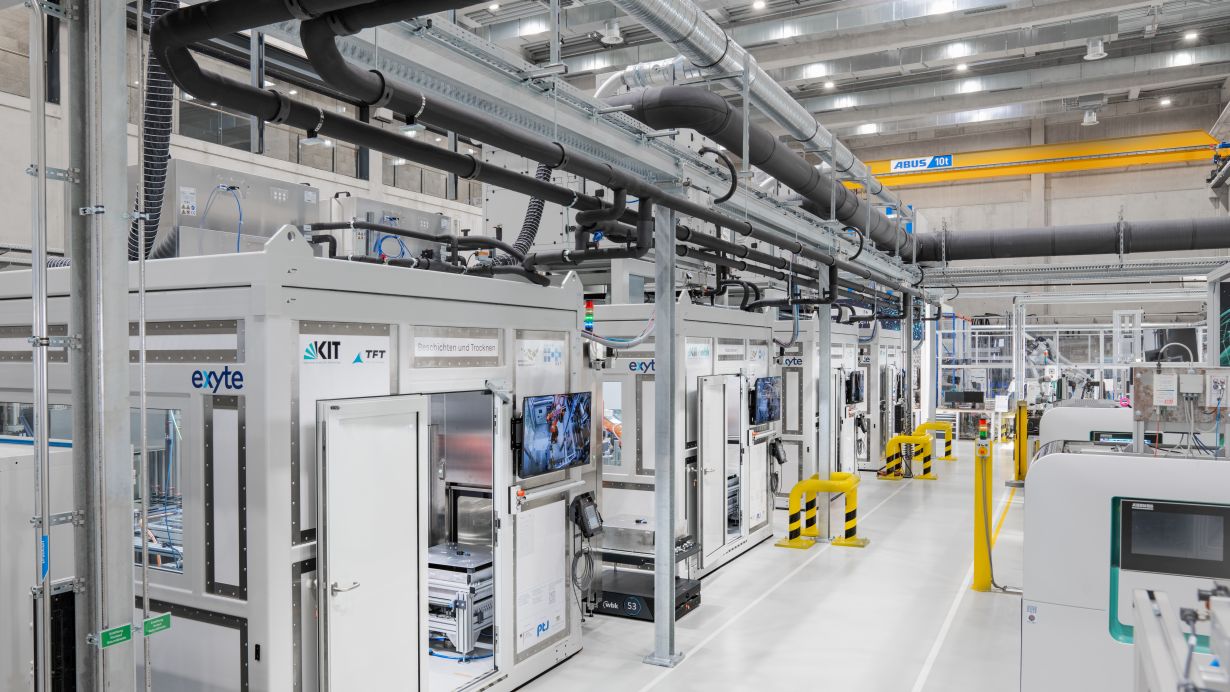
In an effort to make the future production of battery cells (for uses such as electromobility or power tools) more flexible, researchers at the Karlsruhe Institute of Technology (KIT) have set up an agile battery cell production system. Using a highly flexible robotic automation system, they have reached a level of flexibility previously achievable only with manual cell production. This will enable companies to adapt to new technologies and volatile markets more quickly and can boost Germany's industrial competitiveness. The project received EUR 19 million in federal and state funding.
According to Germany's Federal Ministry for Economic Affairs and Climate Action, battery cells are gaining in importance as a versatile and efficient means of storing energy. They are a driving force in advancing electromobility, for example, and a key technology of great strategic and economic significance for manufacturing companies. Current demand is mainly met through cost-driven mass production in Asia and North America, which also affects the mechanical and plant engineering sectors. "In Germany we don't have the conditions to be competitive in purely cost-driven mass production of cells and the associated mechanical engineering," said Professor Jürgen Fleischer, Head of KIT's wbk Institute of Production Science. "Opening the world's first agile battery cell production system in the Karlsruhe Research Factory shows how we can stand out in the world market with highly flexible and resource-efficient production while targeting the high-margin premium segment and niche markets."
