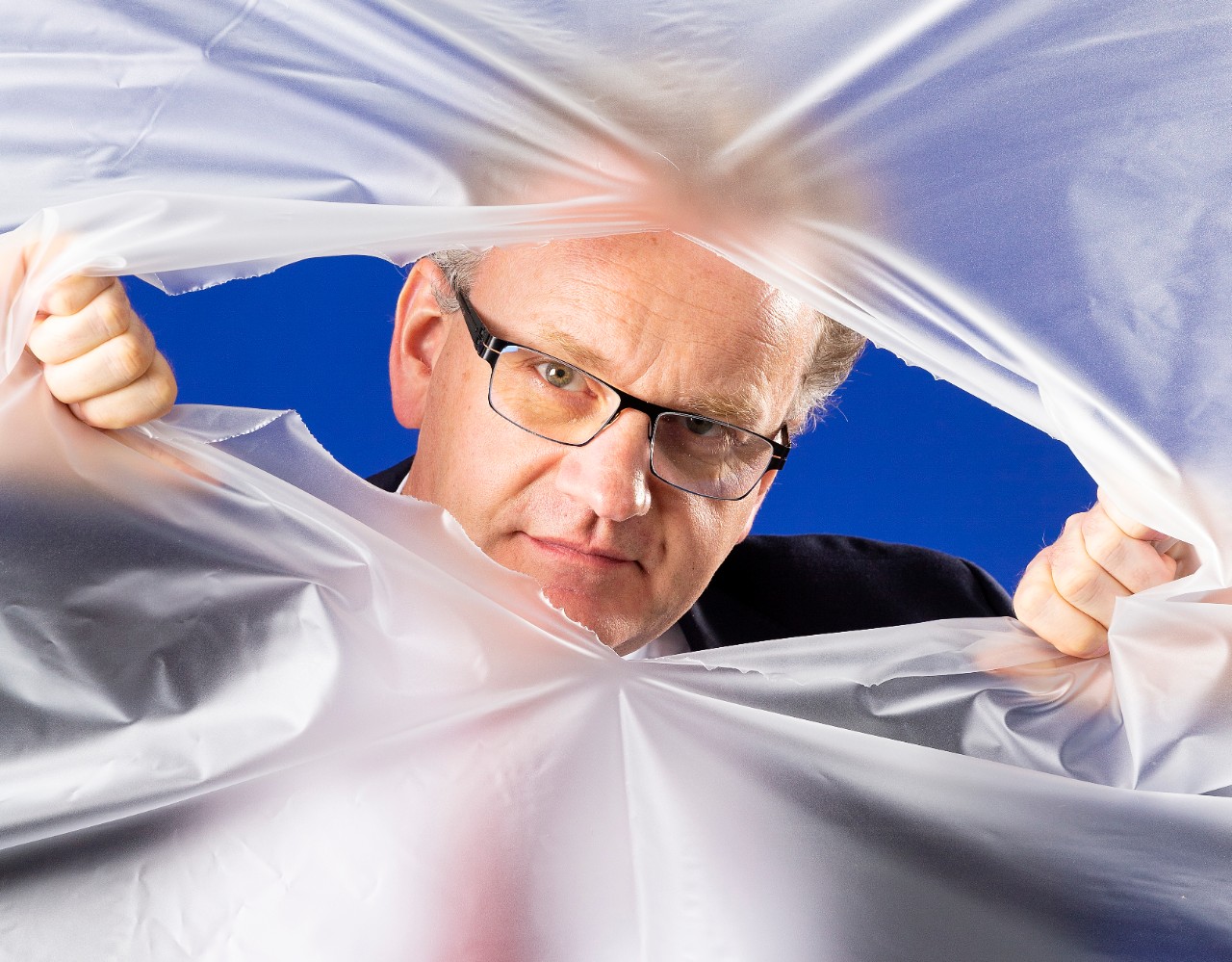
Finding new insights into how the world works has always excited Professor Thomas Maschmeyer, "I ask myself: what are fundamental scientific issues preventing us from solving these problems?"
Perhaps the only time Professor Thomas Maschmeyer (BSc(Hons) '91 PhD '95) doesn't have his head full of research questions is when he's mountain biking. "Trying not to come off a mountain bike as you scream down a hill is a pretty good way to keep your mind away from work," he says.
Maschmeyer's work is both fascinating and important. One aspect is based on a distressing premise: there are beaches in the world where no human has ever set foot that are covered in our garbage.
