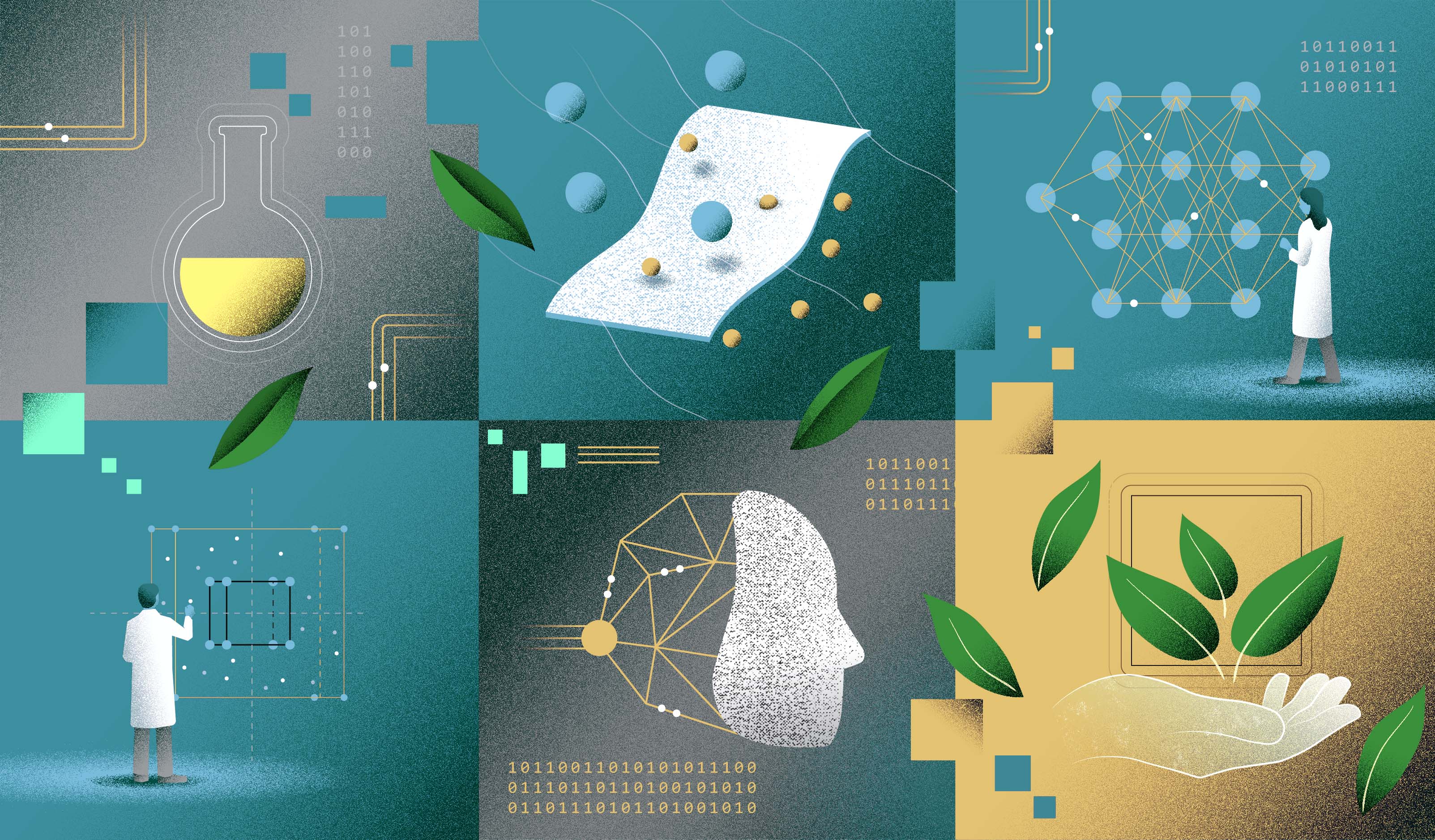
Composite illustration features science research themes. Artwork: Xavier Pita / KAUST
Two startling statistics drive the sustainable manufacturing research of Dr.Gyorgy Szekely, assistant professor of chemical engineering at the Advanced Membranes and Porous Materials Center.
