Billions of tons of plastic waste clutter our world. Most of it has accumulated on the ground and in the oceans or disintegrated into tiny particles known as microplastics that pollute the air and the water, penetrating vegetation and the bloodstreams of humans and other animals. The scope of the danger posed by plastics grows with each passing year, since they are made from massive molecules, known as polymers, that do not readily biodegrade. Currently, biodegradable plastics make up less than one-fifth of the total amount of plastic produced, and the processes needed to break them down are relatively cumbersome.
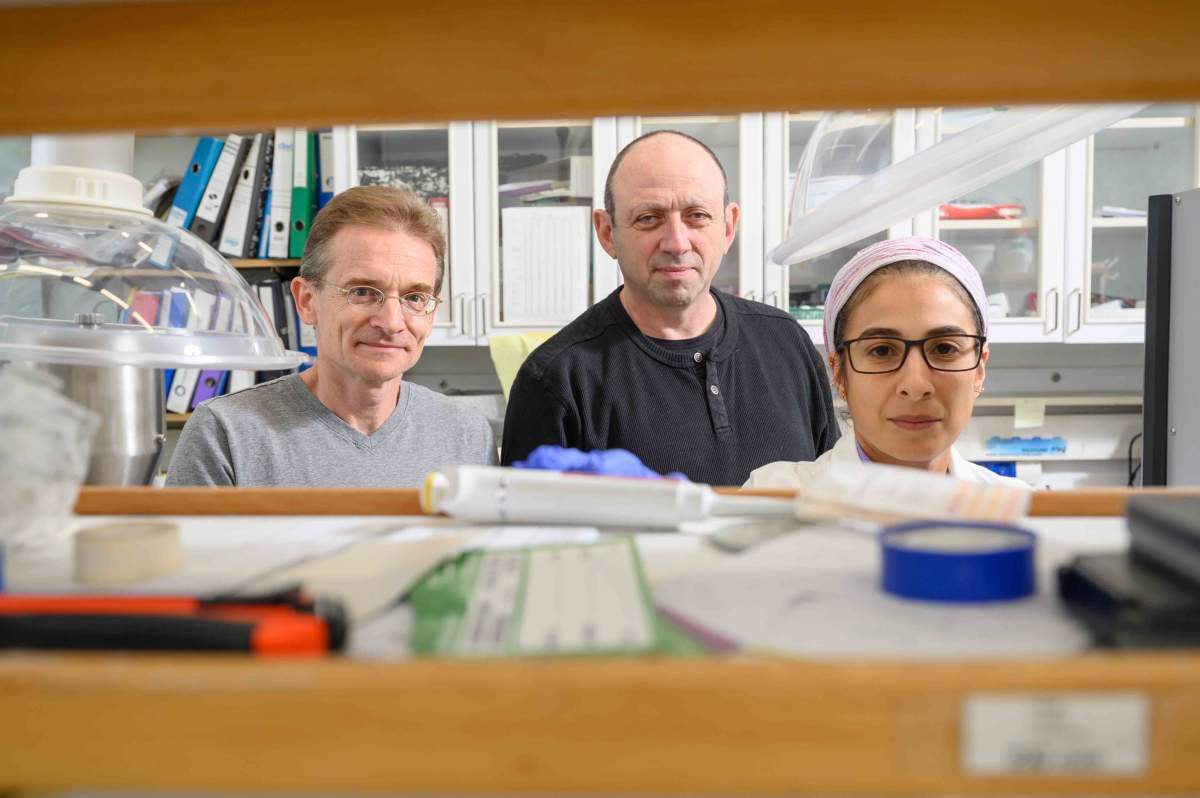
In a study published in ACS Nano, Dr. Angelica Niazov-Elkan, Dr. Haim Weissman and Prof. Boris Rybtchinski of the Molecular Chemistry and Materials Science Department at the Weizmann Institute of Science have created a new composite plastic that degrades easily using bacteria. This new material, produced by combining a biodegradable polymer with crystals from a biological substance, has three major benefits: It is cheap, easy to prepare and very strong. Also participating in the study were the late Dr. Eyal Shimoni, Dr. XiaoMeng Sui, Dr. Yishay Feldman and Prof. H. Daniel Wagner.
Currently, many industries are enthusiastically adopting composite plastics, which are made by combining two or more pure materials and possess the various beneficial properties such as lightness and strength. These plastics now serve to manufacture key parts of a wide variety of industrial products, from airplanes and cars to bicycles.
