Credit: ORNL, U.S. Dept. of Energy
It's a safe bet that lightning is going to strike twice around Vipin Kumar.
In fact, he makes sure it does - every time he tests new technology to protect sky-high wind turbine blades. As a researcher at the Department of Energy's Oak Ridge National Laboratory, Kumar has brainstormed a series of technologies to prevent lightning damage to the composites used in renewable energy turbines and airplanes.
Kumar and a team of ORNL researchers reached a significant milestone by building an entire 6.5-foot turbine blade tip using novel materials. The team then tested it against the forces of simulated lightning in a specialized lab at Mississippi State University, where the blade tip emerged pristine after tests that isolate the effects of high voltage. Separate tests in the same lab found that isolated high current remained destructive. But Kumar is striking back with further innovations. ORNL's recent demonstration highlighted the possibilities of a new approach to protecting blades using conductive materials or coatings.
Although lightning often hits wind turbines, its broader impact on the wind industry remains unclear. Lightning strikes to turbine blades are frequent but rarely catastrophic. They can nevertheless weaken blades with internal damage that translates to increased repair costs over time. For example, lightning strikes are the second leading cause of blade-related downtime, Kumar said.
"We don't have enough data to know the true scope of the challenge, but we know it's a concern to industry and utilities," Kumar said. "We know wind energy is a reliable source of electricity that supports energy security, but I believe anything we can do to make it more resilient and reliable is important."

The project combined Kumar's expertise in composites with ORNL's unique capabilities in carbon fiber. A composite is a material that combines polymers with strong fibers, such as fiberglass or carbon fiber, to create a rigid, lightweight material. The blade tip, made at ORNL in DOE's Carbon Fiber Technology Facility, incorporated two layers each of standard glass fiber and a low-cost carbon fiber developed at the lab. In this case, customized conductive carbon fiber is key to dispersing electrical energy across the blade surface.
Researchers used industry-standard equipment and methods to show the technology can be easily integrated with established manufacturing processes, Kumar said. The research is funded by the Advanced Materials and Manufacturing Technologies Office within DOE's Office of Energy Efficiency and Renewable Energy.
The cost of carbon fiber has generally limited its use to the wind blade's load-bearing structure, called a spar cap. But ORNL's efforts to lower the cost of carbon fiber may make it economical to replace glass fibers in the blade tip, where lightning strikes most often.
"This is a stepping stone in the right direction," said Merlin Theodore, who leads the Advanced Fiber Manufacturing group at ORNL. "We were happy to show this could be done at scale. Although there is more work to be done, this shows that carbon fiber has a more significant role to play in wind energy applications."
ORNL's turbine blade tip, which is fully recyclable, supports the wind industry's push toward greater sustainability. The project recently won a prestigious ACE award for Composites Excellence in the category of "innovation in green composites design" from the American Composites Manufacturers Association.
"We have a plan to show the complete recyclability of this blade by reusing the carbon fiber and reusing the resin for 3D printing in the Manufacturing Demonstration Facility at ORNL," Kumar said.