The first is that less than 50 percent of the energy consumed by the chemicals-based manufacturing industry is actually used to make their products. Whether a commodity chemical, a polymer for a mobile phone component or a finely crafted pharmaceutical, most energy expenditure occurs in purifying or isolating the desired molecule from the complex mix that it was produced in. Traditional industrial separation techniques, such as distillation, are heat-driven processes that can consume vast amounts of energy when conducted on an industrial scale.
Szekely's research is focused on a technology that could slash that energy consumption by 90 percent. Replacing high temperature separations with selective porous membranes - to simply filter out the desired product at ambient temperature - can bring dramatic efficiency gains.
"Membrane processes use a fraction of the energy of conventional separation technologies," Szekely said.
Converting industry's energy-hungry heat-driven product separations into highly efficient membrane-based processes is a challenge Szekely first faced as a Ph.D. studying chemical engineering, specializing in pharmaceutical separations.
"I was part of a European program that brought together industrial and academic partners to try to deal with the product separation problems the industry was facing," he said.
His work has remained focused on industry problems, and some of his membrane separation projects are now in commercial use, but it's a slow process. Optimizing separation materials for a particular application involves simultaneously fine-tuning multiple material parameters; traditionally this has meant months of experiments in the lab. The cost of that approach is not just measured in time but in resource consumption and waste generation.
(From left to right) Drs. Gyorgy Szekely and Rifan Hardian conduct tests in the Advanced Membranes and Porous Materials Lab at KAUST. Photo: KAUST
"Developing new separation materials potentially creates more sustainability issues than it solves," Szekely said."What the field has struggled with for decades is a lack of organized and accessible data.The data problem doesn't allow us to take the next step and run separations much more efficiently."
The fragmented information generated for each project rarely allows generalized patterns to be discerned; yet these are needed to make accurate predictions for the next separation problem. Where data challenges have to date proven intractable to the human eye, he said that today new tools are available to look afresh and pick out patterns we cannot see.
"Artificial Intelligence is a new approach to tackling data problems," Szekely said. "In the past, AI needed large datasets - which we did not have - so there was no possibility of using it for separation technology. Now, based on recent advances in computer science, we can apply it to smaller experimental datasets and already do a lot."
From a few select experiments conducted in the lab, or from small preexisting datasets, machine learning can be applied to help connect the dots to develop or identify the ideal separation material and conditions for the task.
"For us to go to the lab and optimize manually would take ages, but if it is computer-based, we can do it in minutes or hours," he said.
For the membrane separations subfield of organic solvent nanofiltration, the Szekely group recently created an open-access database that anybody can use to help them with a separation problem.
"It is not only a database, we also provide a prediction tool based on machine learning algorithms," he added. "People can go online, draw in their molecules and then use the database and the AI to get the solution for their separation problem."
To put the new computational tool to the test, Szekely sought out a collaboration across the campus at KAUST. "I realized that we are not the only group at KAUST with the word 'sustainability' in the name," Szekely said. "Kyle Lauersen runs the Sustainable and Synthetic Biotechnology Group, so I contacted him to chat about what each of us was doing and how we could work together."
It turned out that Lauersen and his team had engineered algae for the sustainable bio-production of a pharmaceutical product, patchoulol, but had issues with isolating it. To develop a membrane-based process, the team plugged the problem into the Szekely group's online tool.
"The computer predicted that a membrane would retain 100 percent of the patchoulol, and when we tested that membrane, we measured 100 percent patchoulol recovery," Szekely said. "The AI was 100 percent accurate in a real-world problem."
Based on that result, Szekely now has a third compelling statistic to drive his sustainable manufacturing research forward.