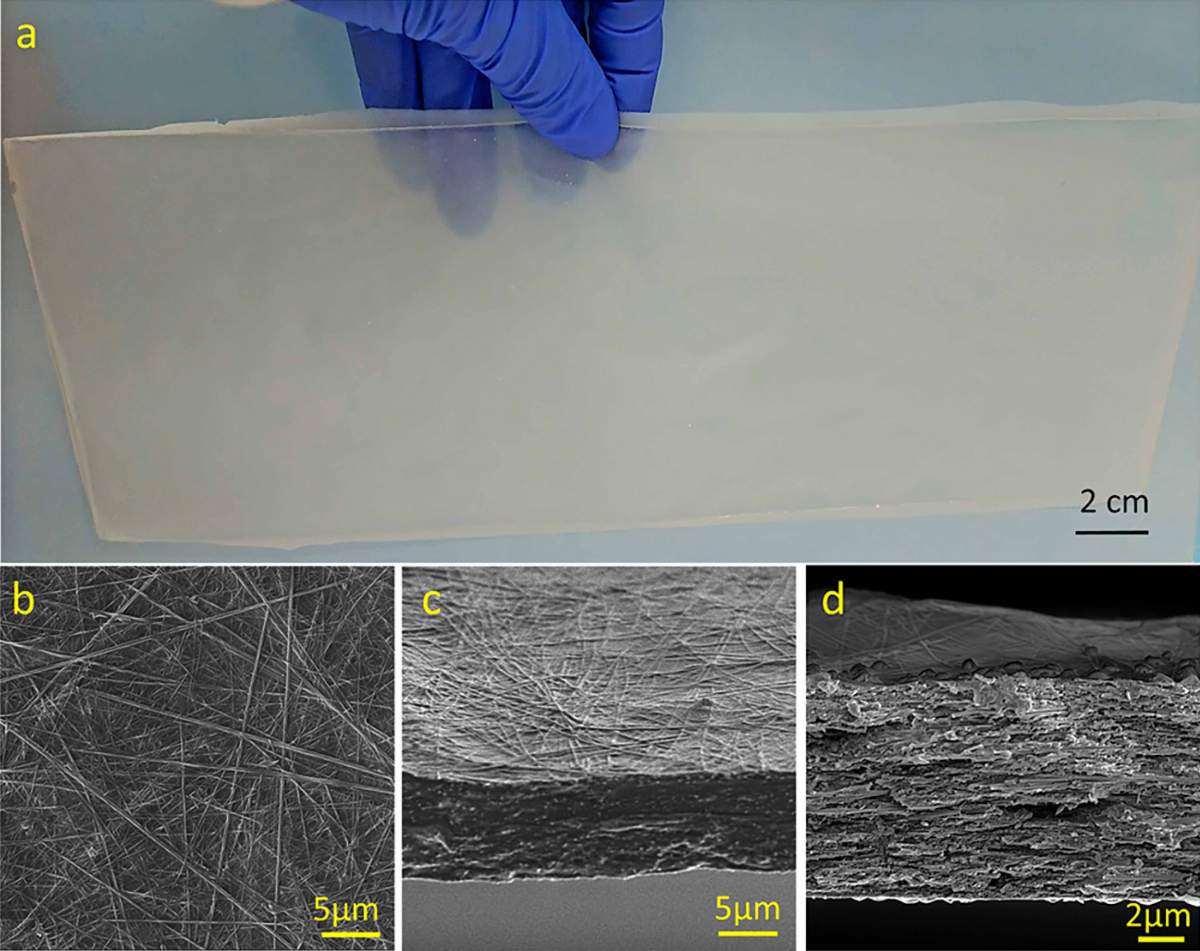
Seeking to create a composite plastic that would meet the needs of industry while also being environmentally friendly, the Weizmann researchers decided to focus on commonplace, inexpensive source materials whose properties could be improved. They found that molecules of tyrosine - a prevalent amino acid that forms exceptionally strong nanocrystals - could be used as an effective component in a biodegradable composite plastic. After examining how tyrosine combines with several types of polymers, they chose hydroxyethyl cellulose, a derivative of cellulose, which is employed extensively in the manufacture of medicines and cosmetics.
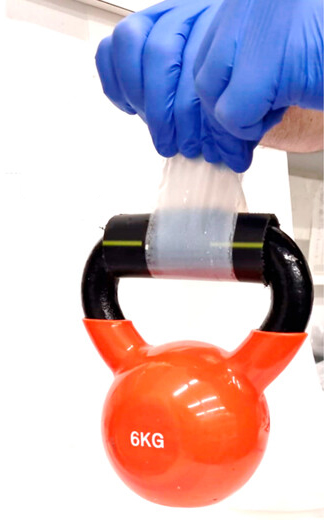
On its own, hydroxyethyl cellulose is a weak material that disintegrates readily. To combine it with tyrosine, the two materials were mixed together in boiling water. When they cooled and dried, an exceptionally strong composite plastic was formed, made of fiber-like tyrosine nanocrystals that grew into the hydroxyethyl cellulose and integrated with it. In one experiment that revealed the new plastic's strength, a 0.04-millimeter-thick strip of the material withstood a load of 6 kilograms. Moreover, the team discovered that the new material had several other unique characteristics, making it even more useful for industry. Usually, when a material is strengthened, it loses plasticity. This new composite plastic, however, in addition to being very strong, is also more ductile (malleable) than its core component, hydroxyethyl cellulose. In other words, combining the two materials created a synergy that manifests itself in the emergence of extraordinary properties and, consequently, has massive industrial potential.

Since both cellulose and tyrosine - the crystals of which can be found in various types of hard cheese - are edible, the biodegradable composite plastic can actually be eaten. Is it also tasty? We will have to wait to find out: Since the production process in the lab is not hygienic enough for foodstuffs, the researchers are yet to have a nibble.

Science Numbers
According to the United Nations Environment Programme, humans produce about 400 million tons of plastic waste every year.
Rybtchinski sums up: "The follow-up study that we have already started could advance the commercial potential of this new material, since we have replaced the boiling in water with melting, as is more common in industry. This means that we heat up the biodegradable polymers until they become liquid and then mix in the tyrosine or other suitable materials. If we manage to overcome the scientific and technical challenges involved in this process, we will be able to explore the possibility of producing this new composite plastic on an industrial scale."
Prof. Boris Rybtchinski's research is supported by the Tom and Mary Beck Center for Advanced and Intelligent Materials and the Wolfson Family Charitable Trust & the Wolfson Foundation.