Abstract
A breakthrough in hybrid patch technology promises to prevent cracks while maintaining robust adhesion without the use of chemical adhesives. This innovation is anticipated to drive advancements in wearable devices, virtual reality (VR) equipment, and the healthcare industry.
The research team, led by Professor Hoon Eui Jeong from the Department of Mechanical Engineering at UNIST, has developed a 'programmable meta patch' technology that effectively prevents cracking over both small and large areas. This technology allows for attachment in specific directions, while maximizing adhesion strength.
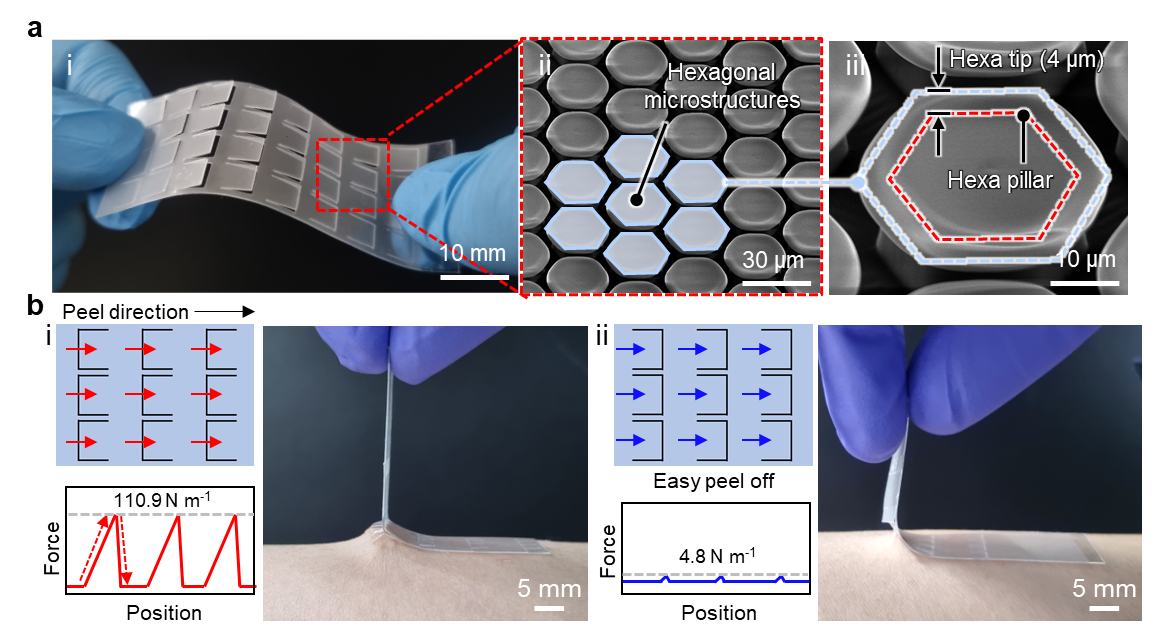
Figure 1. Fabrication of crack-trapping hybrid adhesive patch.
These hybrid patches exhibit adhesion that is 70 times stronger than conventional adhesives through the incorporation of hexagonal pillars, tip structures, and nonlinear cutting designs. Since they do not rely on chemical adhesives, they minimize skin irritation and can be reused. They provide effective crack prevention across a range of surface sizes, from micro-scale to macro-scale.
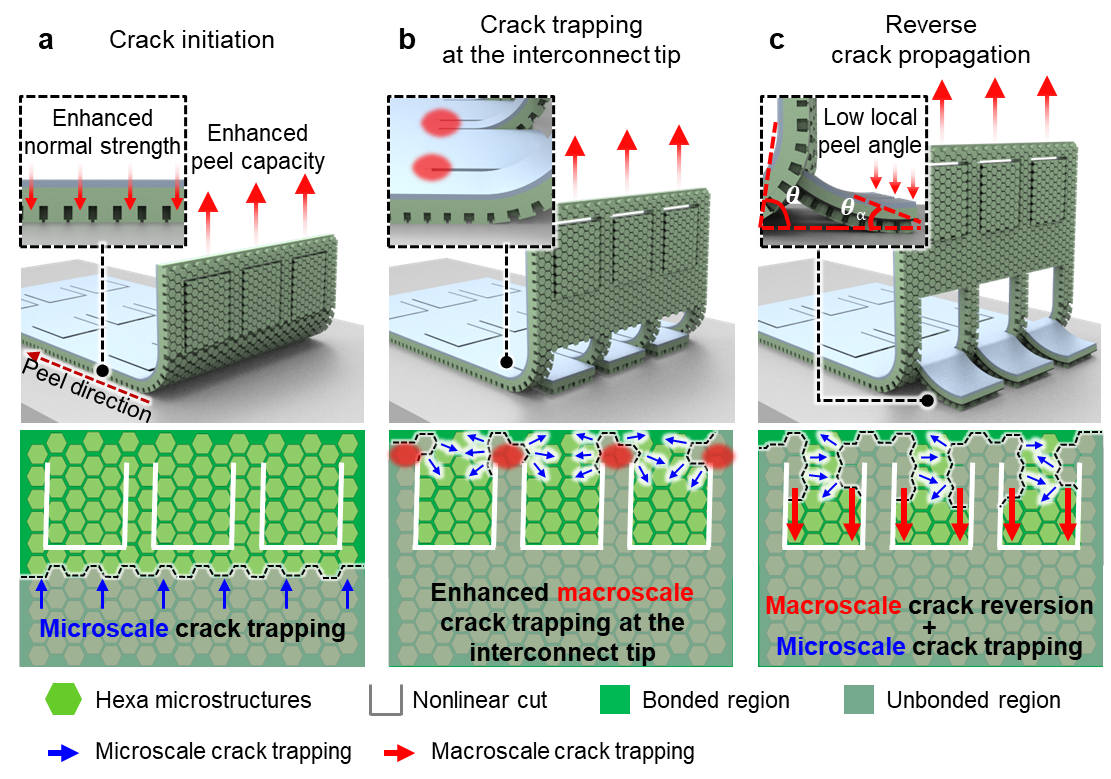
Figure 2. Design of crack-trapping hybrid adhesive patch.