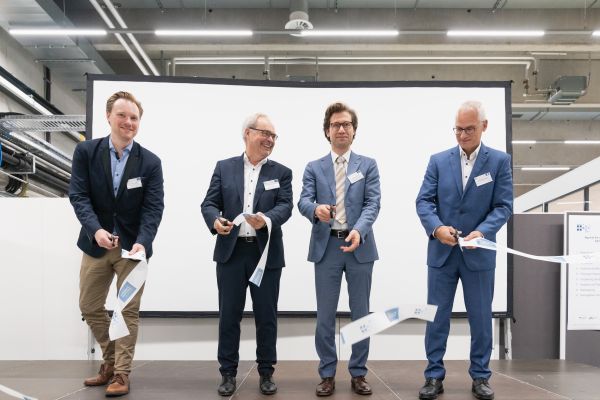
Ministry and KIT representatives at the ribbon-cutting ceremony for the new agile battery cell production system in the Karlsruhe Research Factory; guests from industry, academia and government were in attendance. Left to right: Stefan Jung, Federal Ministry of Education and Research; Jürgen Fleischer, KIT; Ronny Feuer, Baden-Württemberg Ministry of Science, Research, and the Arts; Joachim Knebel, KIT.
(Foto: Amadeus Bramsiepe, KIT)
Flexible and Resource-efficient Battery Cell Production
In cooperation with Exyte, a German engineering company, KIT researchers developed special robot cells. "In this field, they're the first of their kind worldwide. They act as local dry rooms, or microenvironments, to protect moisture-sensitive battery materials," said Fleischer. He added that the volume needing to be dehumidified is considerably smaller than in conventional dry rooms, meaning this technology has especially high potential for reducing energy consumption. With their associated process modules, four such microenvironments constitute the agile battery production system's physical configuration in the Karlsruhe Research Factory.
The project team also created a "digital twin" (software-based simulation) of the production system, which will allow the scientists to analyze the scale effects of replicating individual microenvironments and to determine values for production-related variables such as optimum batch sizes. The simulation can also be used to plan the agile battery cell production system's output. The physical system is connected with a database so that all processes can benefit from AI-based adaptations and improvements in the future.
Close Cooperation Between Academia and Industry
The researchers in the AgiloBat project developed the battery cell production system in cooperation with medium-sized mechanical and plant engineering companies. The project will enable the companies to jointly supply competitive systems for the entire process chain. KIT's contribution of process expertise for more flexible and modular systems will also help the companies to establish automated and resource-efficient production of a wide variety of battery cells and to test new material systems using industrial processes with small amounts of material. The infrastructure developed during the project enhances the battery cell research infrastructure built up at KIT since 2011.
More about AgiloBat
Researchers from seven KIT institutes are working on the AgiloBat research project with partners from the Center for Solar Energy and Hydrogen Research Baden-Württemberg and the Fraunhofer Institute for Chemical Technology. In the mechanical and plant engineering sectors, Coperion GmbH, SAUERESSIG Group, Schunk Group, Herrmann Ultraschalltechnik GmbH & Co. KG, Siemens AG, DEHOF ingenieur+technik and Exyte Technology GmbH are also involved.
The project has received funding from Germany's Federal Ministry of Education and Research (EUR 14.5 million) and Baden-Württemberg's Ministry of Science, Research, and the Arts (EUR 4.5 million). (kla)
More information:
https://www.wbk.kit.edu/english/index.php
https://inzepro-cluster.de/projekt/agilobat2/ (in German)
https://www.karlsruher-forschungsfabrik.de/en.html
Being "The Research University in the Helmholtz Association", KIT creates and imparts knowledge for the society and the environment. It is the objective to make significant contributions to the global challenges in the fields of energy, mobility, and information. For this, about 10,000 employees cooperate in a broad range of disciplines in natural sciences, engineering sciences, economics, and the humanities and social sciences. KIT prepares its 22,800 students for responsible tasks in society, industry, and science by offering research-based study programs. Innovation efforts at KIT build a bridge between important scientific findings and their application for the benefit of society, economic prosperity, and the preservation of our natural basis of life. KIT is one of the German universities of excellence.