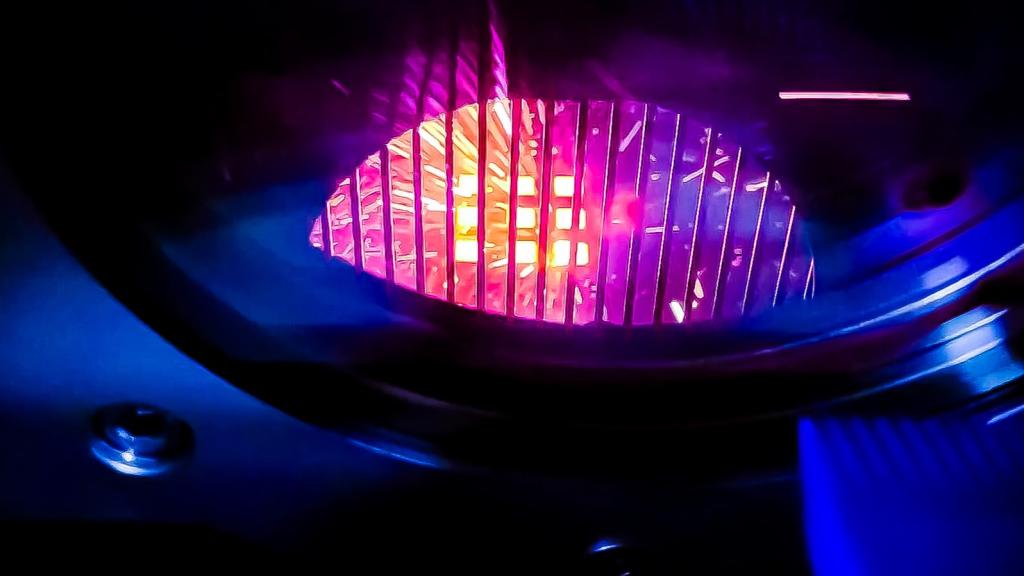
Researchers at Oak Ridge National Laboratory and the National Energy Technology Laboratory have developed and 3D printed the lightest crack-free alloy capable of operating without melting at temperatures above 2400 degrees Fahrenheit. This milestone could enable additively manufactured turbine blades to better handle extreme temperatures, reducing the carbon footprint of gas turbine engines such as those used in airplanes.
The latest significant advancement combines seven elements in a niobium-rich, complex concentrated alloy whose melting point is at least 48% higher than superalloys of nickel and cobalt previously developed at ORNL . Researchers fine-tuned the electron beam melting process to print test parts for the novel alloy.
"No one has been able to develop and print alloys with such a high melting temperature and low density without cracks before," said ORNL's Saket Thapliyal. While metals such as tungsten can take the heat, they would add too much weight to an airplane. "This is significant. We're making something lighter that can hold its structural integrity at ultra-high temperatures."