Most of it is plastic that spews from the rivers where it's been dumped, often on an industrial scale. If you think things are bad now, it's estimated that by 2050, there will be more weight of plastic in the oceans than fish.
But this article isn't about the problem of plastic waste. It's about a potential technological solution, which is already leading to the construction of a new kind of plastic recycling plant in the UK.
The technology is based on what's called a catalytic hydrothermal reactor (Cat‐HTR), an idea originated by Maschmeyer and developed through his start‐up company, Licella. The process was and continues to be strongly supported by the University of Sydney and a highly skilled team of academics, scientists, engineers and entrepreneurs.
"People are excited by work that could make a real difference," says Maschmeyer. "With my students, sometimes we have to tell them to go home because they're working too much."
What makes the Cat‐HTR process exciting isn't that it can recycle plastic. It's that it can recycle mixed plastics, often referred to as contaminated, end‐of‐life plastics. This is the material the Chinese recycling industry no longer accepts from the rest of the world because it is so hard to deal with.
To understand why mixed plastics are difficult to recycle, it helps to understand some basics about plastic itself.
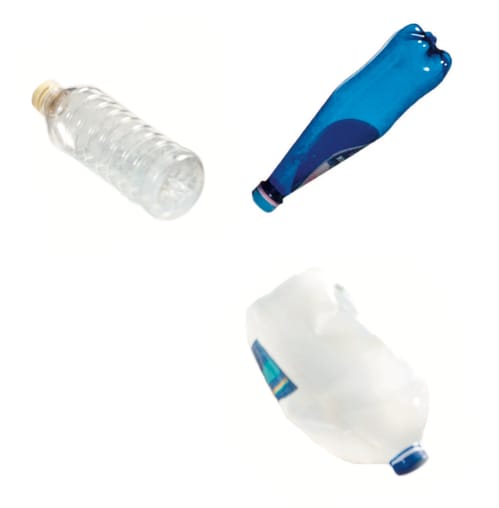
The starting point for most plastic is crude oil, which is rich in carbon atoms linked as rings and chains. Each of the carbon atoms is connected to one or more hydrogen atoms. Collectively, these molecules are called hydrocarbons.
When the bonds between the carbon atoms or between the carbon and hydrogen atoms are broken, radicals are generated. By their nature, these radicals are exceptionally eager to bond with other molecules.
On the plus side, inventing new ways for these hydrocarbons to break and recombine has led to the dizzying array of fuels, chemicals and materials that underpin much of modern life, including a huge range of plastics with qualities like transparency, opaqueness, rigidity, squeezability, toughness, delicacy and all the other features that make plastic so endlessly useful.
Imagine if all our containers were still made of glass, pottery or metal. And how would electricity work if there were no non‐conductive plastics?
Now the downside. In conventional, ie, mechanical recycling, plastics can only be processed with other waste made of the same or very well‐defined mixtures of plastic. Using unsorted, random compositions of plastics gives unpredictable results, producing materials of no use to anyone.
That's why plastics are sorted strictly into their six classes for recycling, and why most contaminated, end‐of‐life plastic, which makes up about 50 percent of the world's waste plastic, is burned, sent to landfill or indeed dumped into rivers. Things would be so much easier if all types of plastic could be recycled together using a chemical route.
The questions has always been: how? For Maschmeyer, the answer is water.
