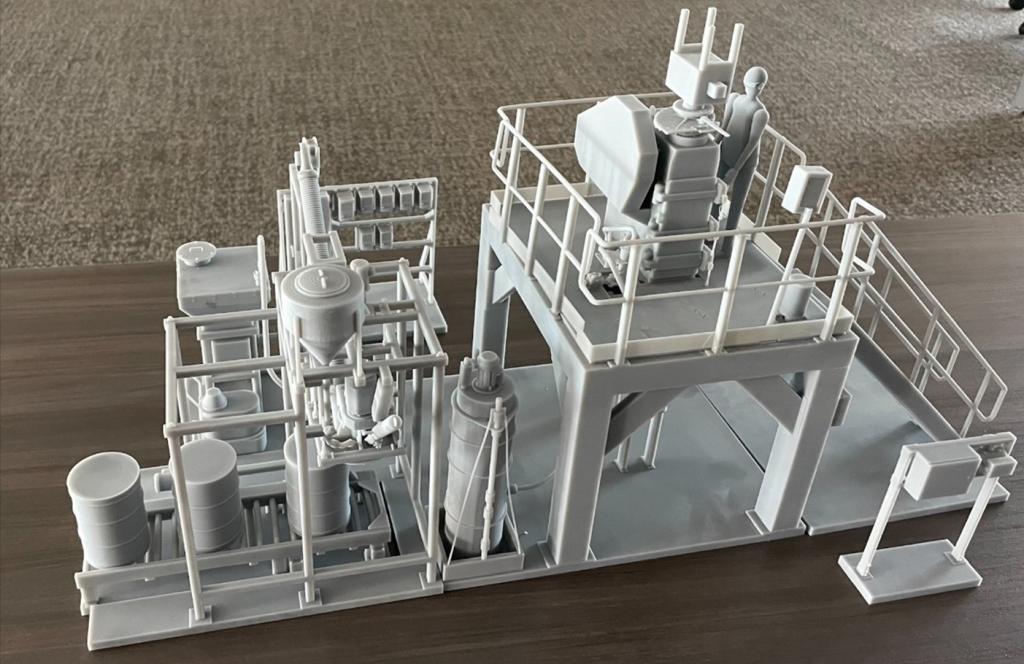
Kris Gaines is on a nonproliferation mission: to make it easier for more countries to eliminate highly enriched uranium, or HEU, thus neutralizing the inherent threat of its potential for nefarious use. As a nuclear nonproliferation specialist and project manager at the Department of Energy's Oak Ridge National Laboratory, Gaines leads aspects of an important project designed to eliminate spent HEU fuel from Kazakhstan.
Developed through a collaboration with the National Nuclear Security Administration (NNSA), the International Atomic Energy Agency (IAEA), Idaho National Laboratory, ORNL, and the National Nuclear Center (NNC) of the Republic of Kazakhstan - owner of the Impulse Graphite Reactor (IGR) and its fuel, on which the project is centered - this new technology is a promising solution for safeguarding spent HEU fuel around the world.
Fueling reactors such as the Kazakh IGR requires HEU, which has been "enriched" to contain greater than or equal to 90% of the fissile U-235 isotope, as opposed to low-enriched uranium, or LEU (equal to or less than 20%). This more potent HEU enables a range of vital materials research and scientific exploration. However, once this fuel has been used and is removed from the reactor, it is known as "spent" fuel, which remains radioactive and must be safely stored or reprocessed into safer forms.
Once it is spent, or irradiated, the ability to down-blend it into otherwise useful material is complicated. To address these challenges and decrease risks posed by the IGR's spent fuel, NNSA, DOE and the Kazakhstan Ministry of Energy collaborated to find a solution for in-country elimination of the spent HEU fuel. The result is a unique new down-blending and cementation technology that readies the fuel for safe, long-term storage.
"Due to the type of fuel, other down-blending technologies like 'melt dilute' aren't feasible options because graphite fuel won't melt," said Gaines. "This fuel will be repackaged for batch operations and sent through a large crusher/grinder until it is ground into very fine particles and mixed with natural or depleted uranium to down-blend it from ≥90% to ≤5% enrichment. The fuel is then transferred to a sealed drum at the mixing and cementation station, where it will be mixed with cement and other additives by in-drum mixing paddles to create unrecoverable, uniformly dispersed low-level waste as a concrete-filled drum."
This first-of-its-kind technology helps to dramatically decrease risks posed by the spent HEU, lowering its enrichment level far below the LEU threshold of 20%. Down-blending irradiated graphite fuel removes the need for IAEA safeguards and renders it virtually unrecoverable through cementation.
