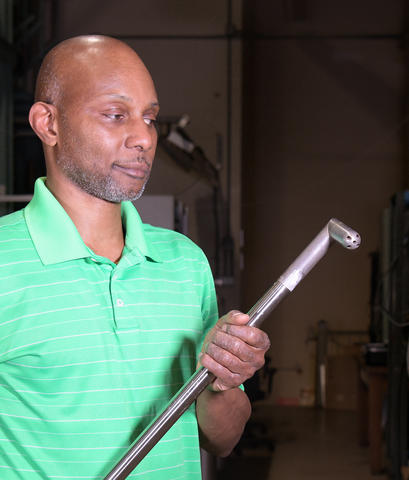
NIST's Aaron Johnson holding the new NIST pitot tube, which improves measurements of smokestack flow during audits without increasing the amount of time it takes to do the audit.
Jennifer Lauren Lee/NIST
Each year, to meet requirements set by the Environmental Protection Agency (EPA), coal-fired power plants must have their smokestack emissions audited by an independent third party. NIST researchers wanted to help auditors improve these measurements without making the audits longer or more complicated to complete.
A few years ago, a NIST team designed new probes for sensing emission flows and a new measurement method that improves accuracy while also speeding up measurements of smokestack flow by a factor of five compared to similar probes.
But though the new probes were promising, in real-world tests in actual smokestacks, NIST researchers identified two significant design problems.
Now, the team has addressed those two remaining issues, meaning the new probes are good candidates to become the new standard probe used in smokestack audits.
"These were the last major obstacles standing in the way of the new design and testing protocol being economical and practical for smokestack testing applications," said NIST researcher Aaron Johnson. "We're pleased by this latest development and working to support the next steps in the recommendation process."
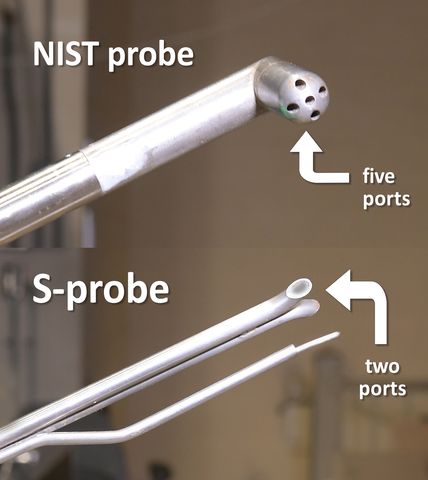
Jennifer Lauren Lee/NIST
The probes used by auditors to monitor smokestack emissions are called pitot tubes, long skinny hollow cylinders that measure the rate at which flue gas is emitted. Auditors insert the pitot tubes horizontally into the smokestack and measure the velocity of the flow at several different locations.
The style of pitot tube used most often by auditors is called an S-probe. It has two holes, or ports, facing in opposite directions. The faster the gas flow, the higher the pressure difference between the two ports; measuring this difference in pressure allows auditors to calculate the flow's speed.
S-probes don't require calibration (though many stack testers do calibrate their S-probes). And measurements can be done fairly quickly. But because S-probes only have two ports, there are some limitations to their accuracy.
Smokestack emissions often contain eddies and swirls that complicate the measurement process, since flow is not necessarily traveling directly upward at the point being tested. Because S-probes only have two ports, they are only capable of one-dimensional or at best two-dimensional measurements, and therefore there is a lot of information about the flow that they might be missing. As a result, S-probes can have significant errors when the flow has significant swirl.
Another type of probe that, on paper, could provide auditors with better measurements is a 3D probe. It has five ports instead of two and is capable of 3D measurements, which give auditors more information about the complex flows inside the smokestacks.
But the 3D probes, along with their associated testing protocols sanctioned by the EPA, can be difficult to use: Their ports, much smaller than those in S-probes, are more readily clogged with smokestack debris. In addition, smokestack testers must manually rotate the probe during each measurement, because the probe's accuracy relies on the head pointing directly into the flow. But this is a time-consuming process, due to the complex eddies and swirls within the smokestack.
As a result, few smokestack testers use these probes and favor the less accurate but more user-friendly S-probes.
"Industry values a robust probe," Johnson said. "If auditors have to fiddle with it to get a good measurement, they're not going to use it."
To address this issue of probes being either accurate or easy to use but not both, NIST created an alternative style of pitot tube, designed by NIST physicist Iosif Shinder. It has a hemispherical face and five holes, which allows it to make a 3D measurement. But unlike previous models capable of 3D measurements, the NIST probe, when calibrated, can measure flow accurately without requiring auditors to perform complicated probe rotations in the stack.
The result is a pitot tube that is robust enough to be used in the field, that provides high-accuracy measurements, and that is five times faster than the conventional 3D probe measurements that required stack testers to rotate the probe in the stack.
But there have been some caveats. After testing their new probe in real smokestacks, researchers found that the five ports at the tip of their probe got plugged easily by ash and water droplets. This clogging would have required testers to purge the tubes during use, which would have added time to audits.
NIST has now fixed this problem by making the holes on the surface of the probe several times larger, increasing their size from about 2 to 3 millimeters to 6.5 millimeters (about a quarter of an inch).
Another issue in the NIST design was that, unlike the simpler S-probes, each NIST probe had to be intensively calibrated - with a total of 3000 separate measurements in a wind tunnel - before it could be taken into the field.
"This is much more calibration than is feasible for commercial uses," said Shinder. "We needed to simplify the calibration process or these pitot tubes would not be useful to the community."
NIST's solution involved using statistical tricks to identify which data they really needed for the calibrations. In the end, they discovered that only 130 "judiciously selected" points (combinations of angles and air velocities in a wind tunnel) are enough to yield the high accuracies they were aiming for.
The American Society of Mechanical Engineers (ASME), an organization that acts as a source of standards, is currently drafting a documentary standard to facilitate the EPA's adoption of this new NIST probe design for stack flow measurements, which would make it the official recommendation to auditors. The NIST design has also been awarded a patent.
-- Reported and written by Jennifer Lauren Lee
Paper: I.I. Shinder, A.N. Johnson, B.J. Filla, V.B. Khromchenko, M.R. Moldover, J. Boyd, J.D. Wright, and J. Stoup. Non-nulling Protocols for Fast, Accurate, 3-D Velocity Measurements in Stacks. Journal of Air and Waste Management. Published online July 28, 2023. DOI: 10.1080/10962247.2023.2218827.