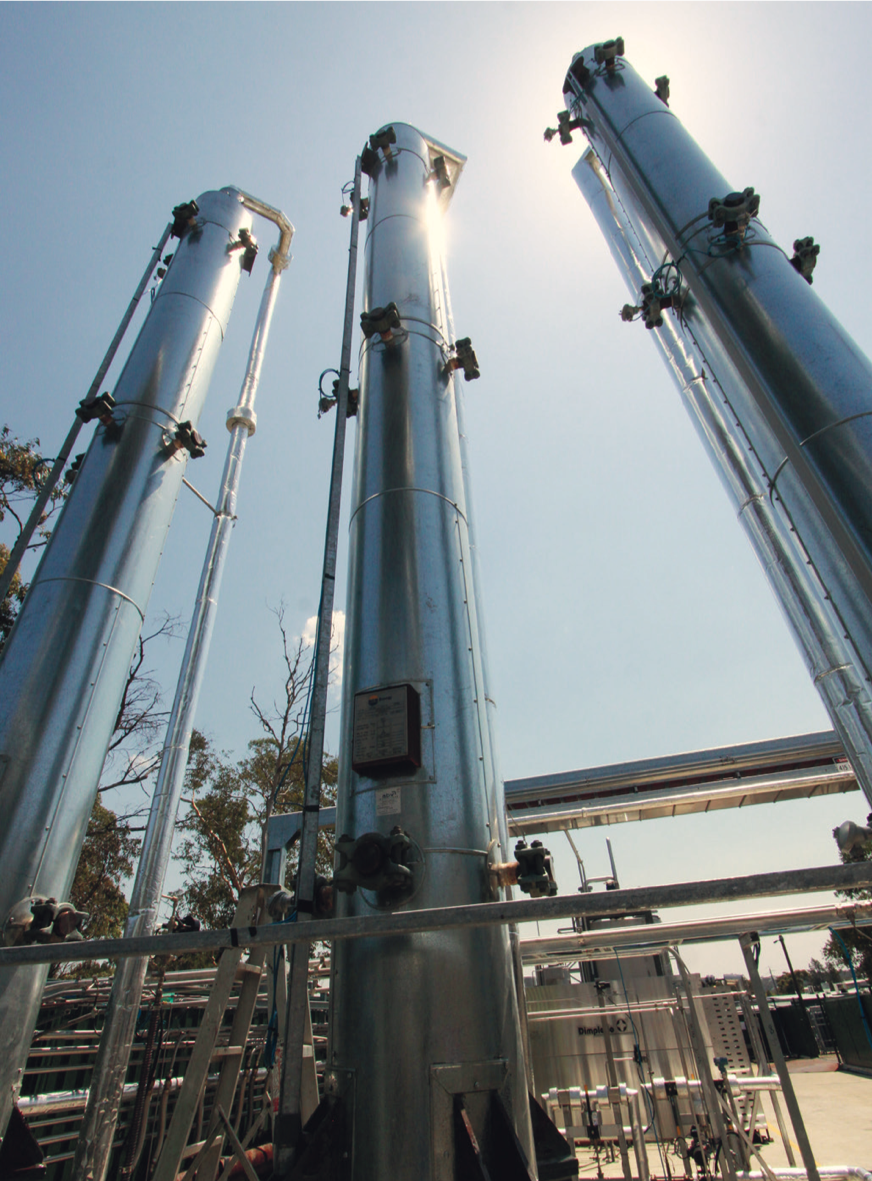
For more than 10 years, this has been the world's only large scale Cat-HTR plant. Located on the New South Wales Central Coast, what was learned here will underpin future international plants.
As Cat‐HTR Technology breaks plastics down into smaller hydrocarbon components, the system uses water and a mix of catalysts to prevent the intermediate radicals from reacting with each other. The resulting liquid is a stew of stable, distillable molecules that can be easily separated into high value components, ready for reuse.
Of all the current recycling methods, this ease of distillation – enabled by Cat‐HTR's stable product mix – makes the process uniquely efficient.
Maschmeyer's method also transforms waste plastic in another hugely significant way.
By converting it into saleable products like waxes, lubrication oils, fuels and gases, which can be used to make new plastics, the waste plastic itself is given monetary value. As Maschmeyer says, "Once you give something value, people look after it. They don't toss it into rivers; they'll try and do something with it."
Considering the sheer volume of waste plastic choking the world that can now be monetised, it's not surprising Maschmeyer's work has attracted commercial interest. The plant in the UK is being built through an infrastructure investor, Armstrong Energy, and when it comes online, it will convert 20,000 tonnes of waste plastic annually.
And that's only the beginning. Oil multinationals have expressed strong interest in the oil products the process can produce, and partnerships are being negotiated for more and bigger plants to open around the world, with the Finnish multinational and renewables leader, NESTE Oil, being the first official partner.
It's an amazing place to be for Maschmeyer, especially considering where he started.