The adhesive patch features a nature-inspired design combined with a kirigami-inspired metastructure, enabling both the strength and direction of adhesion to be adjusted as necessary. While adhesion varies by direction, this adaptability ensures efficient attachment only where needed.
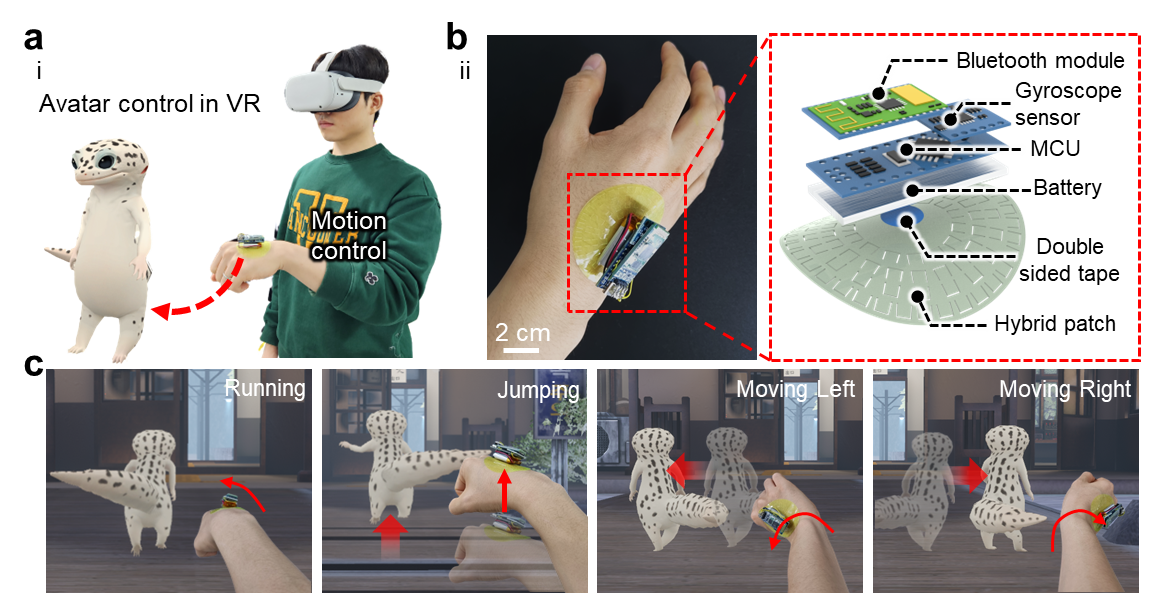
Figure 3. Application of the hybrid adhesive patch.
"Existing skin adhesion technologies in bio-healthcare and wearable devices often cause skin irritation due to chemical adhesives and are difficult to reuse," noted Professor Jeong. "Our reusable adhesion technology significantly reduces skin irritation by applying directional adhesion while maintaining strong adhesion."
Wearable VR devices utilizing these patches adhere securely from all directions while causing minimal irritation to the skin. They also boast high breathability, enhancing user comfort. This accomplishment in overcoming the limitations of existing skin adhesion technology has garnered attention in the biohealthcare sector.
The research findings were published in Science Advances on September 13 and were supported by the Ministry of Science and ICT (MSIT), the National Research Foundation of Korea (NRF), and the National Science Foundation of the United States.
Journal Reference
Seongjin Park, Dong Kwan Kang, Donghyuk Lee, et al., "Multiscale crack trapping for programmable adhesives," Sci. Adv., (2024).