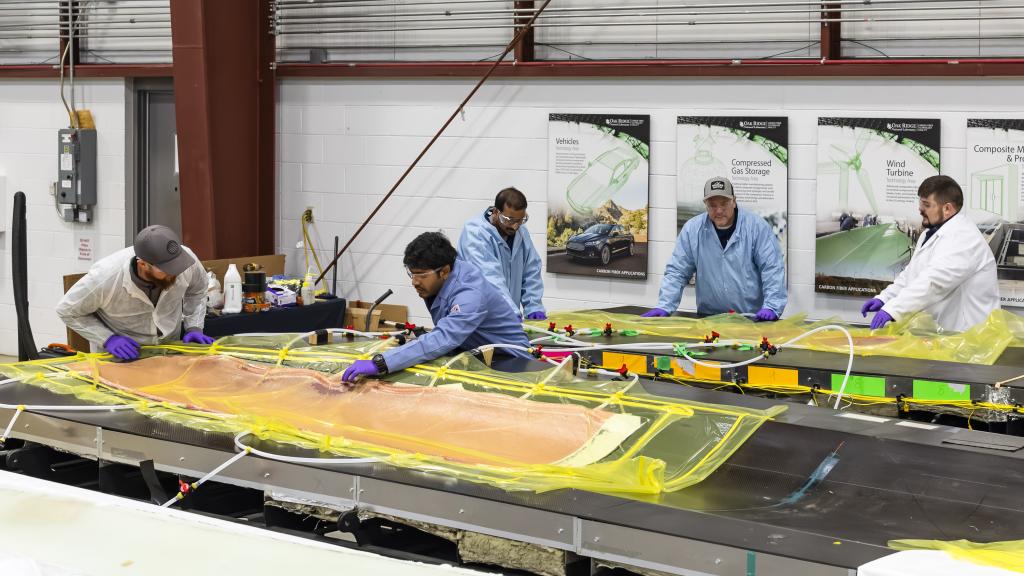
An electrifying career
Kumar's career, which began in 2018 with postdoctoral research at ORNL, has been a relentless search for ways to protect airplanes, drones and wind turbines from lightning that threatens structural integrity and reliable electricity. "I'm trying to save anything in the sky made of a composite from lightning damage," he said.
The strength of carbon fiber makes it the exclusive choice for airplane composites, but carbon composites are semi-conductive. "To protect composites from lightning damage, you have to actually increase its conductivity," Kumar said. "You cannot rely on insulating it or directing lightning to specific locations."
The wind industry has tried that approach by using a metallic receptor attached to a rod in the blade, like a lightning rod under the surface, to transport electricity to the ground. However, the rod doesn't always draw the current when lightning strikes the composite material, Kumar said. "While other wind turbine technologies have evolved significantly in recent decades, the industry's approach to lightning strike protection has not advanced as quickly," he said.
For increasing conductivity, Kumar has used different materials, such as a conductive external coating or a matrix of carbon nanofillers , to create a conductive "skin" that dissipates energy, preventing burning or interior damage at the strike point.
Kumar's experiments, each tested in a lightning lab, produced continuous improvements that culminated with a compression-molded composite using many layers of low-cost carbon fiber. "I didn't expect it to perform as well as it did," Kumar said. "I tested it against five lightning strikes that were six times stronger than the average bolt: No damage. I started scratching my head, asking why."
Kumar learned that ORNL's carbon fiber could be customized for greater conductivity, inspiring him to test it in an entire blade tip.
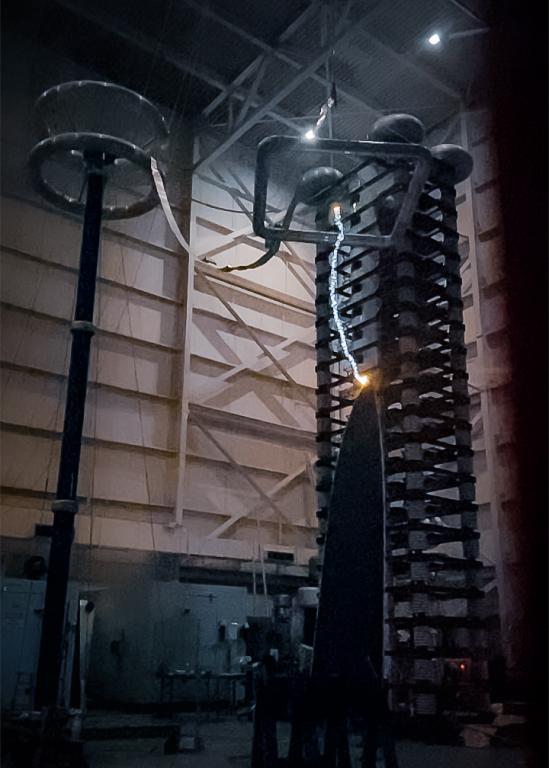
Meeting future wind generation needs
Demand for carbon fiber, a mainstay of the aerospace industry, is expected to outpace supply within five years, further driving up its cost. ORNL's more economical formulation could enable the wind industry to afford to compete for the material, said ORNL researcher Subhabrata Saha, who led creation of the blade tip. "It can help match today's cost while providing higher strength per weight of the blade," he said.
