. The short turnaround also required expedited efforts to obtain flight plan approvals, verify the plane's airworthiness, and perform normal maintenance activities.
Despite the challenges, Rieke and a small team delivered the Learjet to Estrella on March 25, as planned. The next day was spent coordinating with the large Langley and Honeywell team and acquiring baseline noise data. The pilots idled the unmodified engine as the Learjet flew over three perpendicular rows of microphones at an altitude of 500 feet and speed of 230 miles per hour.
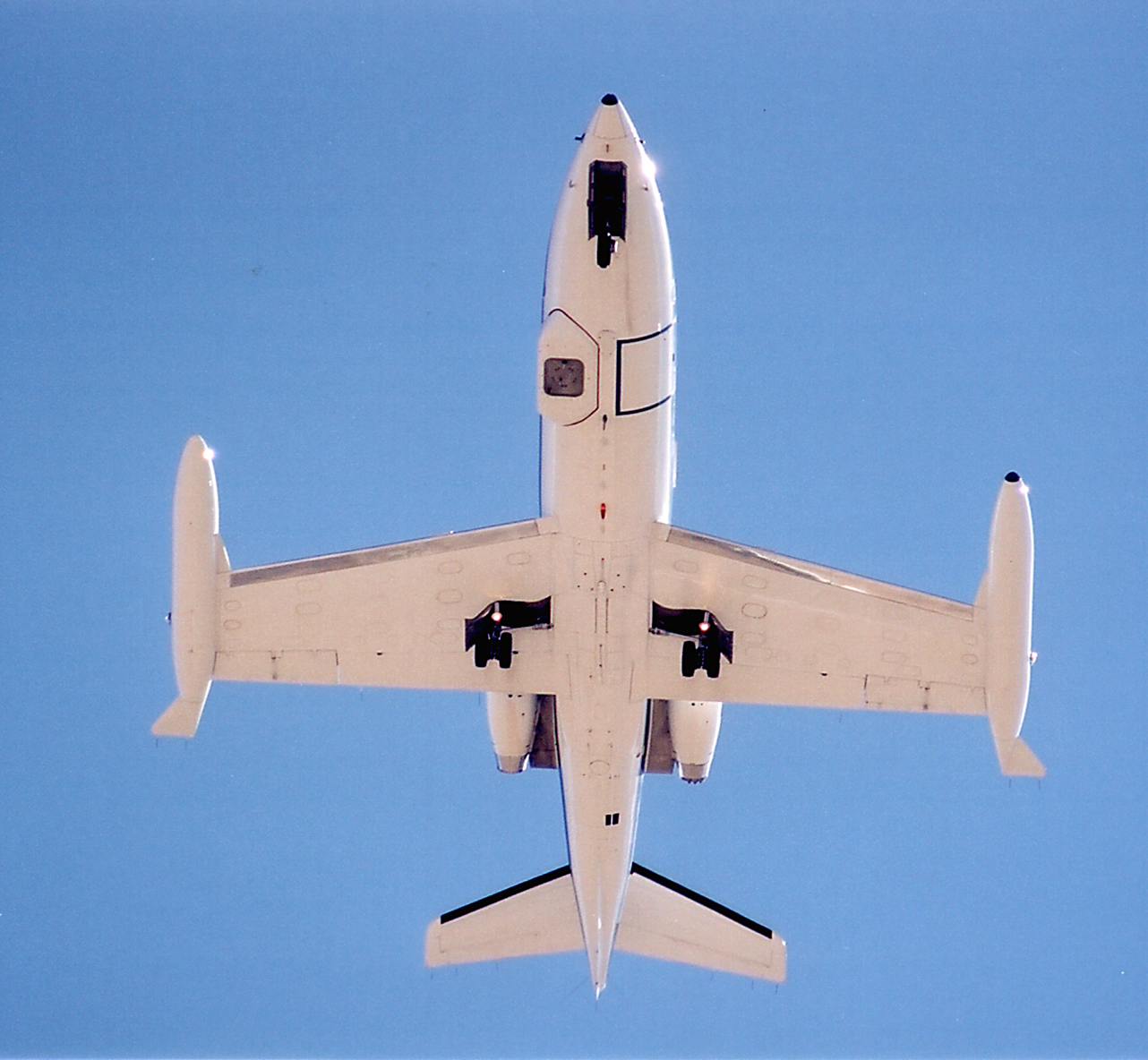
The flight patterns were repeated over the next two days while alternately using the two variations of the chevron nozzle. The researchers anecdotally reported that there was no perceptible noise reduction as the aircraft approached, but significant reductions once it passed. Recordings supported these observations and showed that sideline noise was reduced, as well.
The flights of the Learjet, which was powered by a variation of GE's J-85 turbojet, were complemented by Honeywell's turbofan-powered Falcon 20 aircraft. These flights ultimately confirmed the noise reduction found in earlier AAPL tests.
Overall, the flight tests were so successful that just over a year later the FAA began certifying GE's CF34-8, the first commercial aircraft engine to incorporate chevron technology. The engine was first flown on a Bombardier CRJ900 in 2003. Continued studies by both NASA and industry led to the improved designs and the incorporation of chevrons into larger engines, such as GE's GEnx.
According to Huff, the chevron's three-decibel noise decrease was analogous to the difference between running two lawnmowers and one. Their comparatively easy integration into engine design and minimal effect on thrust made the chevron a breakthrough in noise-reduction technology. In 2002, NASA presented an innovation award to the Glenn, Langley, and Honeywell team that carried out the flights. Today, airliners such as the 737 MAX and 787 Dreamliner use chevron nozzles to lower noise levels for communities near airports.