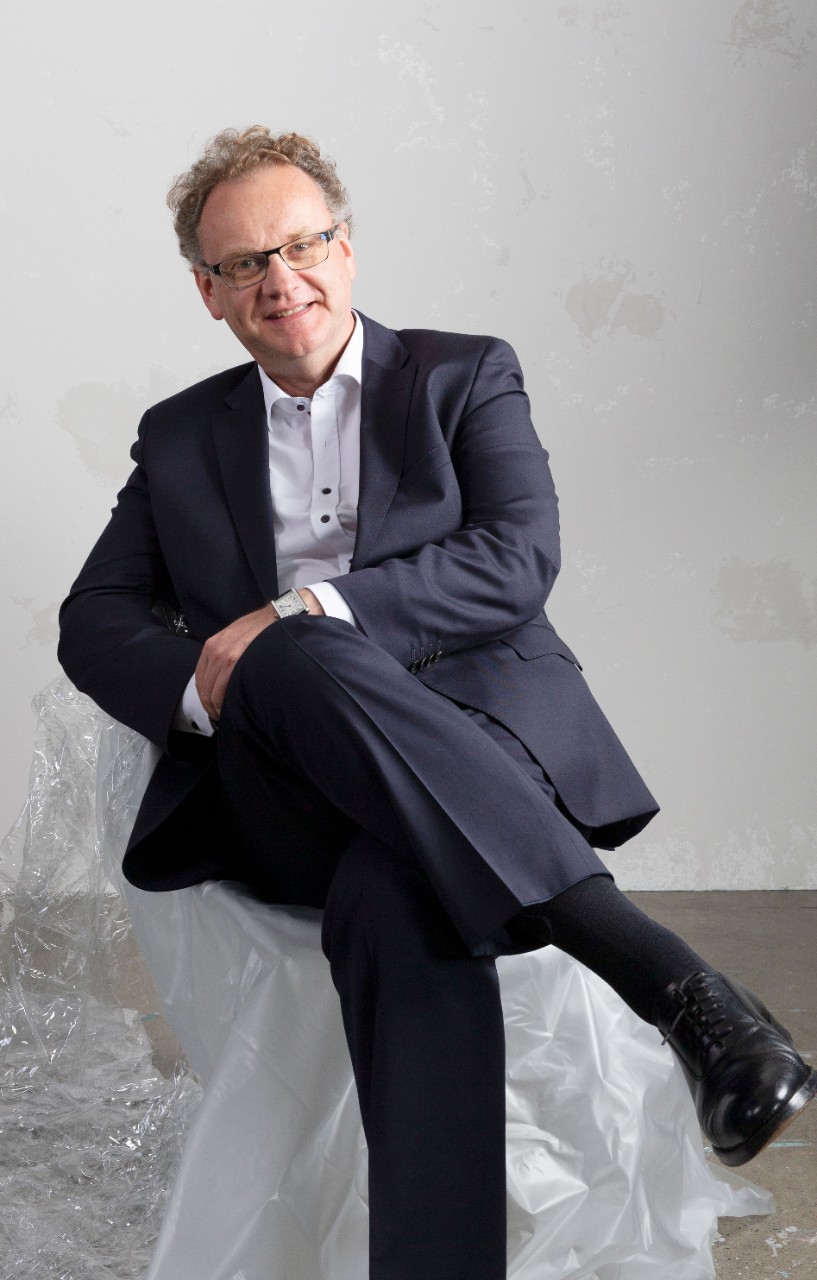
"People realise plastics are entering the food chain and we have a substantial problem," says Maschmeyer.
Growing up in what was then the rough side of post‐Second World War Hamburg, Maschmeyer was the only youngster in his street to finish 'Gymnasium', Germany's senior‐tier of schooling, topping most years. Following his Australian wife to Sydney, he started a double degree at the University of Sydney in science and engineering, later focusing entirely on science.
After his PhD, Maschmeyer worked in London, then Cambridge. He progressed quickly, which he credits to his Lutheran world view and protestant work ethic. By the age of 31 he was in the Netherlands and Head of the Department of Applied Organic Chemistry and Catalysis at the Delft Institute of Chemical Technology. He became Vice Chair of the whole institute a couple of years later.
Missing the hands‐on research he had enjoyed before his appointment to these senior roles, he decided to return to Sydney as a Federation Fellow.
"Also the kids started to support Dutch soccer teams. I had to put a stop to that," he says laughing.
He hasn't fully avoided senior university postings (until recently he was the Founding Director of the University of Sydney's Nano Institute), but he now happily runs a research team, doing work that just earned him the "Australian Science Oscar" – the 2018 Eureka Prize.
"I have around 15 students doing work in all sorts of areas," he says. "I think I'm quite good at spotting talent and getting people hooked on a particular journey. And of course, if they're successful, I'm successful. So, it's enlightened self‐interest, really."
With the Cat‐HTR initiative well underway, Maschmeyer is pursuing numerous other high‐impact projects. His current research focus is on another revolutionary technology – a new generation of batteries for storing renewable energy. But that's a whole other story.
Discover more research
Professor Thomas Maschmeyer's research into chemical recycling is only one element of his work. Find out more about his research into nanoscale battery technology here.
Written by George Dodd
Photography by Louise Cooper