ETH researchers have modified certain bacteria with UV light so that they produce more cellulose. The basis for this is a new approach with which the researchers generate thousands of bacterial variants and select those that have developed into the most productive.
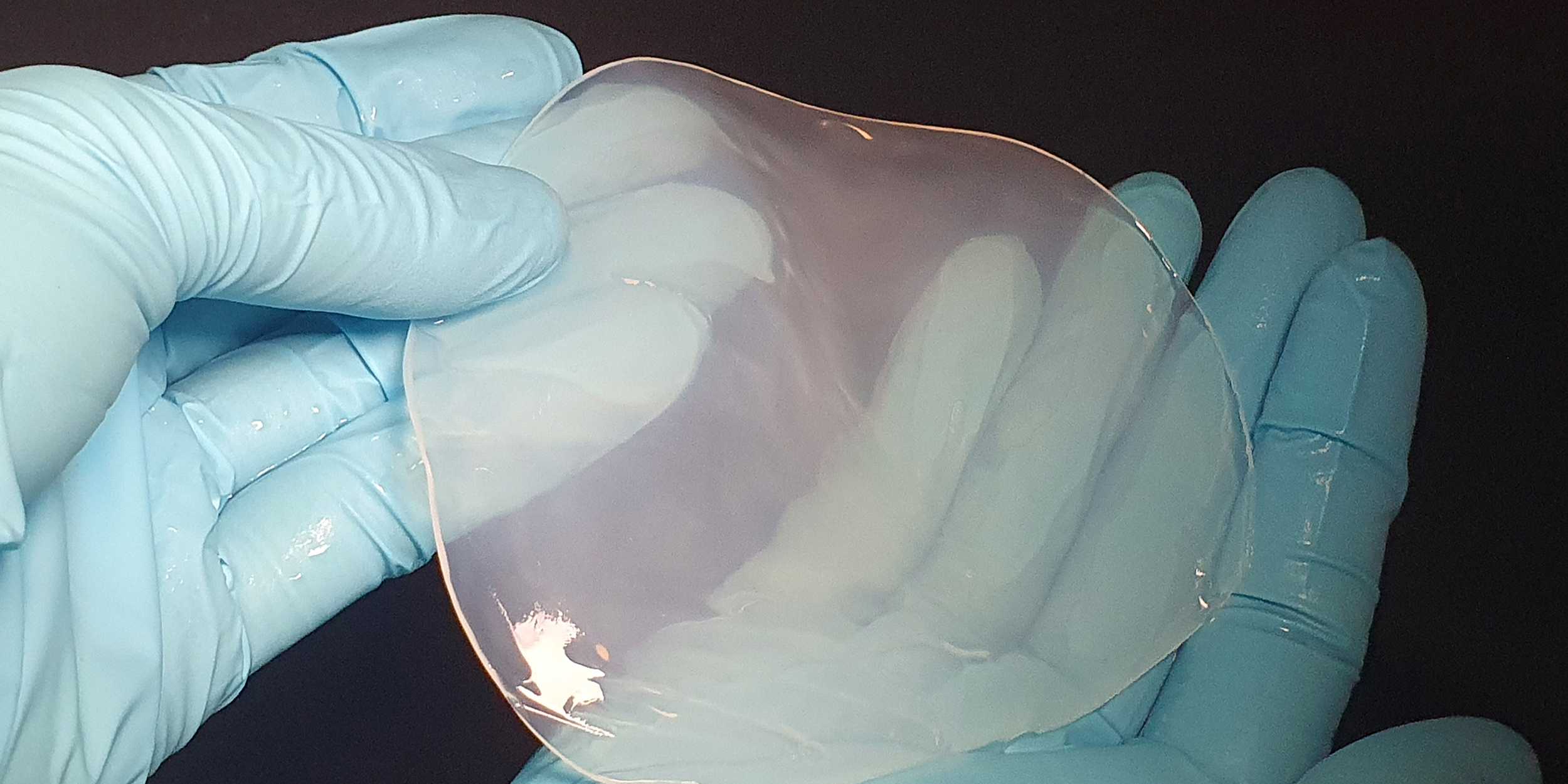
In brief
- Materials researchers at ETH Zurich have created 40,000 variants of the cellulose-producing bacterium Komagataeibacter sucrofermentans.