The hybrid carbon fiber composite blade tip is 41% lighter than a blade tip made with pure glass fibers, Kumar said. "That means we can make bigger blades of the same weight that generate more electricity," he said.
Doubling the length of a turbine blade allows it to generate four times more power , leading to blades that are sometimes over a football field long. This significant size increase allows for more energy output from modern wind turbines. "But the larger the blade, the larger the chance it will be hit by lightning," Kumar said.
With so many turbines under construction, it's urgent to ensure their durability and efficiency with effective lightning protection. "It's exciting, but more importantly, it's needed," Theodore said. "Carbon fiber makes it much easier to extend the length of turbine blades."
Theodore said ORNL is translating foundational science for commercial application. "We have the whole research supply chain here: We are unique in that we can make the fiber as well as the prototype blade within our ecosystem. That's what I call quickly scaling up science."
The blade and a set of smaller composite panels, created simultaneously from the same material, underwent separate tests for voltage and current to simulate lightning's destructive forces. Current is the rate at which electricity flows, and voltage is essentially the force that drives the electricity between two points. High-voltage tests are used to understand the lightning attachment entry and exit locations, while the resistive heat of high-current tests is more destructive to the composite laminate.
Kumar's team then utilized ultrasonic imaging to assess any damage to the material. The full wind blade tip emerged pristine from high-voltage bolts of electricity but did not hold up as well to blasts of intense current. However, the prototype sample panels suffered no visible or internal damage and retained their mechanical properties - a technological first that demonstrated "remarkable resilience" to lightning strikes, Kumar said. The same test blasted a hole in a panel made with standard commercial carbon fiber.
What comes next
Why did the ORNL test panels perform better than the full blade tip, despite being made of the same material? One potential cause is that the panels were compression-molded, which created a higher volume of carbon fiber in the composite. They were also heat-cured, a common practice in the wind industry, while the blade tips were allowed to set at room temperature. Heat-curing improves the material by using heat to strengthen its structure and enhance its thermal properties and performance.
But Kumar isn't counting on an easy solution. Because the resin makes up the largest portion of the blade tip, he wants to experiment with using a more conductive resin.
An affordable, versatile coating can be made from the nanofillers in polymer. Even without the carbon fiber, panels with this coating performed extremely well in recent voltage and current tests, Kumar said.
Kumar explored the economic viability of his research as part of DOE's 2024 Energy I-Corps program , which helps national laboratory scientists identify pathways for bringing their innovations to market. Through an I-Corps project funded by DOE's Wind Energy Technologies Office, Kumar interviewed 82 wind industry professionals, including turbine blade manufacturers, wind farm operators and blade repair companies, to learn more about their challenges and what solutions they'd embrace. His nanofiller coating sparked the most interest. Kumar is talking with potential industry partners about field-testing it at a wind farm where its effectiveness can be monitored over time.
Wind farm operators are eager for options, given repair costs for lightning damage range from $10,000 to $100,000 for onshore blades and up to $1 million for replacing a damaged turbine blade off the coast, Kumar said. Insurance companies and equipment manufacturers often decline to cover costs, labeling turbine lightning damage an exempt "Act of God."
But Kumar is confident: "It's an act of engineering."
UT-Battelle manages ORNL for the Department of Energy's Office of Science, the single largest supporter of basic research in the physical sciences in the United States. The Office of Science is working to address some of the most pressing challenges of our time. For more information, please visit energy.gov/science .