Though the new technology is not yet in place permanently, the necessary equipment has been fabricated and installed at a temporary location in Kazakhstan. Plans for the new technology's use there include continued development of the permanent destination facility, ongoing operator training programs and continual fabrication of mixing drums for further use in the process before the system is moved to its intended site.
Gaines is encouraged by the new process and its potential for use elsewhere with other types of fuels. "This technology is already being considered for the fuel from Kazakhstan's other reactor, IVG.1M. We are currently working with NNC to conduct experiments on both melt-dilute and oxidation of this fuel. Preliminary results show that oxidation may be the best option, as the oxidized powder would then be run through the same system we are using for the IGR fuel," he said.
Prior to implementation and wider use of the new technology, however, the team needed to convince key stakeholders that their solution was effective, safe and affordable. An idea to communicate these benefits through a scaled-down, 3D-printed physical model set the stage for an impressive partnership at ORNL - one with significant international impact.
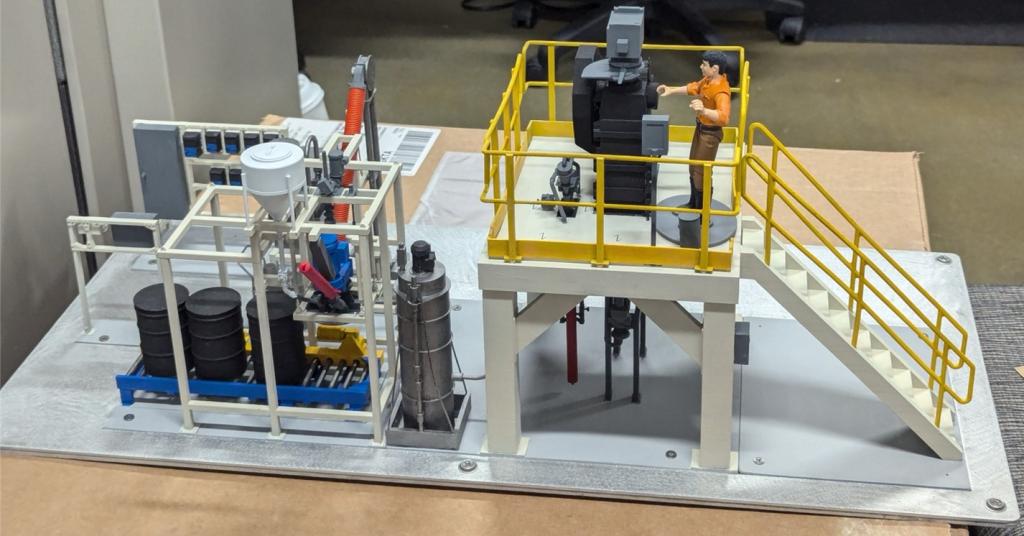
At the NNSA sponsor's suggestion, Gaines teamed up with ORNL's Amiee Jackson, a mechanical engineer at the lab's Manufacturing Demonstration Facility , or MDF, to deliver an accurate scale model of the Kazakh NNC's IGR, highlighting its new down-blending and cementation technology. Over the span of a month, Jackson painstakingly converted the IGR's original engineering files into printable, 1:16th scale files. Jackson then oversaw the process of printing the models.
"The original models were a blend of solid and surface geometry, with all sorts of hollow bits and far more detail than was necessary," Jackson said. "My work was to 'Boolean union' everything [create a new shape from many others, with stable intersections preserving overall integrity], getting rid of any hollow areas, ensuring that scaled wall thicknesses were thick enough to be printable, and then coordinating printing."
The resulting 3D model was displayed at the International Conference on Nuclear Security, or ICONS, in Vienna in May. Attendees indicated they were impressed, not only by the accuracy of the 3D model itself, but also by the news of the system's effectiveness, affordability and ease of assembly and deployment.
"How to eliminate irradiated/spent graphite fuel has long been an issue. This technology answers that question and is now being considered for eliminating other fuel types," Gaines said. "It offers a previously unavailable, safe and effective solution to a longstanding problem. Its affordability and cost-effectiveness are a bonus."
The MDF, supported by DOE's Advanced Materials and Manufacturing Office, is a nationwide consortium of collaborators working with ORNL to innovate, inspire and catalyze the transformation of U.S. manufacturing.
UT-Battelle manages ORNL for the Department of Energy's Office of Science, the single largest supporter of basic research in the physical sciences in the United States. The Office of Science is working to address some of the most pressing challenges of our time. For more information, visit energy.gov/science . - Chris Driver