- Among them were four that produce up to seventy percent more cellulose than those in their original form.
- The researchers achieved this using a new approach developed specifically for this purpose, which they have patented.
- Cellulose is a much-sought-after raw material for food, textile and biomedical applications, for example.
Bacteria produce materials that are of interest to humans, such as cellulose, silk and minerals. The advantage of producing bacteria in this way is that it is sustainable, takes place at room temperature and in water. A disadvantage is that the process takes time and gives rise to quantities too small to be of industrial use.
Consequently, researchers have for some time been trying to turn microorganisms into living mini-factories that can produce larger quantities of a desired product more quickly. This requires either targeted intervention in the genome or the cultivation of the most suitable bacterial strains.
A new approach is now being presented by the research group led by André Studart, Professor of Complex Materials at ETH Zurich, using the cellulose-producing bacterium Komagataeibacter sucrofermentans. Following the principles of evolution by natural selection, the new method allows scientists to produce tens of thousands of variants of the bacterium very quickly and to select those strains that produce the most cellulose.

K. sucrofermentans naturally produces high-purity cellulose, a material that is in great demand for biomedical applications and the production of packaging material and textiles. Two properties of this type of cellulose are that it supports wound healing and prevents infections. "However, the bacteria grow slowly and produce limited amounts of cellulose. We therefore had to find a way to boost production," explains Julie Laurent, a doctoral student in Studart's group and first author of a study that has just been published in the scientific journal PNAS.
The approach she developed has succeeded in producing a small number of Komagataeibacter variants that generate up to seventy percent more cellulose than in their original form.
Accelerating evolution with UV light
The materials researcher first had to create new variants of the original bacterium that occurs in nature - known as the wild type. To do this, Julie Laurent irradiated the bacterial cells with UV-C light, which damages random points of the bacterial DNA. She then placed the bacteria in a dark room to prevent any repair of the DNA damage and to thereby induce mutations.
Using a miniature apparatus, she then encapsulated each bacterial cell in a tiny droplet of nutrient solution and allowed the cells to produce cellulose for a specific length of time. After the incubation period, she used fluorescence microscopy to analyse which of the cells had produced a lot of cellulose and which had produced none or very little.
By means of a sorting system developed by the group of ETH chemist Andrew De Mello, Studart's team automatically sorted out those cells that had evolved to produce an exceptionally large amount of cellulose. This sorting system is fully automated and very fast. In a matter of minutes, it can scan half a million droplets with a laser and sort out those containing the most cellulose. Only four remained that produced 50 to 70 percent more cellulose than the wild type.
The evolved K. sucrofermentans cells can grow and produce cellulose in mats in glass vials at the interface between air and water. Such a mat naturally weighs between two and three milligrams and is about 1.5 millimetres thick. The cellulose mats of the newly evolved variants are almost twice as heavy and thick as the wild type.
Julie Laurent and her colleagues also analysed these four variants genetically to find out which genes had been altered by the UV-C light and how these changes had led to the overproduction of cellulose. All four variants had the same mutation in the same gene. This gene is the blueprint for a protein-degrading enzyme - a protease. To the materials researcher's surprise, however, the genes that directly control cellulose production had not changed. "We suspect that this protease degrades proteins that regulate cellulose production. Without this regulation, the cell can no longer stop the process," the researcher explains.
Patents pending
The new approach is versatile and can be applied to bacteria that produce other materials. Such approaches were originally developed to create bacteria that produce certain proteins or enzymes. "We are the first to use such an approach to improve the production of non-protein materials," ETH Professor André Studart says. "For me, this work is a milestone."
The researchers have applied for a patent for the approach and mutated bacterial variants.
In a next step, they would like to collaborate with companies producing bacterial cellulose to test the new microorganism in real industrial conditions.
Reference
Laurent JM, Jain A, Kan A, Steinacher M, Enrriquez Casimiro N, Stavrakis S, deMello AJ, Studart AR: Directed Evolution of Material-producing Microorganisms. PNAS, July 23, 2024, 121 (31) e2403585121, doi: external page10.1073/pnas.2403585121