Case Western Reserve researcher on team that prints 3D model to prove importance of 'transverse struts' to long-term structure life
New bone-structure research from scientists at Case Western Reserve, Cornell and Purdue universities could give new hope to patients suffering from osteoporosis-and surprising insight that could someday lead to lighter, more durable airplane wings.
For decades, scientists studying osteoporosis have used X-ray imaging to analyze the structure of bones and pinpoint strong and weak spots. Density is typically linked to bone strength, and in assessing that strength, most researchers examine how much load a bone can handle all at once.
But a research team led by Cornell scientist Christopher J. Hernandez has discovered how so-called "transverse struts," previously understood as a minor aspect of the bone's internal structure, can be strengthened to withstand repeated wear and tear.
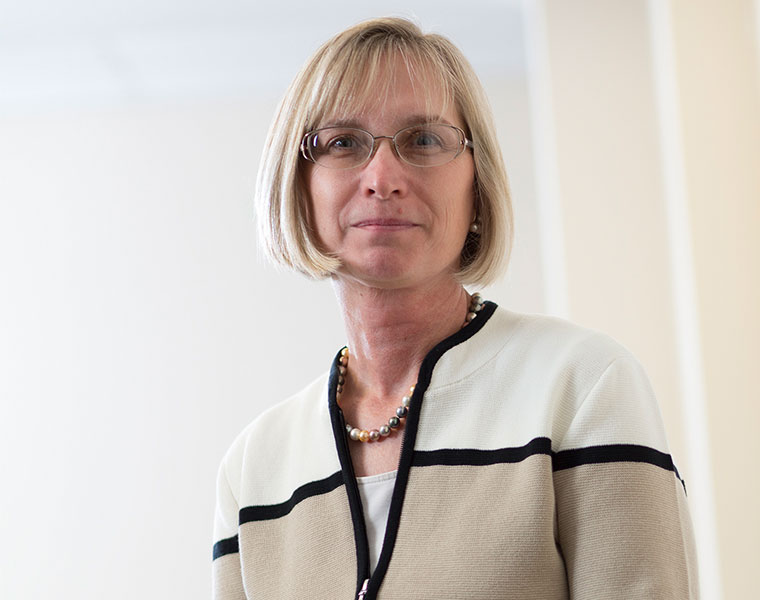
The work was in collaboration with Case Western Reserve University Distinguished University Professor Clare Rimnac.
"The breakthrough here is in gaining a better understanding of the importance to fatigue life of those transverse struts, which are perpendicular to the main, vertical struts," said Rimnac, the Wilbert J. Austin Professor of Engineering in the Department of Mechanical and Aerospace Engineering at Case Western Reserve. "This research has shown us that by making judicious and sometimes relatively modest changes to those struts, you can extend the life of the structure-whether it's a bone or something like an airplane wing."
Rimnac, whose research over more than 30 years has dramatically helped orthopaedic-implant manufacturers improve the performance of replacement knee and hip joints, was asked to consult on the project by Hernandez, a fomer colleague at Case Western Reserve.
The team's paper explaining its findings, "Bone-Inspired Microarchitectured Materials with Enhanced Fatigue Life," was published this month in the Proceedings of the National Academy of Sciences. A video explaining the work was also posted on the Cornell Chronicle website.
Understanding fatigue
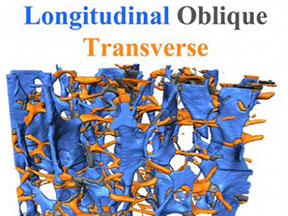
Hernandez, an associate professor in the Sibley School of Mechanical and Aerospace Engineering and in the Meinig School of Biomedical Engineering at Cornell, said he is particularly interested in long-term fatigue life, or how many cycles of loading a bone can bear before it breaks.
"The best way to understand the fatigue properties of material is to think about a part in your car that breaks every so often, so you have to take it to the shop," he said. "Well, why did it break? It was clearly strong enough, because it worked for months, years, just fine. But after cycling and cycling and cycling, tens of millions of cycles, it breaks.
"We've known about this property of materials for 150 years and it's embedded in the design of everything we do," he said. "But not too many people had done this kind of study of the bone."
The team used a new computer software to perform a deeper analysis of a bone sample and a 3D printer to manufacture bone-inspired material made from a urethane methacrylate polymer. By varying the thickness of the transverse struts, the resesearchers increased the material's fatigue life by up to 100 times.
"The amazing thing is that we did this by adding very little additional weight to the 3D-printed structure," Rimnac said. "Just by increasing the thickness of the transverse struts by 20 microns or 60 microns, the fatigue life can be increased by 1,000 cycles to even 100,000 cycles. That's a big deal."